「C3604加工のための最適な切削条件とは?詳細ガイド」
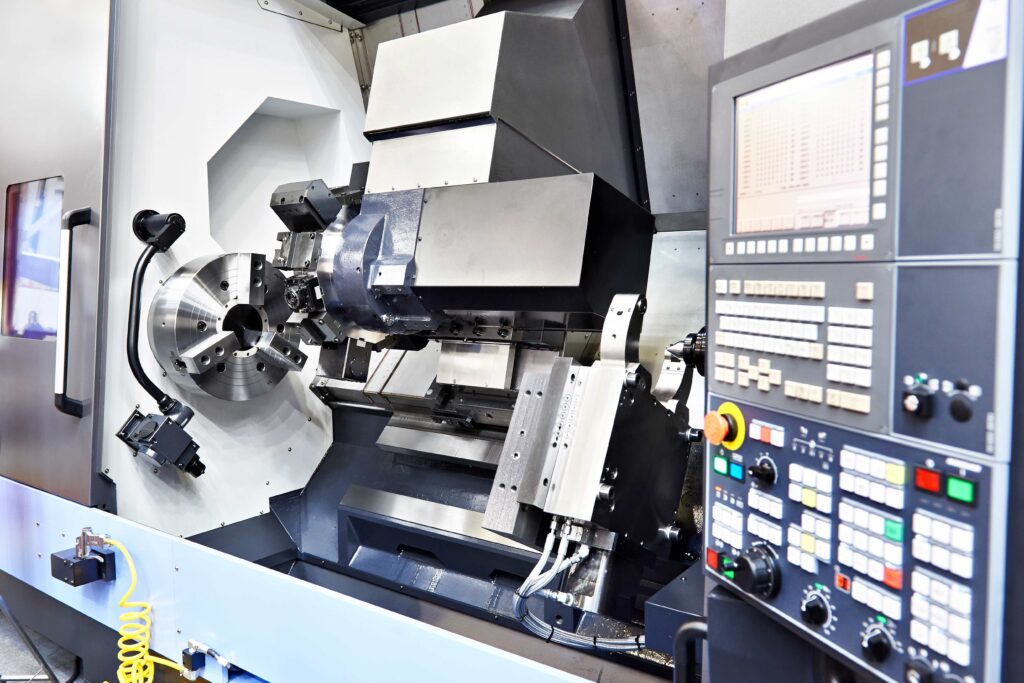
C3604という素材を使った加工作業において、最適な切削条件を知ることは重要です。しかし、どのような条件が最適なのか、具体的に理解している人は少ないのではないでしょうか?本記事では、「C3604加工のための最適な切削条件とは?」というテーマに焦点を当て、詳細なガイドをご紹介します。切削条件に関する専門知識がなくても安心してください。この記事を読むことで、C3604加工における最適な切削条件について理解が深まることでしょう。加工作業における新たな視点を得ることができるかもしれません。ごゆっくりとお楽しみください。
C3604加工の基本
C3604とは?―快削黄銅の特徴
C3604の加工において最適な切削条件を見極めることは、製品の品質向上と製造コストの削減に直結します。この合金は快削黄銅として知られ、その優れた加工性により多くの産業で利用されています。最適な切削条件は材料の特性、加工する機械の種類、製品の要求精度によって異なりますが、一般的に、C3604の加工には比較的高速の切削速度が推奨されます。具体的には、切削速度は100~300m/minの範囲、フィードレートは0.05~0.35mm/revが適しており、さらに、鋭利な工具を用いることで、バリの発生を抑えることが可能です。適切な潤滑剤の使用も、工具の耐久性を高め、より滑らかな表面仕上げを実現します。このように、C3604に対する理解を深め、適切な切削条件を選定することで、効率的かつ高品質な加工が実現されるのです。
C3604の一般的な用途
C3604の適切な切削条件を見つけることは、精密加工において非常に重要です。この合金は、その加工性の良さから幅広い産業用途において利用されています。しかし、最良の結果を得るためには、切削条件を慎重に選定する必要があります。具体的には、適切な切削速度、フィード率、切削液の使用が重要となります。例えば、切削速度が速すぎると、工具の摩耗が早まる可能性がありますし、遅すぎると加工効率が落ちます。同様に、フィード率が適切でないと、表面仕上げが悪化したり、加工精度に影響を与えることがあります。また、切削液は、熱を逃がし摩擦を低減させる役割があるため、適切なものを選択することが必須です。最終的に、これらの条件を正確に組み合わせることが、C3604の切削加工において最適な結果を得る鍵となります。
真鍮加工での一般的な問題点
C3604加工に最適な切削条件を理解することは、高品質な製品を効率的に生産するために不可欠です。この合金は、優れた機械加工性と耐食性を持つため、電子機器や自動車部品など幅広い分野で利用されています。適切な切削条件を選定する際には、ワークピースの材質特性、切削速度、送り速度、加工硬度など多くの要因が考慮されます。
たとえば、C3604はその良好な切削性から高速度で加工が可能ですが、速度が速すぎると工具の摩耗が早くなります。逆に速度が遅すぎると、加工効率が悪くなり、コストが増加します。さらに、適切な冷却液の使用は、切削工具の耐久性を高め、仕上がりの品質を改善する効果があります。
具体的な例としては、C3604の旋削加工においては、切削速度を100〜300m/min、フィードを0.1〜0.3mm/revに設定することが一般的です。こうした条件下で加工することにより、工具の摩耗を抑えながら、清潔な切断面を得ることが可能です。
総じて、C3604の加工に際しては、材質特性を考慮した切削条件の選定が品質と効率の両方を保ちながら加工を行う鍵となります。適切な条件のもとで加工を行うことで、コストを抑えつつ品質の高い製品を生産することができるでしょう。
C3604切削条件の理解
切削条件の基本要素
C3604加工における最適な切削条件を見極めることは、高品質な加工品を得るために不可欠です。結論から言えば、適切な切削条件は、工具の寿命を延ばし、加工精度を保つ上で重要な役割を果たします。その理由は、切削条件が切削速度、送り速度、切削深さのバランスに大きく影響を与え、材料の特性に応じてこれらを調整することが必要だからです。例えば、C3604は真鍮の一種であり、その柔らかさと切削性の良さから、旋盤加工やフライス加工に適していますが、速度が速すぎると材料が溶着しやすくなり、遅すぎると加工時間が不経済になります。また、適切な切削油の使用は、摩擦熱を低減し切削粒子の除去を助けるため、仕上がりの精度を高める効果もあります。結論を再び強調しますが、C3604加工においては切削条件を適切に管理することが、品質と効率の良い加工を実現する鍵です。
C3604の材料特性と切削条件
C3604は真鍮の一種であり、その加工における最適な切削条件の理解は品質と効率を大きく左右します。この素材は優れた機械加工性を持っているため、適切な条件設定により滑らかな表面が得られ、工具の摩耗も抑えられます。具体的には、刃先の角度やスピード、送り速度が重要な要素です。例えば、切削速度は素材の硬さに応じて調整され、一般には中速から高速が推奨されます。さらに、連続的な切削作業には、切削液を適切に用いることで、切り屑の排出を助け、熱の発生を抑制し、切削精度を高めることができます。総じて、C3604の加工に最適な切削条件を見つけることは、生産性向上とコスト削減に繋がり、最終製品の品質保持にも不可欠です。
切削工具の選定とC3604
C3604材の加工における最適な切削条件を理解することは、高品質な加工品を得るために不可欠である。適切な切削条件は、工具の摩耗を減少させ、製品寿命を延ばすことに寄与する。C3604という真鍮合金は、その良好な加工性から幅広い産業で利用されている。しかし、この材質を加工する際には、切削速度や送り速度、切削液の使用といった要素が重要である。
例えば、高速度での切削は材料に熱を発生させ易く、これが寸法精度や表面仕上げに影響を及ぼす可能性がある。対して、適切な切削速度は、工具の摩耗を防ぎ、安定した加工を実現する。加えて、切削液の適切な選択と使用は、摩擦と熱を低減し、切削工具の寿命を延ばす効果が期待できる。
したがって、C3604の加工に最適な切削条件の選定は、材料の特性を考慮し、工具の耐久性や仕上がり品質を最大限に引き出すことが重要である。選定された条件が、安定した高品質な生産を支える基盤となる。
真鍮の反り問題と対策
反りの原因とその影響
反りは製品の品質に大きな影響を与えるため、その原因を理解し、適切な対策を講じることが重要です。主な原因は、材料の不均一な熱処理やクランピングの際の不適切な力の掛け方にあります。例えば、C3604素材の切削加工時に不均一な加熱が生じると、材料内部に応力が生じ、反りの原因となります。また、クランプを使う際に力を均等に分散させないと、加工後に反りが生じやすくなります。このような反りは、製品の精度を低下させるだけでなく、組み立て時の問題や機能不全を引き起こす可能性があります。したがって、加工前の適切な設計と、加工時の熱管理や力の加え方の見直しを通じて、反りを最小限に抑えるべきです。これにより、高品質な製品の製造が可能となります。
反りを防ぐための切削条件の調整
C3604材の加工で最適な切削条件を見つけることは、工具の寿命を延ばし、生産性を向上させる上で非常に重要です。理想的な切削条件は、材料の特性、加工する製品の形状、所望の精度に依存します。例えば、C3604は鉛を含むため、一般的に切削が容易な材料ですが、その柔らかさゆえに切削時にはバリが発生しやすく、また、精度の高い加工が要求される場合は、工具の摩耗が早まることがあります。適切な切削速度とフィード率を設定することにより、これらの問題を抑えることが可能です。具体的には、小さな切削深さを利用し、急速な工具の冷却を行うことで、工具の摩耗を減少させ、加工面の品質を保つことができます。結論として、C3604の加工における最適な切削条件は、材料の特性と加工する製品の要件に応じて細心の注意を払い選定することが求められます。
反り防止のための工夫と実践例
C3604加工における最適な切削条件を見つけることは、高品質な製品を効率的に生産するために不可欠です。C3604は銅合金の一種で、その加工性は優れていますが、切削条件によっては製品の反りが生じることがあります。この反りを防ぐためには、適切な切削速度、送り速度、切り込み量が重要です。例えば、切削速度を適正に保つことで、材料の熱変形を最小限に抑えることができます。また、送り速度や切り込み量を調整することで、切削抵抗を適切にコントロールし、反りの原因となる内部応力を低減することが可能です。具体的な実践例としては、小径エンドミルを用いた高速での軽切削が挙げられます。これにより、工具と材料の熱が分散し、反りを防ぐことができます。結論として、C3604の切削では、機械の性能や材料の特性を考慮した切削条件の選定が、反りを防ぎながら品質と生産性を保つ鍵となるのです。
真鍮材料の旋盤加工における精度向上
精度向上のための基本的な切削条件
C3604の加工に最適な切削条件を知ることは、効率的かつ精度の高い加工に不可欠です。C3604は切削性に優れた真鍮の一種であり、機械部品や電子部品など幅広い用途で使用されます。最適な切削条件を見つけるためには、素材の特性を理解し、切削速度、送り速度、切削液の使用などの要因を適切に調整する必要があります。
例えば、切削速度は加工精度や表面仕上がりに影響を与え、速すぎると工具の摩耗を早める一方で、遅すぎると加工効率が低下します。送り速度も同様に、適切でない場合は加工面の荒さが生じる原因となります。加えて、切削液の使用は工具の冷却や切りくずの排出を助け、工具寿命の延長や加工品質の向上に寄与するため重要です。
結論として、C3604の加工には、素材の特性に合わせた切削速度と送り速度の適正化、そして適切な切削液の使用が最適な切削条件となります。これらをバランス良く調整することで、高い加工効率と精度の向上が期待できるでしょう。
旋盤加工における具体的なテクニック
旋盤加工で使用されるC3604は、加工性が良く、電気部品や装飾品など様々な製品に利用されています。この素材を効率良く加工するためには、最適な切削条件を見極めることが重要です。一般的に、良い切削条件とは、工具の摩耗を抑えつつ、加工表面の品質を保ちながら、生産効率を最大化する条件のことを指します。C3604を加工する際には、切削速度や送り速度、切り込み深さが特に重要となってきます。例えば、切削速度を適切に設定することで、素材への熱の影響を抑えることができ、仕上がりの精度を高めることが可能です。また、適切な送り速度の設定により、刃の摩耗を防ぎつつ、滑らかな表面を得ることができます。これらの切削条件は経験や材料特性に基づき微調整することが望ましいです。最適な切削条件の選定により、C3604の加工効率を高めることができるのです。
加工精度を左右する要因の理解
C3604加工における最適な切削条件を見極めることは、製品の精度を大きく左右します。素材の性質を理解し、適切な切削速度、送り速度、切削液の使用が求められるのです。例えば、C3604は鉛を含む真鍮の一種であり、柔らかく加工しやすい特性を持っていますが、不適切な切削条件下では材料が変形したり、工具の摩耗が激しくなる可能性があります。具体的な例を挙げると、C3604は一般的に高速度鋼か超硬資材の工具を使用し、比較的高い切削速度で加工可能ですが、過剰な速度は切りくずの排出問題を引き起こすことがあります。また、十分な切削液の供給は切りくずの排出を助け、摩耗を減少させる効果が期待できます。最終的に、これらの条件を適切に管理することで、C3604の加工精度は飛躍的に向上し、材料と工具の寿命も延ばされるのです。
快削黄銅のフライス加工における速度向上
フライス加工の速度を決定する要因
C3604加工では、最適な切削条件の選定が品質向上に不可欠です。結論から言えば、切削速度、送り速度、切削深さが加工精度や効率を大きく左右します。具体的には、C3604の材質特性を考慮して、適度な切削速度を保つことが重要です。たとえば、切削速度が過度に速いと材料が熱を持ちやすく、ツールの摩耗や加工物の品質低下の原因となります。逆に、あまりに遅すぎると加工時間が過剰に長くなり、コストや効率に影響を及ぼすことがあります。また、送り速度や切削深さも材料の特性や加工機械の能力に合わせて適切に設定する必要があります。実際には、これらの条件を事前にテスト加工を行いながら最適化することが推奨されます。最適化された切削条件によって、精度の高い加工が実現でき、同時に工具寿命を延ばし、生産性の向上が期待できるためです。
速度向上のための切削条件の最適化
C3604の切削加工における最適な切削条件を見極めることは、加工効率の向上とコスト削減に不可欠です。C3604は真鍮の一種であり、優れた加工性を持つことから多くの部品製造に用いられていますが、切削条件が不適切だと仕上がりの精度や工具の耐用年数に悪影響を及ぼすことがあります。最適な条件とは、具体的には切削速度、送り速度、切り込み量を適切に設定することです。例えば、C3604は比較的柔らかい材料であるため、旋盤加工では高い切削速度を適用できますが、加工中の振動や工具の熱による影響を考慮して、微細な調整が必要になります。また、切屑の排出性を良くするためにも、適切な送り速度の選定が重要です。これらを踏まえ、多くのメーカーは独自の試験を重ね最適な切削条件を見つけています。結論として、C3604の加工においては、材料の特性を十分理解し、実際の加工状況に合わせた切削条件の最適化が、品質向上とコスト削減につながるのです。
効率的なフライス加工のためのコツ
C3604材の加工において最適な切削条件を見極めることは、製品の品質向上と製造コストの削減に直結します。C3604とは、銅合金の一種であり、その加工性は切削条件に大きく左右されます。最適な条件を選定するには、主に工具の種類、切削速度、送り速度、切り込み深さ、潤滑の有無などを考慮します。
たとえば、切削速度は材料の熱伝導率や硬度に影響され、速すぎると工具の摩耗を早め、遅すぎると加工効率が低下します。送り速度もまた、表面仕上げや刃先の負担に密接に関わります。C3604の場合、精密加工が求められることが多いため、適切な切削速度と送り速度のバランスが重要です。また、適切な潤滑剤の使用は、刃先の冷却と摩耗の軽減に役立ちます。
具体的な例を挙げると、C3604をフライス加工する際には、切削速度を30〜100m/min、送り速度を0.1〜0.2mm/revに設定し、切り込み深さは工具の直径の5〜10%以内に抑えると良い結果が得られることが多いです。
結論として、C3604の切削条件を見極めるには、材料の特性を理解し、加工機械の性能と工具選定を適切に行い、試作や経験に基づいた微調整が必要です。これにより、高品質な製品を効率良く生産することが可能となります。
C3604の切削加工での困りごととその解決策
加工中の一般的なトラブルと対処法
最適なC3604加工の切削条件を理解することは、製品の品質を向上させ、製造効率を高めるために不可欠です。C3604は黄銅の一種であり、良い機械加工性を持つ一方で、不適切な切削条件下では加工時のトラブルが発生する可能性があります。
適切な切削条件を決定するには、切削速度、送り速度、および切削液の使用が重要です。例えば、切削速度が速すぎると、工具の摩耗が早く進み、精度が低下します。しかし、適度に速い切削速度は切屑の連続性を保ち、滑らかな表面を実現します。送り速度も同様に、適切に設定されなければ、工具の損傷や仕上がり面の質を損ねる原因になります。また、切削液は、熱の分散を助け、摩擦を減少させることで、工具の寿命を延ばし、加工精度を向上させます。
実際の加工例を見ても、適切な切削条件の下で加工されたC3604は、均一な表面仕上げがされ、寸法精度も高くなります。逆に、条件設定が不適切だと、加工不良や工具の破損などの問題が起こりがちです。
したがって、C3604の加工において優れた結果を得るためには、切削条件を慎重に選び、継続的な監視を行いながら、材料の特性に合わせて調整する必要があります。これにより、高い生産性と製品品質を維持することができます。
切削振動の抑制と精度向上
C3604の加工に最適な切削条件を見つけることは、高い加工精度を実現し、工具の寿命を延ばすために非常に重要です。具体的には、C3604材の切削には、適切な切削速度、送り速度、および切り込み量の選定が不可欠です。例えば、切削速度が速すぎると工具の摩耗が進み、遅すぎると加工時間が増えてしまいます。送り速度も、高すぎると切削振動が発生しやすく、低すぎると表面粗さが悪化する可能性があります。また、切り込み量は加工負担と直接関係し、最適な値を見極めることが重要です。
実際の加工現場で、ある企業がC3604の加工テストを行った際、切削速度や送り速度を段階的に変化させながら、その都度切削振動と表面粗さを検証しました。この結果から、特定の範囲内で安定した切削振動の低減と優れた表面粗度が得られることが確認されました。このように実験を重ねることで、最適な切削条件を導き出すことが可能です。
結論として、C3604の加工において最適な切削条件は、実際の加工環境や機械特性を踏まえ、慎重な試験と調整を通じて見極める必要があります。これにより、切削振動の抑制と高精度な加工が可能となるでしょう。
加工品質を向上させるためのチェックリスト
C3604材の加工における最適な切削条件を適切に設定することは、加工品質の向上に直結します。ここでの結論は、適切な切削速度、送り速度、切削深さを見極めることが不可欠となります。理由としては、これらの条件が加工時の振動や切りくずの排出、ツールの摩耗状態に大きく影響し、これが最終的な製品精度に反映されるからです。例えば、速すぎる切削速度は摩耗を早め、遅すぎると加工時間が増大する上に表面仕上げが悪化する可能性があります。一方、適切な送り速度の選択は表面粗さを効果的にコントロールし、切削深さは加工効率と仕上げ精度のバランスを取るポイントです。最終結論として、この各条件を材質や加工する形状、ツールの種類に応じて慎重に選定し、試作や経験値をもとに最適化を図るべきです。そうすることで、C3604材の切削加工における品質と効率は格段に向上するでしょう。
効率的なC3604の精密加工法
精密加工における切削条件の設定
C3604加工における最適な切削条件を設定することは、精密加工の成功に不可欠です。最良の加工結果を得るために考慮すべき点は多岐にわたりますが、具体的には工具の選定、切削速度、送り速度、そして切削液の使用が主要な要素です。C3604は銅合金の一種であり、その優れた機械加工性から多くの工業分野で利用されますが、適切な切削条件が守られない場合、工具の摩耗が早まったり、仕上がりの品質が低下する可能性があります。例えば、高い切削速度は生産性を向上させることができますが、適度でなければ工具への負担が増加し、耐用年数を短縮します。したがって、C3604の加工時には、材料特性に合わせた切削条件の選定が不可欠であり、そのためには試作や経験に基づく微調整が必要となります。最終的には、精密な加工を実現するための適切な切削条件の設定が、効率良く高品質な製品を生産する鍵であるといえます。
精密加工で求められる機械設備の特徴
C3604の加工において最適な切削条件を見つけることは、精密加工の要となります。適切な切削条件を選択することで、工具の摩耗を減らし、加工精度を向上させることができます。特に、C3604は銅合金の一種であり、優れた切削性能を誇る材料ですが、適切な切削条件を見極めなければ、工具の寿命を短くしてしまう恐れがあります。
具体的には、C3604の場合、高速度の旋削やフライス加工を行う際には、刃先の冷却や潤滑を十分に行うことが重要です。例として、切削速度や送り速度、切り込み量を材料の硬度や工具の種類に応じて最適化し、定期的な刃物の点検を行うことが挙げられます。これにより、精度の高い加工を実現し、生産効率も向上します。
結論として、最適な切削条件を見極めることはC3604の加工において不可欠です。そのためには、材料の特性を正しく理解し、工具と加工方法の選定に注意を払いながら、経験と実測値を基にした調整が求められます。正しい切削条件のもとで加工を行うことで、品質と効率の双方を高めることができるのです。
精密加工における作業の効率化テクニック
C3604の適切な切削条件を理解することは、精密加工における作業の効率化と品質向上に不可欠です。最適な切削条件とは、材料の特性に応じて切削速度、送り速度、切削深さを調整することに他なりません。たとえば、C3604は鉛を含む黄銅であり、その柔らかさから比較的高い切削速度が可能です。しかし、切削速度が高すぎると工具の摩耗が早まるため、適正な速度の選択が重要となります。また、送り速度や切削深さを適切に設定することで、仕上がりの精度を高め、切りくずの除去もスムーズに行えます。具体的な例を挙げると、C3604の場合、切削速度は約100〜300m/minが一般的であり、工具の材質にもよりますが、この範囲内で最適な条件を見つけることが望ましいです。このように、C3604加工では材料特有の特性を考慮し、各切削条件をバランスよく設定することが、効率的で高品質な加工を実現する鍵となります。
C3604加工のための最適な切削条件のまとめ
切削条件のチューニングの重要性
C3604の加工における最適な切削条件を見つけることは、高品質な製品を効率的に生産するために非常に重要です。適切な切削条件を選定することで、工具の摩耗を抑え、長寿命化を実現し、また仕上げ面の精度を向上させることができます。具体的な例として、C3604の場合、切削速度は材料の硬度や耐熱性を考慮して選ぶ必要があり、また刃の進行方向に対する切削深さや送り速度も、表面品質に大きな影響を与えます。また、冷却液の使用は、工具の温度上昇を抑制し、切りくずの排出を助けるために不可欠です。このように、C3604の加工に最適な切削条件を見極めることで、製造コストを削減し、生産効率を高めることができるのです。最終的には、これらの最適化された条件を通じて、製品の競争力を高めることが可能になります。
加工効率と品質のバランス
C3604材の加工に際して、最適な切削条件を選定することは、加工効率と製品品質を高水準で保つうえで重要です。この合金は様々な産業で広く利用されるため、その加工条件について適切な知識を持つことが必須となります。例えば、C3604材は良好な切削性能を発揮するため、切れ味の鋭い工具を選び、適正な切削速度を維持することが推奨されます。具体的には、速度や送り、切り込み深さを材料の硬さや工具の材質に応じて調整する必要があります。また、良質な表面仕上げを実現するためには、適度な潤滑液の使用も重要です。C3604材の切削においては、これらの要因を総合的に考慮し、製品の耐久性や精度を損なわない範囲での加工を心掛けるべきです。結論として、最適な切削条件の選定は、C3604材の加工品質と効率を左右する決定的な要素であり、注意深い検討が求められます。
継続的な改善と技術の進化
C3604の材料を加工する際、最適な切削条件を見極めることは、工作機械の性能を最大限活用し、効率良く製品を生産するために不可欠です。結論から言えば、適切な切削速度、送り速度、工具の選定が重要となります。これらの因子を適正に設定することで、加工精度の向上と工具寿命の延長が期待できます。例えば、C3604は切削性に優れた真鍮の一種で、一般的に高速加工に適しています。しかし、速度が速すぎると工具の摩耗が早まり、遅すぎると加工時間が増加します。過去の実例においては、C3604を高精度に加工するためには、工具の材質やコーティング、切削液の種類にも注意を払う必要があります。再度結論に戻りますが、最適な切削条件の設定は、C3604材料の特性を理解し、実際の加工環境と経験に基づく試行錯誤から見出されます。それにより、高品質でコスト効率の高い加工が可能となるのです。