「真鍮加工のための最適な切削条件とは?」
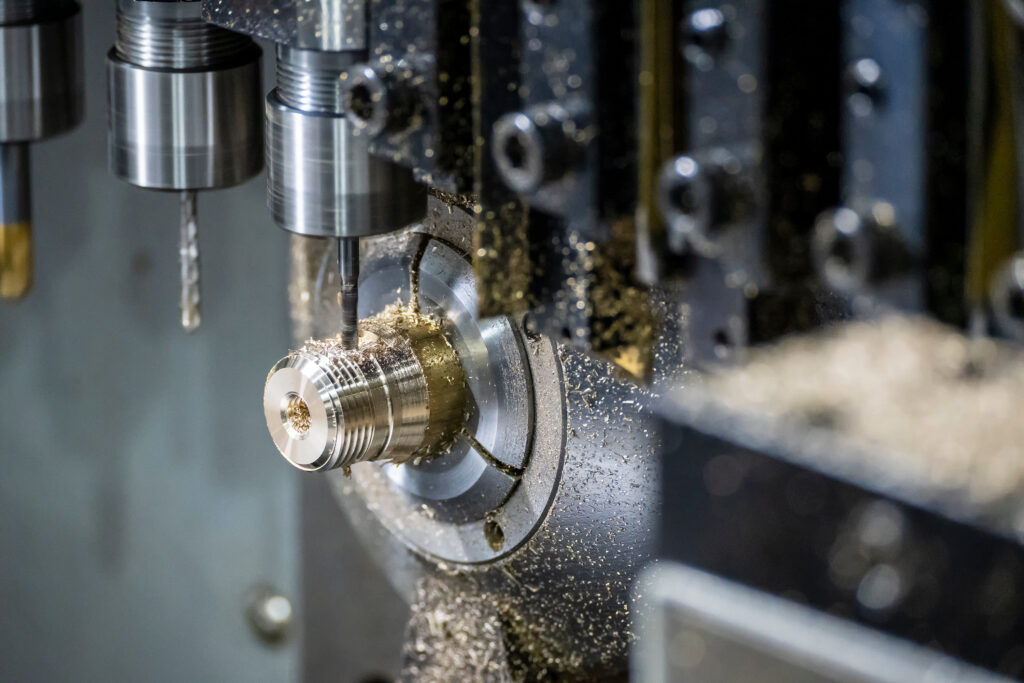
真鍮加工において、最適な切削条件をご存知ですか?真鍮の特性や切削条件の適切な設定は、加工作業の成功に大きく影響を与えます。本記事では、真鍮加工における重要な切削条件に焦点を当て、その正しい設定方法を詳しく解説します。真鍮の特性や材料の選定から始まり、最適な切削速度、送り速度、切削深さなどの要素まで、初心者から上級者まで幅広く役立つ情報を提供いたします。真鍮を効率的かつ正確に加工するためのヒントやコツも紹介しますので、ぜひご一読ください。
真鍮加工の基礎知識
真鍮とは:特性と用途
真鍮はその加工性の良さから多くの工業製品に利用されており、最適な切削条件を知ることは非常に重要です。主に、真鍮の切削では、切削速度、送り速度、切削深さが加工の仕上がりに大きく影響を与えます。例えば、一般的な真鍮加工では切削速度を100〜300m/min程度に設定し、送り速度は材料や工具に応じて調節するのが良いとされています。また、切削油の使用は摩擦熱を抑制し、工具の摩耗を減らすので推奨されます。具体的には、旋盤加工においては、柔らかい真鍮材料であれば高速度での加工が可能で、細かい仕上がりが求められる場合には丁寧な調整が必要です。結論として、真鍮加工における最適な切削条件は、材質や加工する製品の形状、要求される精度などに応じて慎重に選ばれるべきであり、それによって品質の高い製品を効率よく生産することが可能になります。
切削加工とその重要性
真鍮加工における最適な切削条件を定めることは非常に重要です。なぜなら、適切な切削条件によって、加工品の品質が保たれ、工具の寿命が延び、生産性が向上するからです。具体的には、真鍮を加工する際には、切削速度、送り速度、切り込み量という3つの要素が重要となります。例えば、切削速度が速すぎると工具の摩耗が早まり、遅すぎると加工時間が余分にかかります。適切な切削速度の選定は、材料の種類や工具の材質、加工する形状に応じて変わってきます。また送り速度と切り込み量も材料や工具、機械の能力に適応させる必要があります。したがって、真鍮加工で求められる最適な切削条件を見つけるには、これらの要素を総合的に考慮し、試験加工を繰り返しながら調整していくことが不可欠です。それにより、コスト削減と品質向上を同時に実現することができます。最終的には、適切な切削条件の下での加工が、真鍮製品の品質保持と生産効率の向上につながるのです。
真鍮の切削加工における注意点
真鍮の物理的特性への理解
真鍮加工における最適な切削条件は、製品の品質と加工効率に大きく影響を及ぼします。真鍮は熱伝導率が高く、軟らかい特性を持つため、加工時に発生する熱を効率よく逃がしやすい金属です。しかし、それゆえに切削速度や送り速度、工具の選択が重要になります。
具体的には、高速度での切削は熱の発生を抑え、真鍮の軟らかさによる切削工具への負担を低減します。また、適切な潤滑を行うことで、工具の摩耗を防ぎ、より高い精度での加工が可能になります。例えば、複雑な形状の部品加工には、熱影響を最小限に抑えるためにも、適した切削油の選定が必要です。
さらに、切削工具の材質にも注意を払う必要があります。真鍮向けに特化した工具は、より長い耐久性と安定した加工を提供するでしょう。このように、真鍮加工には適正な切削速度、送り速度、潤滑、工具選択が欠かせません。
結論として、真鍮加工の効率と品質を保つためには、加工条件の適切な設定が不可欠です。具体的な条件は加工する真鍮の種類や形状によって異なるため、経験と知識をもって、状況に応じた最適な条件を見極めることが求められます。
真鍮加工時の一般的な問題点
真鍮加工に最適な切削条件は、製品の品質や加工効率に大きな影響を与えます。真鍮はその良好な加工性から、多様な工業製品の材料として広く利用されていますが、適切な切削条件を見極めることが重要です。一般的に、真鍮を切削するには、切削速度を速めに設定するのが効果的です。これにより、切削工具の寿命を延ばしつつ、滑らかな表面仕上げが可能になります。具体的な例として、小径のエンドミルを使用する細かな加工では、高速回転による正確な加工が求められることがあります。また、潤滑剤の適切な使用は、摩擦を減らし、工具の摩耗を抑制し、加工品の品質向上に寄与します。最終的に、真鍮加工において適切な切削条件を選択することは、材料の特性を最大限に活かし、効率的かつ高品質な製品を生産するための鍵です。
工具の選択と管理
真鍮加工における最適な切削条件としては、工具の選択と管理が欠かせません。真鍮は、金属の中でも比較的柔らかく加工しやすい特性を持っていますが、その性質を生かした切削作業を行うには適切な切削速度や送り速度の設定が重要です。例えば、切削速度が速過ぎると工具の摩耗が早まり、遅すぎると加工効率が落ちるため、材質や形状に応じた最適な速度を見極める必要があります。また、刀具の刃の状態を常にチェックし、研磨や交換を適時行うことで、常に安定した加工を実現できます。定期的なメンテナンスと正確な切削条件の設定が、品質向上と効率的な生産の鍵を握っています。
真鍮の切削条件の基本
切削速度の決定
真鍮加工に最適な切削条件を見極めることは、効率的な製造プロセスと品質の高い製品を得るために不可欠です。真鍮はその加工性の良さから、様々な産業で利用されていますが、最適な切削条件には切削速度、送り速度、工具の種類などが影響を与えます。例えば、高い切削速度は生産効率を向上させる可能性がありますが、過度に高い速度は工具の摩耗や製品の精度低下を招くことがあります。実際の加工現場では、真鍮の硬さや熱伝導性を考慮し、経験則や試作を重ねて条件を調整することが一般的です。さらに、専用の冷却液を使用して工具と材料の温度上昇を抑えることも重要です。これにより、工具の寿命を延ばしつつ、製品の寸法精度を保つことが可能になります。したがって、真鍮加工における切削条件の最適化は、試行錯誤と経験を基に、生産性と品質のバランスを見極めることが求められる作業であると言えます。
送り速度とその影響
真鍮加工における最適な切削条件を理解することは、製品の品質向上と製造効率の確保に不可欠です。真鍮はその加工容易性から、多くの部品製造に利用されていますが、適切な切削条件を見極めることが重要です。例えば、送り速度が適切でない場合、仕上がりの粗さが悪化したり、工具の摩耗を早める原因となります。具体的には、真鍮の種類や硬さ、加工する製品の形状に応じて、切削速度や送り速度、切り込みの深さを最適化することが求められます。特に、小さなバリが発生しやすい真鍮加工では、精密な送り速度のコントロールが仕上がりの品質を大きく左右します。最終的に、試作や経験によって得られる知見をもとに、切削条件を細かく調整することで、効率的かつ高品質な真鍮加工が実現可能となります。
切削液の役割と選択
真鍮加工において最適な切削条件を見極めることは、製品の品質や加工効率を左右します。真鍮は切削加工がしやすい素材でありながらも、適切な切削条件を設定することでさらに仕上がりを良くすることが可能です。例えば、切削速度、送り速度、そして切削液の使用は、真鍮の加工品質に大きく影響します。特に切削液は、加工中の摩擦熱を軽減し、工具の摩耗を防ぎ、表面精度を高めるために不可欠です。具体的な例を挙げると、真鍮を加工する際には水溶性の切削液を用いると良い結果が得られます。これは水溶性のものが良い冷却効果と潤滑性を提供し、真鍮の性質に合っているためです。結果として、切削条件の最適化は、高品質な真鍮製品の生産に欠かせない要素となります。
最適な切削条件の設定
真鍮加工に適した工具材質
真鍮加工における最適な切削条件を探ることは、高品質な製品を効率的に製造する上で非常に重要です。一般に、真鍮は柔らかく加工しやすい金属の一つとされていますが、適切な切削条件が重要です。最適な条件とは、工具の材質や刃の角度、さらには送り速度や切削速度など、多岐にわたります。
特に、高速度鋼や超硬合金が工具材質として適しており、これらは真鍮の切削に良好な結果をもたらします。また、シャープなエッジを維持するための適切な刃の角度の設定が、切削精度を高めるためには不可欠です。さらに、加工時の送り速度や切削速度を適切に調整することで、工具の摩耗を防ぎつつ、滑らかな表面仕上げを実現できます。
たとえば、小径のエンドミルを使用する際には、高い切削速度が推奨されることがありますが、これは真鍮の独特な特性と相まって、切削効率を高めるためです。切削液の使用も、工具の寿命を延ばし、切削面の品質を向上させるために重要です。
結論として、最適な切削条件は真鍮の種類や加工する形状によって変わるため、具体的な作業に応じた慎重な設定が求められます。品質と効率を両立する真鍮加工には、これらの検討が不可分なのです。
理想的な切削速度と送り速度の組み合わせ
真鍮加工の適切な切削条件を見つけることは、製品の品質を左右するだけでなく、工具の寿命を延ばし、効率的な生産にも繋がります。理想的な切削速度と送り速度の組み合わせは、素材の特性と加工機の能力に密接に関わっています。例えば、真鍮は比較的柔らかい材質であるため、高すぎる切削速度は材料の発熱を引き起こし、切りくずの除去が困難になります。逆に、遅すぎる速度は切削効率を低下させ、工具の摩耗を早める原因となります。送り速度に関しても、適切な値を見つけることは重要で、材料の変形を防ぎつつ、スムーズな切削を実現する必要があります。したがって、真鍮加工においては、一般的に中程度の切削速度と均一な送り速度を保つことが推奨されます。これにより、高品質な加工面を得ることができ、作業の効率も向上します。最終的に、理想的な切削条件を実現することは、優れた製品を安定して生産するために不可欠です。
切削液の使用法とその効果
真鍮加工における切削条件の最適化は、製品の品質向上と工具の寿命延長に不可欠です。まず、真鍮は他の金属と比べて軟らかく、切削が容易な特性を持っているため、高い切削速度が可能です。しかし、適切な切削速度は材料の熱伝導率や硬度、さらには切削工具の材質に左右されるため、これらを考慮して決める必要があります。
具体的には、小さい切削深さと小さい送り速度を用いることで、工具への負担を軽減し、加工面の仕上がりを良くすることができます。また、高品質な切削油の使用は、摩擦を減少させ、切削温度の上昇を抑えることにより、加工精度を高める効果があります。
したがって、真鍮加工に最適な切削条件とは、素材の特性を考慮した切削速度、工具に負担をかけない切削深さと送り速度の選定、そして高品質な切削油の使用による総合的な管理が求められるのです。これらを適切に組み合わせることで、真鍮加工の効率と品質を同時に向上させることが可能です。
切削条件の調整と最適化
経験則と切削条件の選定
真鍮加工において最適な切削条件を見極めることが、加工効率の向上と製品品質の維持に不可欠である。一般的に、真鍮の切削には、高速度鋼や超硬合金などのツールが使用されるが、切削速度、送り速度、切り込み深さが重要なパラメータとなる。例えば、切削速度が速すぎるとツールの摩耗が激しくなり、遅すぎると加工時間が長くなり非効率的である。また、送り速度が高い場合は表面仕上げが荒くなり、低い場合は切削性が損なわれる。実際の加工現場では、これらの条件を工具の種類や真鍮の特性に応じて見極める知識と経験が求められる。したがって、切削条件は経験則に基づく調整が欠かせない。なお、切削条件の最適化により、加工速度を高めつつもツール寿命を延ばし、結果としてコスト削減にも寄与することができる。
トライアルエラーによる条件の微調整
真鍮加工において最も重要なのは切削条件を最適化することで、これにより加工の品質を高めると共に工具の耐久性も向上させることが可能です。切削速度、送り速度、切削液の使用などが、その条件として挙げられますが、これらは材質の特性や加工する形状によって微妙に異なります。例えば、一般的な真鍮材では、切削速度を速めにすることで滑らかな表面が得られますが、加工時の熱が原因で工具の摩耗が早まることがあります。したがって、実際の工場では、繰り返しトライアルを行いつつ、加工品の仕様や使用する工具の材質に合わせて、細かい条件の調整を重ねていきます。最適な切削条件の探求は、まさに経験と知識が結晶する技術であり、その技術によって、高品質な真鍮加工品を安定して生産することが可能になります。
長期的な加工精度の維持方法
長期的に真鍮加工の精度を保つためには、最適な切削条件の選定が不可欠です。真鍮は軟らかく加工しやすい金属ですが、間違った切削条件では品質が落ちるだけでなく、工具の摩耗も早まります。そのため、切削スピード、送り速度、切り込み深さなどの条件を適切に設定することが重要です。
たとえば、スピンドルの回転数を高くしすぎると、過剰な熱が発生し、真鍮の表面が焼け付いてしまう可能性があります。それを防ぐためには、材質に見合った範囲で回転数を選ぶことが肝心です。また、送り速度は切削効率に直結しますが、早すぎると切断面が荒くなる場合があるため、丁寧な作業を心掛ける必要があります。
実際に、日本の加工業界では、真鍮の切削には特殊なコーティングが施された工具が推奨されることが多く、これにより工具寿命の延長と精度の高い加工が可能になります。最終的には、適切な切削油の使用も品質維持に不可欠であり、これらの切削条件を総合的に管理することで、長期的な加工精度が保たれるのです。
実践的な切削加工事例
成功事例の分析
真鍮加工における最適な切削条件を見極めることは、製品の品質向上とコスト削減に直結します。具体的には、切削速度、送り速度、切削深さといった要素が重要となります。真鍮は比較的柔らかい材料であるため、高い切削速度で加工が可能ですが、適切ではない条件での加工は工具の摩耗を早めたり、仕上がり面にしわや欠けを生じさせる原因となります。例えば、一般的には切削速度を100〜300m/min程度に設定し、送り速度は材料の硬度に応じて調整します。また、切削オイルの使用は、摩擦熱を減少させ、切りくずの排出をスムーズにすることで品質の安定に寄与します。成功事例を分析すると、これらの条件を総合的に考慮した上で、定期的な工具のメンテナンスを行うことが、長期にわたる安定した真鍮加工のための鍵となることがわかります。したがって、真鍮加工において最適な切削条件の把握は、効率的かつ高品質な生産活動に不可欠です。
一般的な失敗事例とその対策
真鍮加工における最適な切削条件を見極めることは、加工効率と製品品質を高める上で非常に重要です。真鍮はその加工性の良さから、幅広い産業で利用されていますが、切削条件が適切でない場合、工具の摩耗が激しくなったり、仕上がりの精度に影響を及ぼすことがあります。特に、カッターの速度、送り速度、切り込み量は最適なバランスが求められます。例として、高速での加工は生産効率を向上させますが、過度な速度は切削熱の増大により工具の寿命を短くしたり、材料の変色やひずみを引き起こす恐れがあります。適切な切削油の使用も、真鍮の切削性を向上させる一因となります。高品質な真鍮加工を実現するためには、これらの条件を事前に細かく調整し、定期的な工具のメンテナンスと共に、材料の特性に適した切削条件の選定が不可欠です。したがって、経験とデータに基づいた条件設定が、効率的かつ高品質な真鍮加工を実現する鍵と言えるでしょう。
切削加工の効率化テクニック
真鍮加工における最適な切削条件を知ることは、製品の品質向上と生産性の向上に不可欠です。切削条件の基本は、切削速度、送り速度、および切削深さといった要素に注目し、これらを適切に設定することにあります。例えば、真鍮は軟らかい材料であるため、高い切削速度を適用できますが、切削速度が高すぎると工具の摩耗が激しくなり、コストが増加します。一方で、送り速度が低すぎると加工時間が長くなり、生産効率が下がることになります。具体的には、高速度鋼や超硬質材料の切削工具を使用し、適切な潤滑剤を選ぶことで、切削抵抗を減少させ、加工精度を高めることができます。結論として、真鍮の切削加工では、材料の特性を考慮した上でバランスの取れた切削条件を選定することが、効率的な製造プロセスを実現する鍵となります。
真鍮加工のための切削条件のまとめとポイント
切削条件設定のチェックリスト
真鍮加工における切削条件は、最終的な製品品質に大きく影響します。適切な切削条件の設定は、工具の耐久性を高め、加工精度を向上させる上で欠かせません。具体的には、切削速度、送り速度、切り込み量などが挙げられます。例えば、真鍮は柔らかい材料なので、高い切削速度で加工することが可能ですが、速度が高すぎると工具や材料が熱を持ちすぎ、寿命を短くしたり品質を損なう恐れがあります。一方、送り速度が遅すぎると生産効率が落ち、経済性に問題が生じます。適切な条件は工具や加工機械、加工する真鍮の種類によっても変わるため、事前に試験加工を行い条件を見極めることが重要です。このように、真鍮の切削には最適化された条件設定が必要であり、それによって製品の品質を保ちながら効率的な生産が可能となります。
持続可能な加工環境の構築
真鍮加工における最適な切削条件は、品質向上とコスト削減の両立に不可欠です。まず、真鍮はその優れた加工性により、さまざまな業界で利用されていますが、適切な切削条件を見極めることが重要となります。ここでいう「切削条件」とは、切削速度、送り速度、切削液の使用などを指します。具体的には、真鍮の種類に応じた適正な切削速度の選定が必須であり、高すぎると工具の摩耗が早まり、低すぎると加工効率が落ちます。さらに、連続して切削を行う際には、適切な送り速度と切削液の利用が、工具の寿命延長と仕上がりの向上に寄与します。例えば、精密部品を加工する際には、精度を保つために冷却機能が優れた切削液の選択が肝心です。このように、真鍮加工の最適な切削条件を見極めることは、製品の品質保持とコスト削減に直結し、持続可能な加工環境の構築に貢献します。
継続的な学習と技術の更新
真鍮加工における最適な切削条件を見極めることは、高品質な製品を効率的に生産するために不可欠です。まず、真鍮はその良好な機械的性質から、装飾品や精密部品など様々な用途に利用されており、切削加工においてもその優れた特性を活かすことが可能です。しかし、適切な切削条件を選定しなければ、工具の摩耗や製品の精度に悪影響を及ぼすことになります。
具体的な最適条件としては、適切な工具材質の選択、切削速度、送り速度、切り込み深さの調整が重要となります。たとえば、真鍮には硬質のチップを使用し、適切な潤滑を行いながら、比較的高めの切削速度で加工することが推奨されています。これにより、加工面の品質を保ちつつ、工具の摩耗を低減させることができるのです。例として、真鍮の旋削加工においては、速度100〜300m/min、送り0.01〜0.2mm/rev、切り込み深さ0.5〜3mmが一般的な目安です。
結論として、真鍮加工における最適な切削条件を見極めることで、加工効率と製品品質の向上が可能となります。このためには、材質や加工内容に応じた適切な設定が求められるため、経験とともに最新の加工技術を常にアップデートしていくことが重要です。
まとめ
真鍮の加工において最適な切削条件を見つけることは重要です。切削速度や切り込み深さ、送り速度などを適切に設定することで、真鍮加工の効率と精度を向上させることができます。また、適切な刃物や冷却方法も重要な要素です。これらの要素を熟考し、最適な切削条件を見つけることが真鍮加工の成功につながります。