【製造業必見!砲金部品の品質向上に役立つ検査項目ガイド】
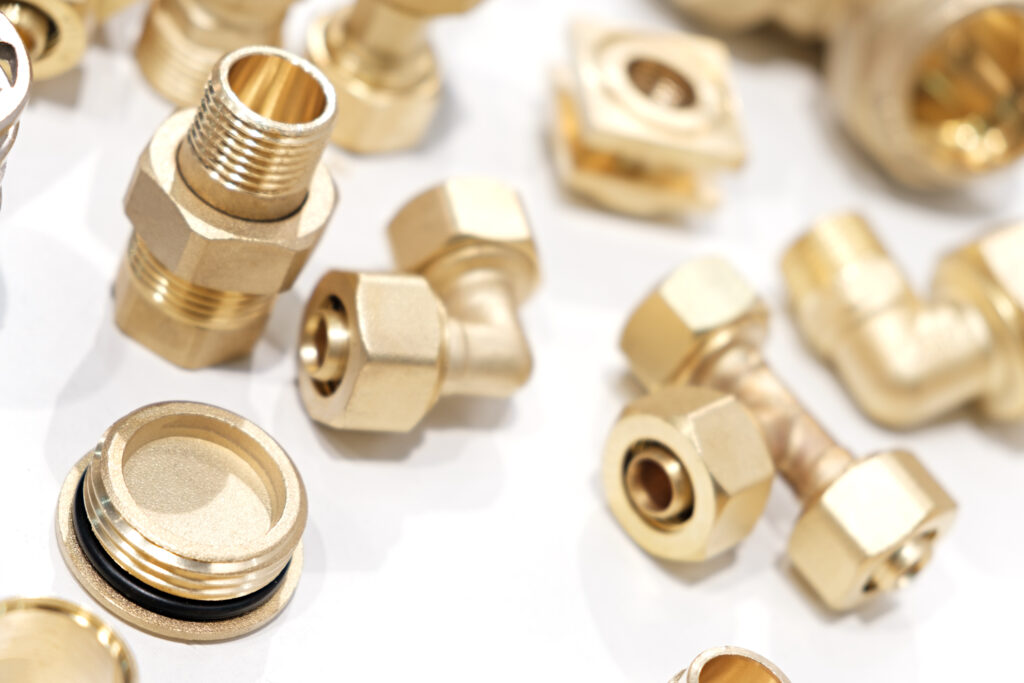
製造業における品質管理は、製品の信頼性と顧客満足度を左右する重要な要素です。特に砲金部品は、その特性上、各種業界で広く使用されているため、その品質が求められます。「どうすれば砲金部品の品質を向上させられるのか?」と悩んでいませんか?そんなあなたのために、今回は「砲金部品の品質向上に必要な検査項目」のガイドをお届けします。
この記事では、以下のような疑問にお答えします。
- 砲金部品の品質を評価するための具体的な検査項目は何か?
- 各検査項目がどのように品質向上に寄与するのか?
- 効果的な検査の実施方法とは?
製造業で成功を収めるためには、品質向上が欠かせません。これから紹介する検査項目を理解し、実践することで、あなたの製品の信頼性を高め、競争力を強化しましょう。さあ、一緒に砲金部品の品質向上に向けた第一歩を踏み出しましょう!
1. 砲金部品の品質向上に必要な検査項目の重要性
砲金(BC:ブロンズキャスト)は耐摩耗性や耐食性に優れ、バルブ、ポンプ、ベアリングなどの重要部品に使用されます。そのため、高品質な砲金部品を製造するには、適切な品質管理と検査が不可欠です。本章では、品質管理の基本概念と金属加工における品質管理の役割について解説します。
1-1. 品質管理の基本概念
品質管理は、製造工程において一定の品質を維持し、不良品の発生を抑えるための管理手法です。特に砲金部品においては、以下の要素が品質に大きく影響します。
- 寸法精度:部品の公差や形状が規格通りか確認することが重要
- 材料の品質:鋳造時の不純物や組成の均一性が性能を左右
- 表面処理:耐摩耗性や耐食性の向上を目的とした処理の適切さ
- 強度と耐久性:使用環境での負荷に耐えられるかを検査
これらの要素を管理することで、製品の信頼性向上につながります。
1-2. 金属加工における品質管理の役割
金属加工において品質管理は、以下のような役割を果たします。
- 製造プロセスの標準化:均一な製品を安定して生産するために工程を標準化
- コスト削減:不良品の発生を減らし、再加工や廃棄コストを削減
- トレーサビリティの確保:材料の出所や加工履歴を管理し、不具合発生時に迅速な対応を可能に
- 信頼性の向上:顧客の要求を満たし、長期的な品質維持を実現
2. 砲金部品の品質向上に必要な検査項目の選定ガイドライン
砲金部品の品質を向上させるためには、適切な検査項目を選定することが重要です。検査項目の基準を明確にし、業界標準を参考にしながら最適な方法を採用します。
2-1. 検査項目の選定基準
砲金部品の検査項目を選定する際は、以下の基準を考慮します。
検査項目 | 目的 | 検査方法 |
---|---|---|
寸法測定 | 指定された公差内に収まっているか確認 | ノギス、マイクロメータ、CMM(3次元測定機) |
材料組成分析 | 材質が規格通りか確認 | 発光分光分析、X線蛍光分析 |
機械的強度試験 | 引張強度・圧縮強度を確認 | 引張試験機、硬度計(ブリネル、ロックウェル) |
表面粗さ測定 | 表面仕上げの品質を保証 | 表面粗さ計、顕微鏡観察 |
耐摩耗性試験 | 長期使用時の摩耗の影響を評価 | 摩耗試験機 |
耐食性試験 | 腐食環境での耐久性を確認 | 塩水噴霧試験(SST)、湿潤試験 |
2-2. 業界標準とベストプラクティス
砲金部品の品質管理では、以下の業界標準が広く採用されています。
- JIS(日本工業規格):JIS H5111(砲金鋳物の規格)
- ASTM規格:ASTM B505(鋳造砲金の材料規格)
- ISO規格:ISO 4386(スライドベアリングの砲金材料)
また、品質管理のベストプラクティスとして、以下の手法を取り入れると効果的です。
- SPC(統計的工程管理):生産ラインのばらつきを監視し、品質の安定化を図る
- QCサークル活動:現場レベルでの継続的な品質改善を推進
- PDCAサイクルの適用:品質改善を継続的に行うための計画(Plan)、実行(Do)、評価(Check)、改善(Act)を回す
これらのアプローチを組み合わせることで、砲金部品の品質を安定させることができます。
3. 砲金部品の品質向上に必要な検査項目を活用したプロセス構築
品質向上を実現するためには、検査項目を単独で運用するのではなく、全体のプロセスの中に組み込むことが重要です。適切なプロセス設計とチームでの協力により、より効果的な品質管理が可能になります。
3-1. 効果的な検査プロセスの設計
効果的な検査プロセスを構築するためには、以下のポイントを考慮します。
- 検査フローの標準化
- 材料の受け入れ検査 → 中間工程検査 → 最終検査の流れを確立
- 各段階で必要な検査項目を明確化し、作業手順を統一
- リアルタイムでの品質管理
- SPC(統計的工程管理)を活用し、リアルタイムでデータを分析
- 問題が発生した際に迅速に対策を講じる仕組みを構築
- トレーサビリティの確保
- 検査データの記録をシステム化し、不具合発生時の追跡を容易にする
- 材料ロットや加工履歴を管理し、再発防止策を講じる
3-2. チームでの協力とコミュニケーション
品質向上には、検査担当者だけでなく、設計・製造・管理部門が一体となって取り組むことが重要です。
- 情報共有の仕組みを構築
- 品質データをクラウド管理し、リアルタイムで共有
- 定期的な品質ミーティングを実施し、問題点の洗い出しと改善策の検討
- 品質意識の向上
- 品質管理に関する研修や勉強会を実施し、現場の意識を高める
- 目標値を設定し、達成度に応じた評価制度を導入
4. 測定誤差を最小限に抑えるためのテクニック
測定誤差は品質管理の精度に大きな影響を与えるため、環境の最適化や測定手順の見直しが必要です。
4-1. 測定環境の最適化
測定環境を整えることで、誤差を最小限に抑えることができます。
- 温度変化への対策
- 材料の膨張・収縮による寸法誤差を防ぐため、測定室の温度を一定(20℃±1℃)に保つ
- 湿度管理
- 測定機器の腐食や変形を防ぐため、湿度を40〜60%に調整し、防湿対策を施す
- 振動の影響を排除
- 測定中の揺れによる数値のブレを防ぐため、防振構造の測定台を使用
- 測定機器の定期校正
- 精度の低下を防ぐため、定期的に校正を行い、誤差をチェック
4-2. 注意すべきポイントとトラブルシューティング
測定時には、以下の点に注意することで誤差を最小限に抑えられます。
- 測定手法の統一
- 測定手順を標準化し、測定者ごとのばらつきをなくす
- 可能な限り非接触測定(レーザー測定器など)を活用
- 測定器具の取り扱い
- マイクロメータやノギスのゼロ点調整を徹底する
- 測定器の使用前後に清掃し、異物付着による誤差を防ぐ
- データの検証
- 測定値に異常があった場合、複数回の測定を行い再確認
- 過去データと比較し、異常値が発生した原因を特定
これらの対策を実施することで、測定精度を向上させ、品質管理の信頼性を高めることができます。
まとめ
製造業において砲金部品の品質向上は不可欠です。本記事では、検査項目ガイドを通じて、寸法精度、表面仕上げ、機械的特性、耐腐食性などの重要な検査基準を紹介。これにより、製品の信頼性を確保し、顧客満足度を向上させる手助けをします。品質管理の強化に役立つ情報が満載です。