真鍮部品の製造過程で注意すべき品質管理のポイント
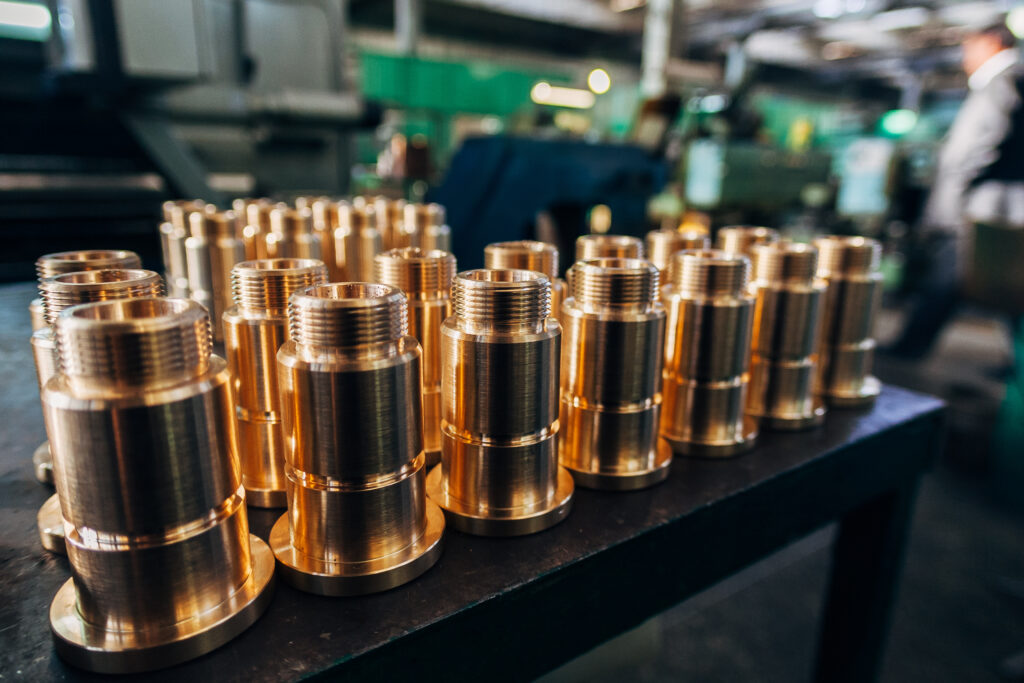
真鍮部品の製造過程において、品質管理は極めて重要な要素です。「どのようにして高品質な真鍮部品を作り上げるのか?」と悩んでいる方も多いのではないでしょうか。製造業に携わる方々が直面する課題や、品質管理において見逃してはいけないポイントを明確にすることで、より効率的で信頼性の高い生産体制を築く手助けをします。
このガイドでは、真鍮部品の品質管理の基本的な考え方から、具体的な手法や注意点までを詳しく解説します。もし、あなたが「真鍮部品の品質を向上させたい」「製造過程におけるトラブルを未然に防ぎたい」と考えているなら、この情報はきっと役立つでしょう。さあ、一緒に品質管理の重要性とそのポイントを探っていきましょう。
1. 真鍮部品の品質管理ポイントとは?
真鍮部品の品質管理は、精度や耐久性を確保するために非常に重要です。品質を確保するための適切な指標とプロセスを理解することが、最終的に高品質な部品を提供する鍵となります。
1-1. 真鍮部品の品質管理の重要性
- 精度の確保:
- 真鍮部品は、機械的強度や耐食性、外観の美しさが求められるため、品質管理をしっかり行うことが必要です。精度が低いと部品としての機能が損なわれるため、加工精度を確保することが最も重要です。
- 生産効率の向上:
- 高品質な製品を一貫して作り続けるためには、品質管理を徹底することが不可欠です。トラブルの発生を未然に防ぐことで、生産効率も向上します。
- コストの削減:
- 品質管理を怠ると、再加工や不良品の発生によるコストが増加します。適切な品質管理を行うことで、無駄なコストを削減することができます。
1-2. 品質管理における主要な指標
- 寸法精度:
- 部品の寸法が設計通りであるかをチェックするために、ゲージや測定機器を使用して寸法精度を管理します。
- 表面仕上げ:
- 真鍮部品の外観は、表面の仕上がりによって大きく影響されます。粗さやキズ、バリなどの表面欠陥を管理することで、品質を向上させます。
- 機械的性質:
- 引張強度、硬度、伸び率などの機械的特性を測定して、部品が求められる性能を満たしているかを評価します。
- 耐食性:
- 真鍮部品が使用環境において腐食しないか、適切なテストを実施し、耐食性を確認します。
1-3. 品質管理のプロセスと手法
- インプロセス管理:
- 加工中にリアルタイムで寸法や品質を監視し、問題が発生した場合にすぐに修正する方法です。これにより、不良品の発生を防ぐことができます。
- 最終検査:
- 加工後に最終的な品質チェックを行い、部品が設計通りに仕上がっているかを確認します。この段階で不良品を発見し、取り除くことで品質を保ちます。
- 統計的品質管理(SQC):
- 生産ラインで得られるデータを統計的に分析し、品質に関する傾向や問題点を把握します。問題が発生する前に予測し、改善措置を取ることができます。
2. 真鍮旋盤加工の際の注意点
真鍮を旋盤加工する際には、特有の注意点があります。これらを理解し、適切に対処することで、良好な加工結果を得ることができます。
2-1. 旋盤加工の基本
- 回転速度と送り速度:
- 真鍮は比較的軟らかい素材なので、切削時には適切な回転速度と送り速度を選ぶ必要があります。過度に高速で回転させると、切り屑が飛び散り、仕上がりが悪くなることがあります。
- 切削工具の選定:
- 真鍮を加工する際には、硬度が低く、耐摩耗性のある工具を使用することが重要です。特に、切削エッジが鈍くなると精度が低下するため、定期的な工具交換が必要です。
- 切削液の使用:
- 真鍮加工時には切削液を使用することで、摩擦を減少させ、工具寿命を延ばし、加工精度を向上させます。冷却効果と潤滑作用を両立させる切削液を選ぶことが重要です。
2-2. 加工中のトラブルとその対策
- 振動の発生:
- 旋盤加工中に振動が発生すると、加工精度が悪化します。これを防ぐためには、工作物をしっかりと固定し、切削条件を適切に設定します。
- 切り屑の詰まり:
- 真鍮は切り屑が大きくなりやすく、詰まりやすい素材です。定期的に切り屑を取り除き、加工がスムーズに進むようにすることが大切です。
- 過熱:
- 真鍮は熱がこもりやすい素材です。過熱を防ぐためには、冷却液を十分に供給し、切削時に適切な速度を選定することが重要です。
2-3. 加工精度を向上させるためのポイント
加工後の仕上げ工程では、精密な測定機器を使って寸法を確認し、必要に応じて微調整を行います。これにより、最終的な精度が向上します。
適切な切削条件の設定:
真鍮の切削には、適切な切削速度、送り速度、切削深さの設定が重要です。これらを最適化することで、精度の高い仕上がりを得ることができます。
工具のメンテナンス:
高精度な加工を維持するために、工具のメンテナンスを怠らないようにします。工具の鋭利さを保つことで、仕上がりがきれいになります。
振動の管理:
加工中の振動は精度に影響を与えるため、振動を最小限に抑えるように加工環境を整えることが重要です。
仕上げ加工の最適化:
加工後の仕上げ工程では、精密な測定機器を使って寸法を確認し、必要に応じて微調整を行います。これにより、最終的な精度が向上します。
3. 真鍮加工の基本的な知識
真鍮は金属部品として非常に広く使用される素材です。加工時にその特性を理解し、適切な方法と工具を選定することが重要です。
3-1. 真鍮の特性と利点
- 加工性:
- 真鍮は比較的柔らかく、切削や加工がしやすい素材です。このため、複雑な形状や細かい部品の製造にも適しています。
- 耐食性:
- 真鍮は耐腐食性に優れ、特に湿気や水に強い特徴があります。これにより、水道機器や海洋機器などに多く使用されます。
- 導電性と熱伝導性:
- 真鍮は良好な導電性を持つため、電気機器や電子機器の部品に使用されることが多いです。また、熱伝導性も良好で、熱を効率的に伝える用途にも適しています。
- 強度と耐久性:
- 真鍮は強度も十分で、長期間にわたって使用できる耐久性を持ちます。この特性により、金具や機械部品としても利用されています。
3-2. 加工方法の種類と選び方
- 切削加工:
- 真鍮は切削性が良いため、旋盤やフライス盤を使用した切削加工に適しています。精密な寸法が求められる場合は、高精度な切削を選択することが重要です。
- 圧延加工:
- 真鍮を薄く広げる圧延加工も行われます。特にシートや板材として使用する際に有効です。圧延によって、真鍮の表面を滑らかにし、強度を高めることができます。
- 鋳造:
- 真鍮は鋳造にも適した素材で、複雑な形状を作ることができます。鋳造後に仕上げ加工を行うことが一般的です。
- 圧縮成形:
- 真鍮のパイプや棒状の製品を圧縮成形で作ることもあります。この方法は大量生産に向いており、コストを抑えながら大量に部品を製造できます。
- 選び方:
- 加工方法の選定は、製品の形状、サイズ、精度、使用する環境に基づいて決定します。加工方法によって、後工程や仕上げの手間が異なるため、コストや生産効率を考慮して選びます。
3-3. 加工に必要な工具と設備
- 旋盤:
- 真鍮の部品加工には旋盤がよく使用されます。回転するワークに切削工具を当てて加工を行います。精密な仕上がりが求められるため、高精度な旋盤を使用することが望ましいです。
- フライス盤:
- フライス盤は、平面や溝などの加工に使用されます。真鍮の複雑な形状を切削するために利用されることが多いです。
- ボール盤:
- 穴あけ加工にはボール盤が使用されます。特に精度が求められる穴あけを行うために、微調整可能なボール盤が必要です。
- 切削工具:
- 真鍮に適した切削工具を選定することが重要です。通常、硬度が低い真鍮には鋼製の工具を使用しますが、加工内容によってはダイヤモンドコーティング工具やセラミック工具を使うこともあります。
- 研削盤:
- 最後に仕上げや精密な表面処理を行うために、研削盤を使用することがあります。これにより、表面の平滑性や寸法精度が向上します。
4. 金属加工における検査方法や注意点
金属加工では、加工後の品質検査が非常に重要です。検査方法と注意点を理解して、良品を確実に得ることが求められます。
4-1. 検査の種類と目的
- 寸法検査:
- 加工した部品が設計通りの寸法に仕上がっているかを測定します。ゲージやマイクロメーター、ノギスなどの測定器を使用して精密に測定します。
- 表面検査:
- 表面の粗さや傷、バリなどをチェックします。視覚検査や専用の表面粗さ測定機を使用して、部品の外観や機能に影響を与える不良を見つけます。
- 機械的特性検査:
- 引張試験や硬度試験を実施し、部品が求められる機械的性質を持っているかを評価します。特に、耐摩耗性や強度が求められる部品で行います。
- X線検査:
- 厚い金属部品や複雑な形状の部品においては、X線検査を使用して内部の欠陥(気泡やひび割れなど)を確認します。
4-2. 検査時の注意点
- 環境の整備:
- 検査を行う場所は、清潔で安定した環境であることが重要です。温度や湿度などの影響を受けないようにすることが、精度の高い検査を行うために必要です。
- 測定器具の校正:
- 測定器具は定期的に校正を行い、誤差を最小限に抑えることが大切です。校正が不十分な場合、正確な測定ができず、品質に影響を与えることがあります。
- 人為的ミスの回避:
- 検査員が注意深く作業を行い、同じ基準で測定することが大切です。また、測定結果を記録し、後から確認できるようにしておくと信頼性が高まります。
4-3. 検査結果の活用方法
検査結果を基に、品質向上のための具体的な指標を設定することができます。これにより、継続的な品質改善を目指すことが可能になります。
不良品の排除:
検査で不良品を発見した場合、その原因を突き止め、次回の生産に活かすことが重要です。頻繁に同じ問題が発生する場合は、加工プロセス自体の見直しを行います。
工程改善:
検査結果を元に、工程改善を行うことができます。例えば、特定の加工条件が不良品を多く生む場合、条件の見直しや新たな技術の導入を検討します。
品質向上の指標:
検査結果を基に、品質向上のための具体的な指標を設定することができます。これにより、継続的な品質改善を目指すことが可能になります。
まとめ
真鍮部品の製造過程では、原材料の選定、加工精度、熱処理、表面処理が重要です。特に、寸法管理や表面の仕上がり具合を厳密にチェックすることで、耐久性や性能を確保できます。また、定期的な機械メンテナンスと従業員の技術向上も品質向上に寄与します。