【旋盤加工のプロが教える!真鍮・黄銅・砲金の仕上げ精度を高める方法】
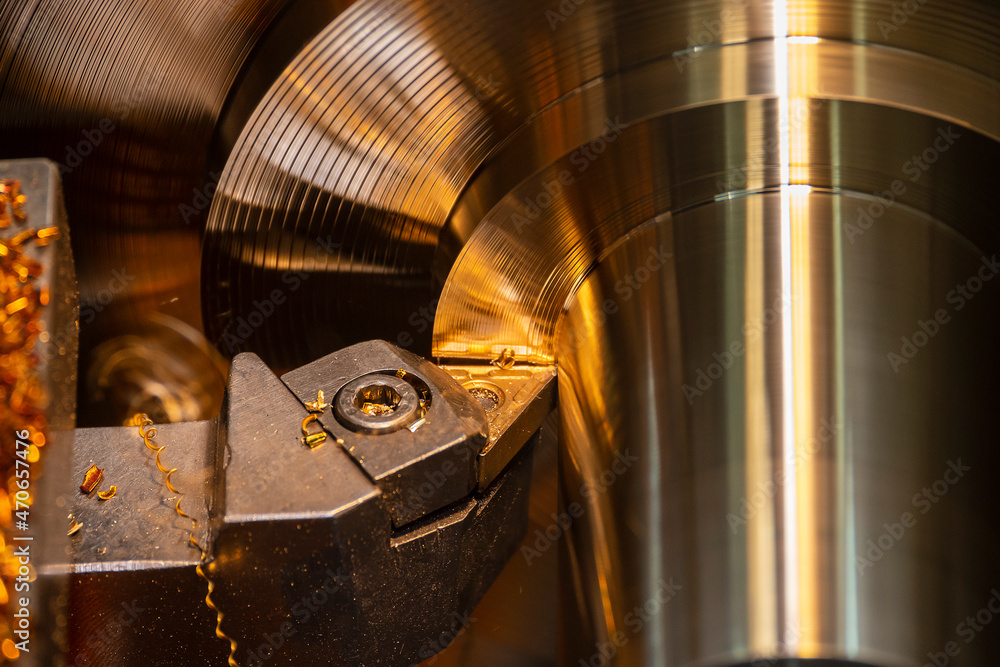
あなたは「旋盤加工をしているけれど、仕上げ精度をもっと高めたい…」と悩んでいませんか?それなら、この記事はまさにあなたのためにあります。旋盤加工のプロが、真鍮、黄銅、砲金の仕上げ精度を向上させるための具体的な方法をお伝えします。
このガイドでは、以下のような疑問を解決していきます。
- 旋盤加工における仕上げ精度とは何か?
- 真鍮や黄銅、砲金の特性と、それに適した加工方法は?
- 精度を高めるためのポイントやテクニックは?
旋盤加工は、工作物を高精度で仕上げるための重要な技術ですが、素材によって求められる技術やアプローチが異なります。本記事を通じて、旋盤加工の基礎から応用までを学び、あなたの技術を一段と向上させる手助けができれば幸いです。それでは、真鍮や黄銅、砲金の加工の世界へ、一緒に踏み出していきましょう!
1. 旋盤での仕上げ精度向上方法:真鍮、黄銅、砲金の基本
旋盤加工における仕上げ精度は、製品の品質に大きく影響します。真鍮、黄銅、砲金はそれぞれ特性が異なるため、仕上げ精度向上のためのアプローチも異なります。
1-1. 旋盤加工の基礎知識
旋盤加工は、回転する材料を切削工具で削りながら加工する方法で、円形の部品を精密に仕上げるために使用されます。加工精度を高めるためには、適切な切削条件や工具の選定が重要です。
1-2. 仕上げ精度とは何か
仕上げ精度は、加工後の部品の寸法や表面の状態を指し、これが高いほど、部品の品質が高いと評価されます。高精度な仕上げを実現するためには、加工中の振動や温度変化を抑え、安定した条件で加工を行う必要があります。
2. 旋盤での仕上げ精度向上方法:真鍮、黄銅、砲金の具体的手法
真鍮、黄銅、砲金における仕上げ精度を向上させるためには、切削条件や工具の選定が非常に重要です。以下に、精度向上のための具体的な手法を紹介します。
2-1. 切削条件の最適化
- 切削速度の調整:
切削速度が速すぎると、工具の摩耗や材料の熱膨張を引き起こし、精度に影響を与える可能性があります。反対に遅すぎると、加工効率が悪くなるため、最適な切削速度を設定することが重要です。 - 切削深さの設定:
適切な切削深さを設定することで、表面の仕上がりが向上します。深すぎる切削は精度を低下させるため、段階的に加工を行うことが推奨されます。
2-2. 適切な工具の選定
- 工具材質:
真鍮、黄銅、砲金などの材料に対して、工具の材質や形状を選ぶことが重要です。硬度が高い工具を使用することで、摩耗を防ぎ、長期間安定した切削が可能になります。 - 工具の鋭利さ:
鋭利な工具を使用することで、より精度の高い仕上げが可能となります。特に仕上げ加工では、工具の先端角度や形状にも注意を払うことが求められます。
2-3. 加工速度と送り速度の調整
- 送り速度の調整:
送り速度が速すぎると、仕上げ精度が悪化し、表面が粗くなります。適切な送り速度で加工することで、滑らかな表面を得ることができます。 - 加工速度と精度のバランス:
高速加工を目指す場合でも、精度を犠牲にしないように調整が必要です。特に精密部品の場合は、適切なバランスを見つけることが大切です。
3. 黄銅や真鍮の加工時の注意点
真鍮や黄銅は、銅をベースとした合金であり、材料特性に基づいた加工が求められます。以下のポイントに注意しながら加工を進めることが重要です。
3-1. 材料特性の理解
- 真鍮や黄銅の特性:
真鍮は加工しやすく、表面が美しいため、装飾部品や精密機器部品に利用されますが、強度が銅に比べてやや低いという特徴があります。これに対して黄銅は、真鍮よりも耐食性や強度に優れています。 - 加工時の温度管理:
高温下では真鍮や黄銅が変形しやすいため、加工時の温度管理をしっかり行う必要があります。特に切削中に発生する熱を適切にコントロールすることが精度向上に寄与します。
3-2. 加工中の熱管理
- 冷却液の使用:
切削時の熱を管理するためには、冷却液の使用が効果的です。適切な冷却液を使用することで、工具の摩耗を抑え、仕上げ精度を高めることができます。 - 熱膨張への対策:
真鍮や黄銅は熱膨張が大きいため、加工前に冷却を行い、熱膨張の影響を最小限に抑える工夫が求められます。
3-3. 切削液の選び方
選定のポイント:
高い冷却性能を持ち、腐食を防ぐ成分が含まれている切削液を選ぶことで、加工精度の向上が期待できます。特に、真鍮や黄銅には、無腐食タイプの切削液が推奨されます。
切削液の役割:
切削液は、摩擦を減らし、工具の冷却と切削面の潤滑を行います。特に真鍮や黄銅では、適切な切削液を選定することが重要です。
4. NC旋盤での特定の加工に関する具体的な質問解決
NC旋盤(数値制御旋盤)は、精密な加工が可能な機械で、様々な金属の部品加工に利用されています。特定の加工に関する問題を解決するために、以下の重要なポイントを押さえておきましょう。
4-1. NC旋盤の基本操作
NC旋盤は、コンピュータプログラムによって制御される旋盤です。プログラムに従って工具の位置や動きを正確に制御し、部品の加工を行います。基本操作には、以下のようなステップがあります:
- プログラムの入力:加工する部品の図面に基づいて、必要な加工情報(切削深さ、送り速度、回転速度など)をプログラムに入力します。
- 機械のセットアップ:材料を機械に固定し、工具を適切にセットします。
- 加工の開始:プログラムに従って自動で加工が行われます。
4-2. よくあるトラブルとその対策
NC旋盤でよく見られるトラブルとその対策には以下のようなものがあります:
- 振動:加工中に振動が発生すると、精度が低下することがあります。振動を抑えるためには、切削条件を調整するか、機械の安定性を確認します。
- 工具の摩耗:長時間の使用で工具が摩耗し、精度が落ちることがあります。定期的に工具を交換したり、適切な切削液を使用することが効果的です。
- 寸法誤差:加工後の部品が図面通りでない場合、プログラムの設定ミスや機械の調整不良が原因です。定期的な校正や、プログラムの再確認が必要です。
4-3. 加工プログラムの作成方法
NC旋盤の加工プログラムは、CAD/CAMソフトを使用して作成することが一般的です。以下の流れでプログラムを作成します:
- 部品の図面を作成:加工する部品の寸法や形状を詳細に記載します。
- 加工順序の決定:各工程(粗加工、仕上げ加工など)を順番に設定します。
- CAMソフトでのプログラム作成:図面を基に、切削速度、送り速度、工具の選定などを設定し、NC旋盤用のプログラムを作成します。
- プログラムの検証:仮想加工でプログラムの動作を確認し、エラーがないことを確認します。
5. 黄銅と真鍮の違いや特性を理解して使い分ける
黄銅と真鍮は、どちらも銅を基盤とした合金ですが、性質が異なり、用途にも違いがあります。それぞれの特性を理解し、適切な材料を選択することが重要です。
5-1. 黄銅の特性と用途
- 特性:黄銅は、銅に亜鉛を主成分とする合金で、優れた耐食性や強度を持っています。加工が容易で、比較的低コストで製造可能です。
- 用途:黄銅は、装飾品や機械部品、コインなどの用途に広く使用されています。耐食性が求められる場面で特に役立ちます。
5-2. 真鍮の特性と用途
- 特性:真鍮は、銅に亜鉛を加えた合金で、金色の外観が特徴です。真鍮は黄銅よりも柔らかく、熱や電気の導通性が優れています。
- 用途:真鍮は、音響機器や精密機械部品、電気接続部分など、特に導電性や美観が重要な部分に利用されます。
5-3. 適切な材料選定のポイント
- 強度が求められる場合:黄銅を選ぶと良いでしょう。黄銅は強度が高く、耐摩耗性にも優れています。
- 導電性や美観が求められる場合:真鍮を選ぶと、より適しています。特に美しい金色が重要な場合や、導電性が必要な場合に最適です。
6. 銅合金の加工方法やポイントを学ぶ
銅合金は、様々な種類があり、それぞれ異なる特性を持っています。銅合金を加工する際には、特性に応じた方法を選択することが重要です。
6-1. 銅合金の種類と特性
- C3604(黄銅):加工性が非常に高く、主に精密機器部品や配管に使用されます。耐腐食性も高いです。
- C3771(砲金):耐摩耗性や耐食性が非常に高いですが、加工はやや難しいため、特別な技術が求められます。
6-2. 加工時の注意点
- 熱管理:銅合金は熱膨張が大きいので、加工時に適切な冷却が必要です。
- 工具の摩耗:銅合金は比較的柔らかいため、工具が摩耗しやすいです。切削条件を調整して、工具寿命を延ばすことが重要です。
6-3. 仕上げ精度向上のためのヒント
工具の選定:銅合金に適した工具を使用することで、より精密な仕上げが可能になります。特に硬度が高い工具を選択すると、長寿命化が期待できます。
切削条件の最適化:切削速度や送り速度を適切に設定することで、仕上がりが向上します。特に仕上げ加工では細かな設定が求められます。
まとめ
旋盤加工において、真鍮・黄銅・砲金の仕上げ精度を高めるためには、適切な工具選定と切削条件の設定が重要です。冷却材の使用や加工速度の調整、仕上げ段階での微細加工を行うことで、表面品質を向上させることができます。また、定期的な工具のメンテナンスも精度維持に寄与します。