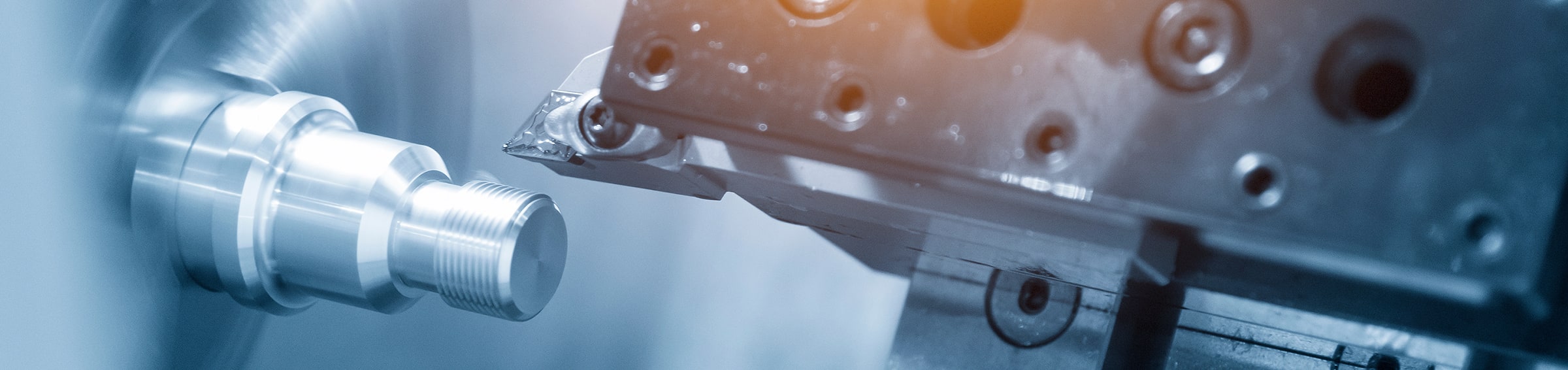
加工技術 column
旋盤加工の効率を上げる!最適な切削速度と送り速度の決定方法
旋盤加工の効率を上げるためには、最適な切削速度と送り速度の設定が不可欠です。しかし、これらの設定をどのように決定すれば良いのでしょうか?多くの加工業者がこの問題に直面しており、適切な速度設定に悩むことも少なくありません。
本記事では、旋盤加工における切削速度と送り速度の重要性を解説し、具体的な設定方法について詳しく説明します。特に、切削工具や素材の特性に応じた最適な速度を見つける方法を紹介し、効率的かつ高品質な加工を実現するためのヒントを提供します。
もしあなたが旋盤加工を行っているなら、この記事を通じて効率を最大化し、コスト削減や生産性向上を図るための具体的な知識を得られることでしょう。旋盤加工の技術を深め、さらなる発展を目指しましょう!
1. 旋盤での最適な切削速度と送り速度設定の重要性
旋盤加工における最適な切削速度と送り速度の設定は、加工精度と工具の寿命に直結します。適切な切削条件を選ぶことは、効率的で高品質な加工を実現するために非常に重要です。
1-1. 切削条件の決定方法
切削条件を決定する際は、以下の要素を考慮します:
- 材料の種類:加工する材料の硬さや特性に応じて、切削速度や送り速度を設定します。
- 工具の種類:使用する工具の材質や形状に適した条件を選びます。例えば、超硬工具やコーティング工具ではより高い切削速度が可能です。
- 機械の能力:旋盤の馬力や回転数の範囲を考慮し、機械が適切に動作できる条件を選びます。
- 加工目的:仕上げ加工か荒削りか、または加工後の仕上がり精度の要求に応じて、最適な条件を設定します。
1-2. 切削速度と送り速度の関係
切削速度と送り速度は互いに密接に関連しています:
- 切削速度(Vc):工具の先端が材料表面を1分間に移動する速度で、通常、メートル/分で表されます。切削速度が高すぎると、工具の摩耗が早くなり、逆に低すぎると加工効率が悪くなります。
- 送り速度(F):工具が材料に対してどれだけ進むか、1回の回転でどれくらい前進するかを示します。送り速度が速すぎると表面仕上げが荒くなり、遅すぎると加工時間が長くなります。
- 関係:切削速度が適切に設定されていれば、それに見合った送り速度を設定することが重要です。送り速度が遅いと切削熱が集中しやすくなり、過度の摩耗や加熱が発生します。
2. 旋盤の切削速度や回転数の計算方法
旋盤加工における切削速度や回転数を計算することは、最適な加工条件を導き出すために必要です。以下の計算方法を使用します。
2-1. 切削速度の計算式
切削速度(Vc)は以下の式で計算できます:
- Vc:切削速度(m/min)
- D:ワークピースの直径(mm)
- N:回転数(rpm)
この式を用いることで、所定の回転数と材料の直径から、切削速度を求めることができます。
2-2. 回転数の求め方
回転数(N)は切削速度(Vc)を用いて以下の式で求められます:
- N:回転数(rpm)
- Vc:切削速度(m/min)
- D:ワークピースの直径(mm)
この計算により、切削速度を設定した場合の適切な回転数を導き出すことができます。
3. 特定の材料(SUS440C)に対する最適な加工速度
SUS440Cは、ステンレス鋼の一種で、高い硬度と耐摩耗性を持ち、切削加工が難しい材料です。そのため、最適な切削条件を設定することが重要です。
3-1. SUS440Cの特性
SUS440Cは、高炭素クロム鋼で、以下の特性を持っています:
- 高硬度:焼き入れ後の硬度が非常に高く、刃物や金型などにも使用されます。
- 耐摩耗性:高い耐摩耗性を有するため、長期間の使用に耐えます。
- 耐食性:ステンレス鋼として、耐食性も一定程度備えています。
3-2. SUS440Cの最適切削速度
SUS440Cの切削時の最適切削速度は、工具や切削条件によって異なりますが、一般的には以下のように設定されます:
- 切削速度(Vc):20~30 m/min
- 送り速度(F):0.05~0.15 mm/rev(回転あたりの送り)
高硬度材料であるため、低速で慎重に加工を進める必要があります。また、工具の摩耗が早くなる可能性があるため、冷却・潤滑の管理も重要です。
4. 加工方法や材質に応じた適正な送り速度
送り速度の設定は、加工方法や材質に合わせて調整することで、加工効率や仕上がり精度を最適化できます。材質によって適切な送り速度が異なり、それにより加工の品質や工具の寿命に大きな影響を与えます。
4-1. 送り速度の基本概念
送り速度(F)は、工具がワークに対してどれだけ進むかを示す速度で、通常はmm/rev(回転あたりの送り)で表されます。送り速度を適切に設定することで、次の利点があります:
- 加工時間の短縮:最適な送り速度により加工時間が短縮され、生産性が向上します。
- 表面仕上がりの向上:適切な送り速度を設定することで、表面の粗さが低減し、仕上がり精度が向上します。
- 工具の摩耗を抑制:過度に速い送り速度は工具の摩耗を早めますが、適切な設定で工具寿命を延ばすことができます。
4-2. 材質別の送り速度設定
材質ごとに最適な送り速度は異なります。以下は代表的な材質別の送り速度設定の例です:
- 鉄系材料(例:S45C、SS400):比較的高い送り速度が許容され、0.1~0.2 mm/revの範囲で設定されます。
- ステンレス鋼(例:SUS304、SUS440C):硬度が高いため、0.05~0.1 mm/revの遅い送り速度が推奨されます。
- アルミニウム:比較的柔らかく加工しやすいため、送り速度は0.2~0.3 mm/rev程度が一般的です。
- 鋳物や高硬度材料:送り速度を低めに設定し、0.03~0.05 mm/revが推奨されます。
材質が硬くなるほど送り速度は低くし、工具の負担を減らすことが重要です。
5. 汎用旋盤とNC旋盤の切削条件の違い
汎用旋盤とNC旋盤では、切削条件が異なるため、加工精度や効率にも違いが生じます。それぞれの特徴を理解することで、適切な切削条件の設定が可能です。
5-1. 汎用旋盤の特徴
汎用旋盤は、手動操作を主体にした旋盤であり、以下の特徴があります:
- 操作の柔軟性:オペレーターの熟練度に応じて多様な加工が可能で、少量多品種生産に向いています。
- 設定が簡単:操作が直感的で簡単なため、初めて使用する人でも扱いやすいです。
- 限られた自動化:基本的に手動での送り操作となるため、複雑な加工や高精度な繰り返し加工には限界があります。
- 加工条件設定:切削速度や送り速度をオペレーターが手動で調整するため、作業者の技術が重要になります。
5-2. NC旋盤の利点と切削条件
NC旋盤は、コンピュータ制御によって自動的に加工が進むため、以下の利点があります:
- 高精度な加工:自動で繰り返し精度の高い加工が可能で、特に大量生産に向いています。
- 複雑な加工の対応:プログラムに基づいて複雑な形状や多軸加工が簡単に行えるため、複雑な部品加工に適しています。
- 切削条件の最適化:NC旋盤では、加工条件(切削速度や送り速度)が自動で最適化されるため、常に安定した加工が可能です。機械の自動化により、高速回転や適正な送り速度の設定も容易に実現できます。
- 操作性:プログラムにより設定されるため、オペレーターの経験に依存せず、高度な加工が可能です。
NC旋盤は、特に精度や生産性を重視する場合に有効で、切削条件を最適化することでさらに効率を高めることができます。
まとめ
旋盤加工の効率を向上させるためには、最適な切削速度と送り速度の設定が重要です。切削速度は材料や工具の特性に基づき、適切な回転数を選定します。送り速度は加工精度と表面仕上げに影響を与えるため、試験加工を通じて最適値を見つけることが推奨されます。これにより、生産性と品質の向上が期待できます。
旋盤加工トラブルを防ぐための基本知識と対策
旋盤加工は、精密な部品を作るための重要なプロセスですが、その過程で予期しないトラブルが発生することも少なくありません。「旋盤加工中にトラブルが発生したらどうすれば良いのだろう?」と悩んでいる方も多いのではないでしょうか。そんな悩みにお応えするために、本記事では旋盤加工におけるトラブルを防ぐための基本知識と実践的な対策をお伝えします。
旋盤加工が初めてで、どこから手を付ければよいのか迷っている方、トラブルの原因を知りたい方、または改善策を探している方にとって、本記事は役立つ情報が満載です。具体的なトラブルの事例や、それを解決するためのヒントを紹介し、旋盤加工をよりスムーズに進められるようサポートします。旋盤加工のスキルを向上させ、安心して作業を進めるための第一歩を踏み出しましょう。
1. 旋盤加工中のトラブルを解決するためのヒント
旋盤加工中にはさまざまなトラブルが発生することがあります。これらのトラブルを未然に防ぎ、円滑に作業を進めるためのヒントを以下にまとめました。
1-1. 旋盤加工の基本知識
旋盤加工は、回転する材料を切削工具で削ることによって、外形や内径を加工する方法です。主に金属やプラスチックを対象とし、精密な形状の部品を製造します。
- 基本的なプロセス:材料をチャックで固定し、工具が回転する材料に接触して削ります。切削速度、送り速度、切込み深さの調整が重要です。
- 工具の種類:旋盤で使用する工具には、バイト、ドリル、タップ、リーマなどがあり、各種工具を使い分けます。
1-2. よくあるトラブルとその原因
旋盤加工で発生しやすいトラブルとその原因は次の通りです:
- 工具の摩耗:切削中に工具が摩耗し、仕上がりが不良になることがあります。原因としては、過度の切削速度や不適切な工具の選定が挙げられます。
- 振動(チャタリング):加工中に発生する振動で、表面仕上げが荒くなる原因となります。原因には、機械の不安定な設置や切削パラメータの不適切さがあります。
- バリの発生:部品の切断面にバリが残ることがあります。これにより、品質が低下します。原因は、切削角度や送り速度の不適切さです。
1-3. 切削加工での加工不良を防ぐためのポイント
加工不良を防ぐためのポイントは以下の通りです:
- 適切な切削条件の設定:切削速度、送り速度、切込み深さを材料に応じて最適化します。過度の負荷がかからないように調整します。
- 冷却・潤滑の強化:冷却液を使用して、加工時の温度を適切に管理します。これにより工具の摩耗や材料の変形を防ぎます。
- 工具の状態チェック:工具の摩耗状態を定期的にチェックし、交換や再研磨を行います。
1-4. 初心者が知っておくべき高品質な加工の実現方法
初心者が高品質な加工を実現するためには、以下の基本的なポイントを押さえておくことが重要です:
- 工具の選定:使用する材料に最適な工具を選びます。工具が適切でないと、加工中に問題が発生しやすくなります。
- 適切な切削条件:加工する材料に合わせて切削速度、送り速度、切込み深さを設定します。これを守ることで、高精度で仕上げられます。
- 機械のメンテナンス:旋盤自体のメンテナンスも重要です。ガタつきや不具合がないように定期的にチェックします。
1-5. 旋盤のガタつきを解消するための対策
旋盤のガタつきは、加工精度に大きく影響を与えます。ガタつきを解消するための対策としては:
- 機械の調整:旋盤の各部分(ガイド、ベアリング、チャックなど)を定期的に調整し、緩みや摩耗を防ぎます。
- 機械の設置環境の確認:旋盤はしっかりと平坦な場所に設置する必要があります。設置面が不安定だと、加工精度が低下します。
- 適切な潤滑:旋盤の動作部位に適切な潤滑を施し、スムーズな動作を確保します。
1-6. 加工時の具体的な手順とコツ
旋盤加工を行う際の具体的な手順とコツは以下の通りです:
段階的な切削:一度に大きく削りすぎず、段階的に切削を進めていきます。これにより、加工中の材料の変形や切削工具の負担を減らすことができます。
準備:材料を適切にチャックに固定し、工具を正確にセットします。材料がしっかりと固定されていないと、加工中にブレや誤差が生じます。
切削条件の設定:適切な切削速度や送り速度を設定し、加工中に過負荷がかからないように注意します。最初は軽い設定で試し、徐々に調整します。
段階的な切削:一度に大きく削りすぎず、段階的に切削を進めていきます。これにより、加工中の材料の変形や切削工具の負担を減らすことができます。
まとめ
旋盤加工トラブルを防ぐためには、適切な工具選定、切削条件の最適化、定期的なメンテナンスが重要です。材料の特性を理解し、加工前に十分な準備を行うことで、精度向上と不具合の軽減が図れます。トラブル発生時には迅速な原因分析と対策が求められます。
加工業界必見!旋盤での切削熱のコントロール方法とその効果
旋盤を用いた加工において、切削熱は避けて通れない重要な要素です。「加工中の切削熱をどうにかコントロールできれば、仕上がりも向上するのに…」と悩んでいる方も多いのではないでしょうか?そこで本記事では、旋盤での切削熱のコントロール方法とその効果について詳しく解説します。
このガイドは、以下のような疑問を抱いている方に最適です:
- 切削熱とは具体的に何か、なぜそれが問題になるのか知りたい。
- 加工中の切削熱を効果的に抑える方法を学びたい。
- 切削熱をコントロールすることで得られるメリットや、実践的なアドバイスが知りたい。
旋盤加工の精度や耐久性を高めるためには、切削熱の管理が不可欠です。この記事を通じて、切削熱の基本からそのコントロール方法まで、幅広く掘り下げていきますので、ぜひ最後までご覧ください。あなたの加工技術をさらに高めるための情報をお届けします。
1. 加工中の切削熱をコントロールするための方法
切削加工中に発生する切削熱は、加工精度や工具寿命に大きな影響を与えます。ここでは、切削熱の発生原因やそのコントロール方法、そして加工硬化への対応策を詳しく解説します。
1-1. 切削加工中の温度が高くなる原因
切削加工中に温度が高くなる主な原因は以下の通りです:
- 切削速度の過剰:切削速度が速すぎると、摩擦が増えて切削熱が発生しやすくなります。
- 切削条件の不適切さ:送り速度や切込み量が不適切な場合、切削抵抗が増加し、熱がこもりやすくなります。
- 工具の摩耗:工具の摩耗が進むと、摩擦が増え、熱が発生しやすくなります。
- 材料の特性:材料によっては熱伝導率が低く、切削熱が逃げにくいため、温度が高くなりやすいです。
1-2. 切削熱を効果的にコントロールする方法
切削熱を効果的にコントロールするための方法には、以下のアプローチがあります:
- 適切な切削条件の設定:切削速度や送り速度を適正に設定することで、過剰な熱の発生を抑えます。
- 冷却液の使用:冷却液を適切に使用することで、切削熱を効率的に除去できます。冷却液の選定や供給方法が重要です。
- 工具の適切な選定:高温に強いコーティングされた工具や、熱伝導性に優れた材料を選ぶことで、熱の発生を抑えることができます。
- 工具の角度調整:工具の切削角度を最適化することで、切削抵抗を減少させ、熱の発生を抑制します。
1-3. 加工硬化の影響とその対策
加工硬化は、材料が切削中に硬化する現象で、これが進行すると工具摩耗が急速に進行します。対策としては:
- 切削速度の調整:高すぎる切削速度は加工硬化を促進するため、適切な速度を選択します。
- クーラントの使用:冷却液や潤滑油を適切に使用することで、加工硬化を防ぎ、材料の温度上昇を抑えることができます。
- 反復加工の回避:同じ箇所を繰り返し加工すると硬化が進みやすいため、一度に必要な深さを加工するようにします。
1-4. フライス加工における熱負荷の管理
フライス加工では、工具と材料の接触面積が大きくなるため、特に熱負荷の管理が重要です:
- ツールパスの最適化:フライス加工中のツールパスを最適化し、切削力や熱の集中を避けるようにします。
- 工具の冷却:工具と材料の接触部分に冷却液を直接供給することで、温度の上昇を防ぎます。
- 切削パラメータの調整:送り速度や切削深さを調整することで、熱負荷を分散させ、工具の過熱を防止します。
1-5. 加工時に樹脂の熱劣化を防ぐ方法
樹脂材料の加工では、過剰な熱によって材料が劣化することがあります。これを防ぐための方法は:
工具の選定:樹脂加工に適した工具を選ぶことで、熱の発生を最小限に抑えることができます。
低速での加工:樹脂は高温に弱いため、低速で加工を行い、熱の蓄積を避けます。
冷却の強化:樹脂に適した冷却液を使用し、加工中に熱を効率的に除去します。
工具の選定:樹脂加工に適した工具を選ぶことで、熱の発生を最小限に抑えることができます。
まとめ
旋盤での切削熱のコントロールは、加工精度や工具寿命に大きく影響します。冷却剤の適切な使用や切削条件の最適化が重要です。これにより、熱変形を防ぎ、仕上がり品質を向上させることができます。さらに、切削熱の管理は生産効率の向上にも寄与します。
黄銅を使った旋盤加工をマスターするための基本知識とポイント
黄銅を使った旋盤加工は、金属加工の中でも特に魅力的な技術です。しかし、「どこから手を付ければいいのかわからない」「黄銅の特性を活かした加工方法を知りたい」と感じている方も多いのではないでしょうか?そんな悩みを解決するために、本記事では「黄銅を使った旋盤加工をマスターするための基本知識とポイント」を徹底解説します。
このガイドは、以下のような方々に最適です。
- 黄銅旋盤加工の基礎を学びたい方
- より精度の高い加工を目指している方
- 成功する加工のコツやポイントを知りたい方
旋盤加工は、技術や経験が重要な分野ですが、正しい知識と適切なコツを身につけることで、あなたの加工技術は大きく向上します。黄銅の特性を理解し、それを最大限に活かす方法を学びましょう。このガイドを通じて、旋盤加工の世界を一緒に探求していきましょう!
1. 黄銅旋盤加工のコツとポイントを徹底解説
黄銅はその加工性の良さから、さまざまな精密部品の制作に利用されています。黄銅旋盤加工を行う際のポイントやコツを押さえ、仕上がりを良くするための方法を解説します。
1-1. 黄銅の特性と加工方法の基本
黄銅は、銅と亜鉛の合金で、耐腐食性や加工性に優れた特性を持っています。旋盤加工を行う際には以下の点を意識することが重要です:
- 柔らかさ:黄銅は比較的軟らかい金属であるため、加工中に材料が変形しやすいです。そのため、慎重に切削を行う必要があります。
- 熱伝導性:黄銅は優れた熱伝導性を持つため、加工中に温度が上昇しやすいです。冷却のために適切な切削液を使用することが重要です。
1-2. 黄銅旋盤加工の仕上がりを良くするためのテクニック
黄銅旋盤加工の仕上がりを良くするためのテクニックは以下の通りです:
- 切削速度の調整:黄銅は軟らかい素材であるため、高速回転ではなく、中速での切削が最適です。切削速度が速すぎると、部品表面に傷が付きやすくなります。
- 送り速度の管理:切削中の送り速度は、あまり速すぎないように設定し、均一な仕上がりを得ることが重要です。
- 仕上げの切削:仕上げ加工の際は、粗削り後のバリや残りかすを取り除き、精度の高い仕上げを行うことが大切です。
1-3. 特定の真鍮素材(C2801やC3604)の加工における注意点
C2801やC3604などの特定の真鍮素材を加工する際の注意点は以下の通りです:
- C2801:この真鍮は、強度が高く、耐腐食性に優れていますが、切削中に工具が摩耗しやすいため、切削工具の選定に注意が必要です。
- C3604:この真鍮は、機械加工性が非常に良いため、旋盤加工には適していますが、硬さの違いにより切削条件を適切に設定する必要があります。
1-4. タップ加工における黄銅の特性とコツ
黄銅を使用したタップ加工のコツは以下の点です:
- 切削油の使用:黄銅のタップ加工には、切削油をしっかりと使用することで、摩擦を軽減し、タップの寿命を延ばすことができます。
- タップの選定:黄銅用のタップを選ぶことが重要です。強度や形状が適切なタップを選定することで、加工精度が向上します。
- 回転速度と進行速度:タップ加工では、回転速度を適切に設定し、過度な進行速度を避けることで、タップの破損や仕上がりの不良を防げます。
1-5. 切削加工における真鍮の加工性と効率的な方法
真鍮の切削加工を効率的に行うための方法は以下の通りです:
加工環境の最適化:加工中の温度や湿度を管理し、安定した加工環境を整えることで、仕上がりの精度を向上させることができます。
冷却と切削液の使用:真鍮は熱伝導性が高いため、切削中に十分な冷却が必要です。切削液を適切に使用することで、工具の寿命を延ばし、加工精度を保つことができます。
切削工具の選定:真鍮に適した切削工具を選ぶことで、切削の効率を最大化できます。特に、耐摩耗性の高い工具を選ぶことが大切です。
まとめ
黄銅を使った旋盤加工では、適切な切削工具の選定や回転速度の調整が重要です。切削油の使用で熱を抑え、仕上がりを向上させます。また、黄銅の特性を理解し、加工条件を最適化することで、精度の高い仕上げが可能になります。定期的なメンテナンスも忘れずに。
部品制作を外注する際に知っておくべき重要なステップとヒント
部品制作を外注することを考えていますか?しかし、「どのように外注を進めれば良いのか分からない……」というお悩みを抱えている方も多いのではないでしょうか。そこで、私たちは「部品制作を外注する際に知っておくべき重要なステップとヒント」というガイドを用意しました。
この記事では、外注を成功させるための重要な知識や、実際にどのように進めていけばよいのか、具体的なステップについて詳しく解説します。特に、「外注先を選ぶ際のポイント」や「見積もりを取得する方法」、「納期や品質管理の重要性」など、実践的なヒントも盛り込みました。
外注をうまく活用することで、コストを削減しながら、高品質な部品を効率的に手に入れることができます。この機会に、部品制作の外注についての理解を深め、ビジネスに役立ててみませんか?それでは、具体的なステップに入っていきましょう。
1. 部品制作を外注する際に必要な知識
部品制作を外注する際には、適切な知識と準備が求められます。外注のプロセスを理解することで、効率的かつ円滑に部品を製作することができます。
1-1. 外注の基本概念とメリット
外注とは、自社で製造するのではなく、外部の企業や専門業者に製造を委託することです。これには以下のようなメリットがあります:
- コスト削減:自社で設備や人員を抱える必要がないため、初期投資を抑えることができます。
- 専門技術の活用:専門業者に依頼することで、技術的に高度な部品や精密な加工が可能になります。
- 柔軟な対応:需要に応じて外注先を変更できるため、生産量や納期に柔軟に対応できます。
1-2. 部品制作を外注する際の依頼方法
外注を依頼する際には、具体的な部品の仕様や要求事項をしっかり伝えることが重要です。以下の手順を参考にしてください:
- 詳細な図面と仕様書の作成:部品の寸法、材質、仕上げ方法などを含んだ詳細な図面を準備します。
- 納期と数量の確認:必要な部品の納期と数量を確認し、外注先に伝えます。
- 見積もり依頼:外注先に見積もりを依頼し、価格や納期、品質を確認します。
- 契約の締結:契約内容には、価格、納期、品質、納品方法などを明確に記載し、双方が合意することが大切です。
1-3. 外注先の選定基準
外注先を選定する際には、以下のポイントを基準に選ぶことが重要です:
- 技術力:部品の要求精度や加工技術に対応できる能力があるかを確認します。
- 納期の遵守:納期を守ることができる信頼性の高い企業かどうかを調査します。
- 品質管理:品質管理体制が整っているか、過去の納品実績などをチェックします。
- コスト:見積もりが適正か、他の業者と比較してコストパフォーマンスが良いかを検討します。
2. 部品制作を外注する際に必要な知識と納品までの流れ
部品制作を外注する際には、依頼から納品までのプロセスをしっかりと把握することが重要です。以下の流れを理解することで、スムーズな進行が可能になります。
2-1. 外注先とのコミュニケーションの重要性
外注先との円滑なコミュニケーションは、納期や品質の確保に欠かせません。以下のポイントに留意することが大切です:
- 定期的な進捗確認:加工の進行状況を定期的に確認し、問題が発生していないかをチェックします。
- 変更事項の連絡:仕様変更や納期変更があった場合には、早めに外注先に伝えることが重要です。
- フィードバックの提供:納品後に品質や納期に関するフィードバックを行い、次回の改善点を共有します。
2-2. 納品スケジュールの設定と管理
納品スケジュールを設定し、管理することで遅延を防ぎ、納期通りに部品を受け取ることができます:
- 納期の確定:部品の製造に必要な時間を見積もり、納期を設定します。
- リードタイムの確認:製造から納品までのリードタイムを確認し、余裕を持たせたスケジュールを設定します。
- 進行状況の把握:外注先に進捗状況を確認し、問題がないかを確認します。
2-3. 品質管理と検品のポイント
納品された部品が仕様通りであることを確認するため、品質管理と検品が必要です:
品質保証:納品後の保証期間を設定し、万が一の不具合に備えます。
受入検査:納品された部品が図面通りに製作されているか、寸法や仕上がりを確認します。
不良品対応:不良品があった場合は、外注先と連携して再製作や調整を行います。
3. 部品制作を外注する際に必要な知識と機械加工の基礎
部品制作を外注する際、機械加工に関する基本的な知識が不可欠です。加工のプロセスや方法を理解することで、より適切な外注先の選定や依頼が可能になります。
3-1. 機械加工の基本用語とプロセス
機械加工とは、金属やプラスチックなどの素材を、工具を使用して所定の形状に加工するプロセスです。以下の基本用語とプロセスを理解することが大切です:
- 切削:素材から余分な部分を削り取って形を作る加工。
- フライス加工:回転するフライス盤を使用して素材を削る加工法。
- 旋盤加工:回転する素材に工具を当てて形を削る加工法。
- 研削:表面を平滑に仕上げるために、研削盤を使用する加工。
3-2. 加工方法の種類と選び方
加工方法にはいくつかの種類があり、それぞれの方法に特徴があります。以下の基準で最適な加工方法を選定します:
- 精度が必要な場合:旋盤加工やマシニングセンタを使用したフライス加工などが適しています。
- 大量生産の場合:自動化された加工方法(例:NC旋盤)やダイカストが効率的です。
- 複雑な形状の部品:ワイヤーカットや放電加工が有効です。
3-3. 外注先に求める技術力
外注先に求める技術力には以下の要素があります:
- 精密な加工技術:部品の精度が要求される場合、外注先が持つ加工技術のレベルが重要です。
- 多様な加工手段:複数の加工方法に対応できる能力を持っていることが望ましいです。
- 材料の取り扱い能力:特定の金属や合金の加工が得意であることが求められます。
4. 部品制作を外注する際に必要な知識と購買・外注管理
部品制作の外注を成功させるためには、購買や外注管理の知識も不可欠です。これらをしっかり理解することで、外注プロセスを円滑に進めることができます。
4-1. 購買プロセスの理解
部品制作を外注する際には、適切な購買プロセスを理解しておくことが重要です:
- ニーズの確認:必要な部品の仕様や数量を明確にします。
- 見積もり依頼:複数の外注先に見積もりを依頼し、価格、納期、品質を比較します。
- 発注と契約:最適な外注先を選定し、発注契約を結びます。
4-2. 外注管理のベストプラクティス
外注管理は、納期や品質を守るために重要な要素です。以下のベストプラクティスを実践しましょう:
- 進捗管理:定期的に外注先と連絡を取り、進捗状況を確認します。
- 品質チェック:納品された部品が品質基準を満たしているかを確認します。
- 問題解決の迅速化:問題が発生した場合、迅速に対応し、外注先と協力して解決します。
4-3. コスト管理と予算設定
コスト管理と予算設定は、部品制作の外注において非常に重要です:
リスク管理:納期遅れや品質不良などのリスクを考慮し、リスク管理計画を立てます。
予算設定:部品の単価や納期を基に、予算を設定します。予算を守るために見積もりの段階でしっかり確認しましょう。
コスト削減の工夫:材料費や加工費用の見直しを行い、コスト削減を図ります。
まとめ
部品制作を外注する際は、まず明確な仕様書を作成し、信頼できる業者を選定することが重要です。見積もりを比較し、納期や品質管理の体制を確認しましょう。また、契約書には詳細な条件を明記し、定期的なコミュニケーションを心掛けることで、トラブルを防げます。
【旋盤加工のプロが教える!真鍮・黄銅・砲金の仕上げ精度を高める方法】
あなたは「旋盤加工をしているけれど、仕上げ精度をもっと高めたい…」と悩んでいませんか?それなら、この記事はまさにあなたのためにあります。旋盤加工のプロが、真鍮、黄銅、砲金の仕上げ精度を向上させるための具体的な方法をお伝えします。
このガイドでは、以下のような疑問を解決していきます。
- 旋盤加工における仕上げ精度とは何か?
- 真鍮や黄銅、砲金の特性と、それに適した加工方法は?
- 精度を高めるためのポイントやテクニックは?
旋盤加工は、工作物を高精度で仕上げるための重要な技術ですが、素材によって求められる技術やアプローチが異なります。本記事を通じて、旋盤加工の基礎から応用までを学び、あなたの技術を一段と向上させる手助けができれば幸いです。それでは、真鍮や黄銅、砲金の加工の世界へ、一緒に踏み出していきましょう!
1. 旋盤での仕上げ精度向上方法:真鍮、黄銅、砲金の基本
旋盤加工における仕上げ精度は、製品の品質に大きく影響します。真鍮、黄銅、砲金はそれぞれ特性が異なるため、仕上げ精度向上のためのアプローチも異なります。
1-1. 旋盤加工の基礎知識
旋盤加工は、回転する材料を切削工具で削りながら加工する方法で、円形の部品を精密に仕上げるために使用されます。加工精度を高めるためには、適切な切削条件や工具の選定が重要です。
1-2. 仕上げ精度とは何か
仕上げ精度は、加工後の部品の寸法や表面の状態を指し、これが高いほど、部品の品質が高いと評価されます。高精度な仕上げを実現するためには、加工中の振動や温度変化を抑え、安定した条件で加工を行う必要があります。
2. 旋盤での仕上げ精度向上方法:真鍮、黄銅、砲金の具体的手法
真鍮、黄銅、砲金における仕上げ精度を向上させるためには、切削条件や工具の選定が非常に重要です。以下に、精度向上のための具体的な手法を紹介します。
2-1. 切削条件の最適化
- 切削速度の調整:
切削速度が速すぎると、工具の摩耗や材料の熱膨張を引き起こし、精度に影響を与える可能性があります。反対に遅すぎると、加工効率が悪くなるため、最適な切削速度を設定することが重要です。 - 切削深さの設定:
適切な切削深さを設定することで、表面の仕上がりが向上します。深すぎる切削は精度を低下させるため、段階的に加工を行うことが推奨されます。
2-2. 適切な工具の選定
- 工具材質:
真鍮、黄銅、砲金などの材料に対して、工具の材質や形状を選ぶことが重要です。硬度が高い工具を使用することで、摩耗を防ぎ、長期間安定した切削が可能になります。 - 工具の鋭利さ:
鋭利な工具を使用することで、より精度の高い仕上げが可能となります。特に仕上げ加工では、工具の先端角度や形状にも注意を払うことが求められます。
2-3. 加工速度と送り速度の調整
- 送り速度の調整:
送り速度が速すぎると、仕上げ精度が悪化し、表面が粗くなります。適切な送り速度で加工することで、滑らかな表面を得ることができます。 - 加工速度と精度のバランス:
高速加工を目指す場合でも、精度を犠牲にしないように調整が必要です。特に精密部品の場合は、適切なバランスを見つけることが大切です。
3. 黄銅や真鍮の加工時の注意点
真鍮や黄銅は、銅をベースとした合金であり、材料特性に基づいた加工が求められます。以下のポイントに注意しながら加工を進めることが重要です。
3-1. 材料特性の理解
- 真鍮や黄銅の特性:
真鍮は加工しやすく、表面が美しいため、装飾部品や精密機器部品に利用されますが、強度が銅に比べてやや低いという特徴があります。これに対して黄銅は、真鍮よりも耐食性や強度に優れています。 - 加工時の温度管理:
高温下では真鍮や黄銅が変形しやすいため、加工時の温度管理をしっかり行う必要があります。特に切削中に発生する熱を適切にコントロールすることが精度向上に寄与します。
3-2. 加工中の熱管理
- 冷却液の使用:
切削時の熱を管理するためには、冷却液の使用が効果的です。適切な冷却液を使用することで、工具の摩耗を抑え、仕上げ精度を高めることができます。 - 熱膨張への対策:
真鍮や黄銅は熱膨張が大きいため、加工前に冷却を行い、熱膨張の影響を最小限に抑える工夫が求められます。
3-3. 切削液の選び方
選定のポイント:
高い冷却性能を持ち、腐食を防ぐ成分が含まれている切削液を選ぶことで、加工精度の向上が期待できます。特に、真鍮や黄銅には、無腐食タイプの切削液が推奨されます。
切削液の役割:
切削液は、摩擦を減らし、工具の冷却と切削面の潤滑を行います。特に真鍮や黄銅では、適切な切削液を選定することが重要です。
4. NC旋盤での特定の加工に関する具体的な質問解決
NC旋盤(数値制御旋盤)は、精密な加工が可能な機械で、様々な金属の部品加工に利用されています。特定の加工に関する問題を解決するために、以下の重要なポイントを押さえておきましょう。
4-1. NC旋盤の基本操作
NC旋盤は、コンピュータプログラムによって制御される旋盤です。プログラムに従って工具の位置や動きを正確に制御し、部品の加工を行います。基本操作には、以下のようなステップがあります:
- プログラムの入力:加工する部品の図面に基づいて、必要な加工情報(切削深さ、送り速度、回転速度など)をプログラムに入力します。
- 機械のセットアップ:材料を機械に固定し、工具を適切にセットします。
- 加工の開始:プログラムに従って自動で加工が行われます。
4-2. よくあるトラブルとその対策
NC旋盤でよく見られるトラブルとその対策には以下のようなものがあります:
- 振動:加工中に振動が発生すると、精度が低下することがあります。振動を抑えるためには、切削条件を調整するか、機械の安定性を確認します。
- 工具の摩耗:長時間の使用で工具が摩耗し、精度が落ちることがあります。定期的に工具を交換したり、適切な切削液を使用することが効果的です。
- 寸法誤差:加工後の部品が図面通りでない場合、プログラムの設定ミスや機械の調整不良が原因です。定期的な校正や、プログラムの再確認が必要です。
4-3. 加工プログラムの作成方法
NC旋盤の加工プログラムは、CAD/CAMソフトを使用して作成することが一般的です。以下の流れでプログラムを作成します:
- 部品の図面を作成:加工する部品の寸法や形状を詳細に記載します。
- 加工順序の決定:各工程(粗加工、仕上げ加工など)を順番に設定します。
- CAMソフトでのプログラム作成:図面を基に、切削速度、送り速度、工具の選定などを設定し、NC旋盤用のプログラムを作成します。
- プログラムの検証:仮想加工でプログラムの動作を確認し、エラーがないことを確認します。
5. 黄銅と真鍮の違いや特性を理解して使い分ける
黄銅と真鍮は、どちらも銅を基盤とした合金ですが、性質が異なり、用途にも違いがあります。それぞれの特性を理解し、適切な材料を選択することが重要です。
5-1. 黄銅の特性と用途
- 特性:黄銅は、銅に亜鉛を主成分とする合金で、優れた耐食性や強度を持っています。加工が容易で、比較的低コストで製造可能です。
- 用途:黄銅は、装飾品や機械部品、コインなどの用途に広く使用されています。耐食性が求められる場面で特に役立ちます。
5-2. 真鍮の特性と用途
- 特性:真鍮は、銅に亜鉛を加えた合金で、金色の外観が特徴です。真鍮は黄銅よりも柔らかく、熱や電気の導通性が優れています。
- 用途:真鍮は、音響機器や精密機械部品、電気接続部分など、特に導電性や美観が重要な部分に利用されます。
5-3. 適切な材料選定のポイント
- 強度が求められる場合:黄銅を選ぶと良いでしょう。黄銅は強度が高く、耐摩耗性にも優れています。
- 導電性や美観が求められる場合:真鍮を選ぶと、より適しています。特に美しい金色が重要な場合や、導電性が必要な場合に最適です。
6. 銅合金の加工方法やポイントを学ぶ
銅合金は、様々な種類があり、それぞれ異なる特性を持っています。銅合金を加工する際には、特性に応じた方法を選択することが重要です。
6-1. 銅合金の種類と特性
- C3604(黄銅):加工性が非常に高く、主に精密機器部品や配管に使用されます。耐腐食性も高いです。
- C3771(砲金):耐摩耗性や耐食性が非常に高いですが、加工はやや難しいため、特別な技術が求められます。
6-2. 加工時の注意点
- 熱管理:銅合金は熱膨張が大きいので、加工時に適切な冷却が必要です。
- 工具の摩耗:銅合金は比較的柔らかいため、工具が摩耗しやすいです。切削条件を調整して、工具寿命を延ばすことが重要です。
6-3. 仕上げ精度向上のためのヒント
工具の選定:銅合金に適した工具を使用することで、より精密な仕上げが可能になります。特に硬度が高い工具を選択すると、長寿命化が期待できます。
切削条件の最適化:切削速度や送り速度を適切に設定することで、仕上がりが向上します。特に仕上げ加工では細かな設定が求められます。
まとめ
旋盤加工において、真鍮・黄銅・砲金の仕上げ精度を高めるためには、適切な工具選定と切削条件の設定が重要です。冷却材の使用や加工速度の調整、仕上げ段階での微細加工を行うことで、表面品質を向上させることができます。また、定期的な工具のメンテナンスも精度維持に寄与します。
プロが教える真鍮の旋盤加工テクニックと応用例
真鍮加工の世界に興味を持っていますか?「真鍮の旋盤加工に挑戦したいけれど、基本やテクニックが分からない…」という悩みを抱えている方も多いことでしょう。そんなあなたのために、この記事では「真鍮加工の極意:旋盤加工の基本から応用まで」をお届けします。
このガイドを通じて、真鍮加工の基礎知識や旋盤加工の基本から、実践的な応用技術までを詳しく解説します。真鍮は、その美しい色合いや優れた加工性から、様々な製品に利用されており、旋盤加工はその魅力を引き出す重要な技術です。
「どうやって始めれば良いかわからない」、「旋盤加工の具体的なテクニックを知りたい」と思っている方にとって、必要な情報が満載です。あなたの加工技術を一歩進めるための手助けとなるよう、わかりやすく解説を進めていきますので、ぜひ最後までご覧ください。真鍮加工の魅力を共に探求していきましょう!
1. 真鍮加工の極意:旋盤加工の基本から応用まで
真鍮はその優れた機械的特性や加工性から、金属加工業界で非常に人気のある素材です。旋盤加工を用いて、精密な部品や美しい仕上がりを実現するためには、基本的な技術から応用まで幅広い知識が求められます。
1-1. 旋盤加工とは何か
- 旋盤加工の概要:
旋盤は、回転する材料に対して切削工具を当てて加工する機械で、円筒形や円錐形の部品を作成するために使用されます。回転する工作物と切削工具の相対的な動きによって、金属の除去が行われ、部品の形状が整えられます。 - 旋盤加工の用途:
旋盤加工は、精密部品の製造に欠かせない技術であり、真鍮やアルミニウムなどの軟金属、さらには硬金属の加工にも適しています。特に、自動車部品、航空機部品、精密機器などの製造に広く利用されます。
1-2. 真鍮の特性とその加工の重要性
- 真鍮の物理的特性:
真鍮は、銅と亜鉛を主成分とする合金で、耐食性、加工性、そして良好な機械的特性を持ち合わせています。その特性により、さまざまな形状の部品を精密に加工することが可能です。 - 加工における重要性:
真鍮は切削加工が容易であるため、旋盤を使って非常に精密な加工が可能です。適切な切削速度と工具選定を行うことで、部品の精度や美しい仕上がりを実現できます。
1-3. 旋盤加工の基本技術
- 工具の選定:
旋盤加工では、素材に合った切削工具の選定が重要です。真鍮には硬度や強度を考慮した適切な工具を選び、加工の精度と仕上がりを確保します。 - 回転数の設定:
回転数は、使用する材料や工具、切削条件によって最適化する必要があります。高回転数での加工が可能な真鍮においては、過度な摩耗を防ぐために適切な設定が求められます。
1-4. 真鍮加工における最適な切削速度
- 切削速度の影響:
真鍮の切削速度は、加工時間や仕上がりに大きく影響します。速すぎる切削速度は工具の摩耗を早め、遅すぎると加工効率が低下します。一般的に、真鍮の切削速度は中程度が推奨されます。 - 切削条件の調整:
仕事の精度を高めるために、切削速度だけでなく、送り速度や切削深さも重要な要素となります。真鍮の加工では、適切な条件を設定することで、高精度な仕上がりを得ることができます。
1-5. 最新の切削技術とその応用
- 高効率切削技術:
高速回転を活用した切削技術や、クーラントを活用した冷却技術は、真鍮の加工精度を向上させるために重要な役割を果たします。これらの技術を活用することで、より高速かつ精密な加工が実現できます。 - CNC旋盤技術の活用:
CNC(コンピュータ数値制御)旋盤は、精密なプログラミングにより非常に高精度な加工を実現します。プログラムによる自動化により、安定した品質の製品を効率よく生産することができます。
1-6. 真鍮の切削加工の具体的な方法
- 荒加工と仕上げ加工:
真鍮を加工する際には、荒加工で粗い形状を削り取った後、仕上げ加工で精密な形状を整えます。これにより、最終的に高い精度を持つ部品を得ることができます。 - 切削液の使用:
切削中の摩擦や熱を抑えるため、適切な切削液を使用します。真鍮の加工には、特に清浄で冷却性の高い切削液が推奨されます。
1-7. 美しい仕上がりを実現するためのコツ
研磨技術の活用:
仕上げ加工後には研磨を行い、さらに滑らかな仕上がりを目指します。真鍮の表面に磨きがかかることで、製品の美しさと耐久性が向上します。
仕上げ方法の工夫:
真鍮は切削後の仕上げが重要です。表面処理を施すことで、美しい光沢を出すことができます。また、仕上げ加工では微細な欠陥を取り除き、表面を滑らかにすることが求められます。
まとめ
真鍮の旋盤加工は、精密な部品作成に欠かせない技術です。プロのテクニックとしては、切削速度や工具の選定、冷却材の使用が重要です。応用例としては、時計部品や楽器パーツが挙げられ、これらは真鍮の特性を活かした美しい仕上がりが求められます。正しい技術を習得することで、品質の高い製品が生まれます。
黄銅部品制作を依頼する際のチェックリスト
黄銅部品の制作を考えている皆さん、そんな時に気になるのが「何をチェックすればよいのか?」というポイントではありませんか?特に、初めて依頼する場合や複雑な部品を必要としている場合、注意すべき点は多岐にわたります。そこで、この記事では「黄銅部品制作を依頼する際のチェックリスト」をご紹介します。
このリストは、以下のような疑問を持つ方々に向けています。
- 黄銅部品を依頼する際に必要な情報は何ですか?
- 信頼できる業者を選ぶための基準は?
- 部品の仕様や材質について、どのように伝えれば良いのか?
黄銅はその特性から多くの産業で利用されており、適切な部品制作を行うことが業務の成功に直結します。依頼時に失敗を避けるためのポイントをしっかりと抑えて、安心して制作を進めましょう。それでは、具体的なチェックリストを見ていきましょう。
1. 黄銅部品制作を依頼する際のポイント
黄銅部品は、金属加工において広く使用される素材であり、その特性に基づいて加工方法や依頼のポイントを理解することが重要です。
1-1. 黄銅部品の加工に関する基礎知識
- 黄銅の特性:
- 黄銅は銅と亜鉛を主成分とする合金で、優れた耐腐食性と加工性を持っています。軽量でありながら強度が高く、導電性や熱伝導性にも優れています。これらの特性により、電子機器や配管、金具など幅広い分野で使用されます。
- 加工方法:
- 黄銅は切削性が良いため、旋盤加工やフライス加工が一般的です。また、圧延や鋳造による製造方法もあります。加工時には、適切な切削条件や工具の選定が求められます。
- 加工時の注意点:
- 黄銅は柔らかいため、切削速度や送り速度を適切に設定することが重要です。また、冷却液の使用や切削工具の管理も重要です。
1-2. 黄銅とメッキの違い
- 黄銅:
- 黄銅は金属そのものの合金で、元々の金属の特性(強度、耐食性、耐摩耗性)を活かして使用されます。見た目が金色で美しいため、装飾品や高級品にも使用されます。
- メッキ:
- メッキは、金属の表面に他の金属(例えば、金やクロム)を薄くコーティングする技術です。メッキは主に美観や耐食性の向上、または摩耗に対する保護を目的として使用されます。
- 違い:
- 黄銅はそのままで金属部品として使用され、耐久性や加工のしやすさを重視します。一方、メッキは主に表面の改善が目的であり、耐久性や外観を向上させる役割を持っています。
1-3. 精密部品の加工にかかる費用
- 費用の要因:
- 精密部品の加工には、使用する機械の種類や加工の精度、部品の形状や数量などが影響します。例えば、高精度な加工や特殊な処理が必要な場合、加工費用が高くなります。
- 数量による違い:
- 少量生産では、型を作成するコストや準備作業が費用に加算されるため、単価が高くなります。一方、大量生産の場合は単価が下がりますが、初期投資が必要です。
- 素材の選定:
- 素材自体のコストも影響します。黄銅のように比較的高価な素材を使用する場合、加工費用が上がることがあります。
1-4. 低予算・短納期で金属部品加工を依頼する方法
- 適切な加工方法の選定:
- 低予算や短納期での依頼を考える場合、加工方法を工夫することが重要です。例えば、切削加工よりも圧延や鋳造を利用することで、コストや納期を短縮できる場合があります。
- 標準化された部品の使用:
- 特注品の加工を依頼する際でも、標準化された部品や材料を使用することで、コストを削減できます。規格外のサイズや形状を避けることが、予算を抑えるために有効です。
- 事前に納期と予算を明確に伝える:
- 発注前に納期や予算を明確に伝え、無理のない範囲で作業を依頼することが重要です。予算に合わせて適切な加工方法を提案してくれる業者を選びましょう。
1-5. 初心者が金属加工を依頼する際の流れや注意点
- 依頼の流れ:
- 依頼内容の整理:必要な部品の設計図や仕様書を準備します。
- 業者選び:信頼できる業者を選び、過去の実績や評価を確認します。
- 見積もり依頼:業者に見積もりを依頼し、価格や納期を確認します。
- サンプル製作:必要に応じてサンプルを製作してもらい、品質や精度を確認します。
- 正式発注:サンプルが問題ない場合、正式に発注を行います。
納品後の確認:納品された部品は、必ず品質チェックを行い、問題があればすぐに連絡するようにします。
注意点:
コミュニケーションの確保:依頼内容をしっかり伝え、納期や仕様に関して曖昧な点がないようにします。
納期と予算の調整:予算や納期に関して無理な要求を避け、現実的な範囲で依頼します。
まとめ
黄銅部品制作を依頼する際は、以下のチェックリストを参考にしましょう。まず、設計図や仕様書を明確に用意し、納期や予算を確認します。次に、製造業者の技術力や過去の実績を調査し、材料の品質や加工方法についても確認が必要です。アフターサービスや保証内容も重要なポイントです。これらを押さえることで、スムーズな製作依頼が可能になります。
真鍮部品の製造過程で注意すべき品質管理のポイント
真鍮部品の製造過程において、品質管理は極めて重要な要素です。「どのようにして高品質な真鍮部品を作り上げるのか?」と悩んでいる方も多いのではないでしょうか。製造業に携わる方々が直面する課題や、品質管理において見逃してはいけないポイントを明確にすることで、より効率的で信頼性の高い生産体制を築く手助けをします。
このガイドでは、真鍮部品の品質管理の基本的な考え方から、具体的な手法や注意点までを詳しく解説します。もし、あなたが「真鍮部品の品質を向上させたい」「製造過程におけるトラブルを未然に防ぎたい」と考えているなら、この情報はきっと役立つでしょう。さあ、一緒に品質管理の重要性とそのポイントを探っていきましょう。
1. 真鍮部品の品質管理ポイントとは?
真鍮部品の品質管理は、精度や耐久性を確保するために非常に重要です。品質を確保するための適切な指標とプロセスを理解することが、最終的に高品質な部品を提供する鍵となります。
1-1. 真鍮部品の品質管理の重要性
- 精度の確保:
- 真鍮部品は、機械的強度や耐食性、外観の美しさが求められるため、品質管理をしっかり行うことが必要です。精度が低いと部品としての機能が損なわれるため、加工精度を確保することが最も重要です。
- 生産効率の向上:
- 高品質な製品を一貫して作り続けるためには、品質管理を徹底することが不可欠です。トラブルの発生を未然に防ぐことで、生産効率も向上します。
- コストの削減:
- 品質管理を怠ると、再加工や不良品の発生によるコストが増加します。適切な品質管理を行うことで、無駄なコストを削減することができます。
1-2. 品質管理における主要な指標
- 寸法精度:
- 部品の寸法が設計通りであるかをチェックするために、ゲージや測定機器を使用して寸法精度を管理します。
- 表面仕上げ:
- 真鍮部品の外観は、表面の仕上がりによって大きく影響されます。粗さやキズ、バリなどの表面欠陥を管理することで、品質を向上させます。
- 機械的性質:
- 引張強度、硬度、伸び率などの機械的特性を測定して、部品が求められる性能を満たしているかを評価します。
- 耐食性:
- 真鍮部品が使用環境において腐食しないか、適切なテストを実施し、耐食性を確認します。
1-3. 品質管理のプロセスと手法
- インプロセス管理:
- 加工中にリアルタイムで寸法や品質を監視し、問題が発生した場合にすぐに修正する方法です。これにより、不良品の発生を防ぐことができます。
- 最終検査:
- 加工後に最終的な品質チェックを行い、部品が設計通りに仕上がっているかを確認します。この段階で不良品を発見し、取り除くことで品質を保ちます。
- 統計的品質管理(SQC):
- 生産ラインで得られるデータを統計的に分析し、品質に関する傾向や問題点を把握します。問題が発生する前に予測し、改善措置を取ることができます。
2. 真鍮旋盤加工の際の注意点
真鍮を旋盤加工する際には、特有の注意点があります。これらを理解し、適切に対処することで、良好な加工結果を得ることができます。
2-1. 旋盤加工の基本
- 回転速度と送り速度:
- 真鍮は比較的軟らかい素材なので、切削時には適切な回転速度と送り速度を選ぶ必要があります。過度に高速で回転させると、切り屑が飛び散り、仕上がりが悪くなることがあります。
- 切削工具の選定:
- 真鍮を加工する際には、硬度が低く、耐摩耗性のある工具を使用することが重要です。特に、切削エッジが鈍くなると精度が低下するため、定期的な工具交換が必要です。
- 切削液の使用:
- 真鍮加工時には切削液を使用することで、摩擦を減少させ、工具寿命を延ばし、加工精度を向上させます。冷却効果と潤滑作用を両立させる切削液を選ぶことが重要です。
2-2. 加工中のトラブルとその対策
- 振動の発生:
- 旋盤加工中に振動が発生すると、加工精度が悪化します。これを防ぐためには、工作物をしっかりと固定し、切削条件を適切に設定します。
- 切り屑の詰まり:
- 真鍮は切り屑が大きくなりやすく、詰まりやすい素材です。定期的に切り屑を取り除き、加工がスムーズに進むようにすることが大切です。
- 過熱:
- 真鍮は熱がこもりやすい素材です。過熱を防ぐためには、冷却液を十分に供給し、切削時に適切な速度を選定することが重要です。
2-3. 加工精度を向上させるためのポイント
加工後の仕上げ工程では、精密な測定機器を使って寸法を確認し、必要に応じて微調整を行います。これにより、最終的な精度が向上します。
適切な切削条件の設定:
真鍮の切削には、適切な切削速度、送り速度、切削深さの設定が重要です。これらを最適化することで、精度の高い仕上がりを得ることができます。
工具のメンテナンス:
高精度な加工を維持するために、工具のメンテナンスを怠らないようにします。工具の鋭利さを保つことで、仕上がりがきれいになります。
振動の管理:
加工中の振動は精度に影響を与えるため、振動を最小限に抑えるように加工環境を整えることが重要です。
仕上げ加工の最適化:
加工後の仕上げ工程では、精密な測定機器を使って寸法を確認し、必要に応じて微調整を行います。これにより、最終的な精度が向上します。
3. 真鍮加工の基本的な知識
真鍮は金属部品として非常に広く使用される素材です。加工時にその特性を理解し、適切な方法と工具を選定することが重要です。
3-1. 真鍮の特性と利点
- 加工性:
- 真鍮は比較的柔らかく、切削や加工がしやすい素材です。このため、複雑な形状や細かい部品の製造にも適しています。
- 耐食性:
- 真鍮は耐腐食性に優れ、特に湿気や水に強い特徴があります。これにより、水道機器や海洋機器などに多く使用されます。
- 導電性と熱伝導性:
- 真鍮は良好な導電性を持つため、電気機器や電子機器の部品に使用されることが多いです。また、熱伝導性も良好で、熱を効率的に伝える用途にも適しています。
- 強度と耐久性:
- 真鍮は強度も十分で、長期間にわたって使用できる耐久性を持ちます。この特性により、金具や機械部品としても利用されています。
3-2. 加工方法の種類と選び方
- 切削加工:
- 真鍮は切削性が良いため、旋盤やフライス盤を使用した切削加工に適しています。精密な寸法が求められる場合は、高精度な切削を選択することが重要です。
- 圧延加工:
- 真鍮を薄く広げる圧延加工も行われます。特にシートや板材として使用する際に有効です。圧延によって、真鍮の表面を滑らかにし、強度を高めることができます。
- 鋳造:
- 真鍮は鋳造にも適した素材で、複雑な形状を作ることができます。鋳造後に仕上げ加工を行うことが一般的です。
- 圧縮成形:
- 真鍮のパイプや棒状の製品を圧縮成形で作ることもあります。この方法は大量生産に向いており、コストを抑えながら大量に部品を製造できます。
- 選び方:
- 加工方法の選定は、製品の形状、サイズ、精度、使用する環境に基づいて決定します。加工方法によって、後工程や仕上げの手間が異なるため、コストや生産効率を考慮して選びます。
3-3. 加工に必要な工具と設備
- 旋盤:
- 真鍮の部品加工には旋盤がよく使用されます。回転するワークに切削工具を当てて加工を行います。精密な仕上がりが求められるため、高精度な旋盤を使用することが望ましいです。
- フライス盤:
- フライス盤は、平面や溝などの加工に使用されます。真鍮の複雑な形状を切削するために利用されることが多いです。
- ボール盤:
- 穴あけ加工にはボール盤が使用されます。特に精度が求められる穴あけを行うために、微調整可能なボール盤が必要です。
- 切削工具:
- 真鍮に適した切削工具を選定することが重要です。通常、硬度が低い真鍮には鋼製の工具を使用しますが、加工内容によってはダイヤモンドコーティング工具やセラミック工具を使うこともあります。
- 研削盤:
- 最後に仕上げや精密な表面処理を行うために、研削盤を使用することがあります。これにより、表面の平滑性や寸法精度が向上します。
4. 金属加工における検査方法や注意点
金属加工では、加工後の品質検査が非常に重要です。検査方法と注意点を理解して、良品を確実に得ることが求められます。
4-1. 検査の種類と目的
- 寸法検査:
- 加工した部品が設計通りの寸法に仕上がっているかを測定します。ゲージやマイクロメーター、ノギスなどの測定器を使用して精密に測定します。
- 表面検査:
- 表面の粗さや傷、バリなどをチェックします。視覚検査や専用の表面粗さ測定機を使用して、部品の外観や機能に影響を与える不良を見つけます。
- 機械的特性検査:
- 引張試験や硬度試験を実施し、部品が求められる機械的性質を持っているかを評価します。特に、耐摩耗性や強度が求められる部品で行います。
- X線検査:
- 厚い金属部品や複雑な形状の部品においては、X線検査を使用して内部の欠陥(気泡やひび割れなど)を確認します。
4-2. 検査時の注意点
- 環境の整備:
- 検査を行う場所は、清潔で安定した環境であることが重要です。温度や湿度などの影響を受けないようにすることが、精度の高い検査を行うために必要です。
- 測定器具の校正:
- 測定器具は定期的に校正を行い、誤差を最小限に抑えることが大切です。校正が不十分な場合、正確な測定ができず、品質に影響を与えることがあります。
- 人為的ミスの回避:
- 検査員が注意深く作業を行い、同じ基準で測定することが大切です。また、測定結果を記録し、後から確認できるようにしておくと信頼性が高まります。
4-3. 検査結果の活用方法
検査結果を基に、品質向上のための具体的な指標を設定することができます。これにより、継続的な品質改善を目指すことが可能になります。
不良品の排除:
検査で不良品を発見した場合、その原因を突き止め、次回の生産に活かすことが重要です。頻繁に同じ問題が発生する場合は、加工プロセス自体の見直しを行います。
工程改善:
検査結果を元に、工程改善を行うことができます。例えば、特定の加工条件が不良品を多く生む場合、条件の見直しや新たな技術の導入を検討します。
品質向上の指標:
検査結果を基に、品質向上のための具体的な指標を設定することができます。これにより、継続的な品質改善を目指すことが可能になります。
まとめ
真鍮部品の製造過程では、原材料の選定、加工精度、熱処理、表面処理が重要です。特に、寸法管理や表面の仕上がり具合を厳密にチェックすることで、耐久性や性能を確保できます。また、定期的な機械メンテナンスと従業員の技術向上も品質向上に寄与します。
旋盤加工の精度を高める!真鍮・黄銅・砲金の加工テクニック解説
旋盤加工は、金属加工の中でも非常に重要な技術であり、さまざまな分野で広く利用されています。しかし、特に真鍮や黄銅、砲金などの素材において、その加工精度は仕上がりのクオリティを大きく左右します。「旋盤加工の精度を高める!真鍮・黄銅・砲金の加工テクニック解説」というタイトルの本記事では、これらの素材に特化した旋盤加工のテクニックを詳しく解説します。
「旋盤加工の精度を向上させたいが、具体的にどうすれば良いか分からない」といったお悩みを抱えるあなたにとって、本記事は最適な情報源です。真鍮や黄銅、砲金の特性を理解し、それに応じた加工法をマスターすることで、高品質な製品を生み出すことが可能になります。
これから紹介する内容を通じて、旋盤加工の精度を向上させるための具体的なテクニックや、注意すべきポイントを学び、あなたの加工技術を一層高めていきましょう。精度を求める旋盤加工において、真鍮、黄銅、砲金を使った加工法は欠かせません。さあ、一緒に深く掘り下げていきましょう!
1. 旋盤加工の精度向上テクニック:真鍮・黄銅・砲金編
旋盤加工における精度向上には、材料の特性に合わせた適切な設定と方法が不可欠です。真鍮、黄銅、砲金それぞれの特性を理解し、加工精度を高めるためのテクニックを紹介します。
1-1. 旋盤加工の精度を向上させるための具体的な方法
- 切削条件の最適化:
- 加工精度を向上させるためには、切削速度、送り速度、切削深さの適切な設定が重要です。これらを最適化することで、振動や熱の発生を抑え、精度を保ちます。
- 適切な工具の選定:
- 高精度な仕上がりを実現するためには、鋭利な切削工具を使用することが不可欠です。特に真鍮や黄銅では工具が摩耗しやすいため、耐摩耗性に優れたコーティングを施した工具を選ぶことが有効です。
- 冷却方法の工夫:
- 加工中の熱の発生を抑えるため、冷却液の使用は必須です。冷却液の選定や流量調整を行うことで、工具の温度上昇を防ぎ、精度を維持します。
1-2. 真鍮や黄銅を加工する際の注意点
- 熱膨張:
- 真鍮や黄銅は熱膨張しやすいため、高温での加工中に変形が発生する可能性があります。これを防ぐためには、冷却液の使用と温度管理を徹底することが重要です。
- 切削中の変形:
- 加工中に材料が変形しないよう、適切な支持方法や、加工順序を工夫することが求められます。特に薄い部品や長尺部品では、切削中に変形しやすいので注意が必要です。
- 加工後のストレス解放:
- 加工後に材料に内応力が残っている場合、後処理として焼きなましを行うことが有効です。これにより、内部応力が解消され、より安定した仕上がりが得られます。
1-3. 切削加工での仕上がりを美しくするためのテクニック
- 精密仕上げ:
- 真鍮や黄銅を加工する際は、最終的な仕上げで微細なバリや傷を取り除くことが大切です。仕上げの段階では、細かい切削工具や研磨剤を使い、表面の滑らかさを高めます。
- 微細な切削:
- 加工時に微細な切削を行うことで、表面の美しさを保ちながら高精度な仕上がりが可能です。特に精密部品や装飾品などでは、このテクニックが重要です。
- 高精度の測定機器使用:
- 仕上げ前に高精度な測定機器を使用して寸法を確認し、必要に応じて微調整を行います。これにより、仕上がり精度を一層高めることができます。
1-4. 旋盤加工における材料選びのポイント
- 材料の硬度と強度:
- 真鍮、黄銅、砲金の各材料の硬度や強度を理解し、加工条件に最適な材料を選びます。硬度が高い材料では、工具の摩耗が進みやすいため、耐摩耗性のある工具を使用します。
- 加工目的に合った材料:
- 加工の目的に応じて、強度や耐食性が求められる場面では黄銅や砲金が適しています。デザインや機能性が重視される場合は、真鍮が適していることが多いです。
- コストと効率:
- 加工する部品の要求精度や強度に対して、適切な材料を選ぶことでコストを抑えることができます。高精度な部品には高品質な材料を使用し、標準的な部品にはコストパフォーマンスの良い材料を選ぶと良いです。
1-5. 加工中のトラブルを防ぐための対策
一度に大きな切削を行うと、材料にストレスがかかり、加工精度が下がります。段階的に切削量を調整することで、安定した加工が可能になります。
振動の抑制:
加工中の振動は精度を大きく低下させる原因となります。これを防ぐためには、切削速度や送り速度の適正化、固定具や治具の強化が有効です。
過剰な熱の発生を防ぐ:
高温が発生すると、材料が膨張して精度が落ちます。冷却液を適切に使い、必要に応じて冷却システムの強化や調整を行います。
工具の摩耗管理:
工具の摩耗が進むと、加工精度が低下します。定期的に工具の状態をチェックし、摩耗した場合は早めに交換することで、トラブルを未然に防ぎます。
段階的な加工:
一度に大きな切削を行うと、材料にストレスがかかり、加工精度が下がります。段階的に切削量を調整することで、安定した加工が可能になります。
まとめ
旋盤加工において真鍮、黄銅、砲金の精度を高めるためのテクニックを解説します。適切な工具選定や切削条件の設定、冷却材の使用、加工順序の工夫が重要です。これらを駆使することで、精密な仕上がりが実現し、製品の品質向上に寄与します。