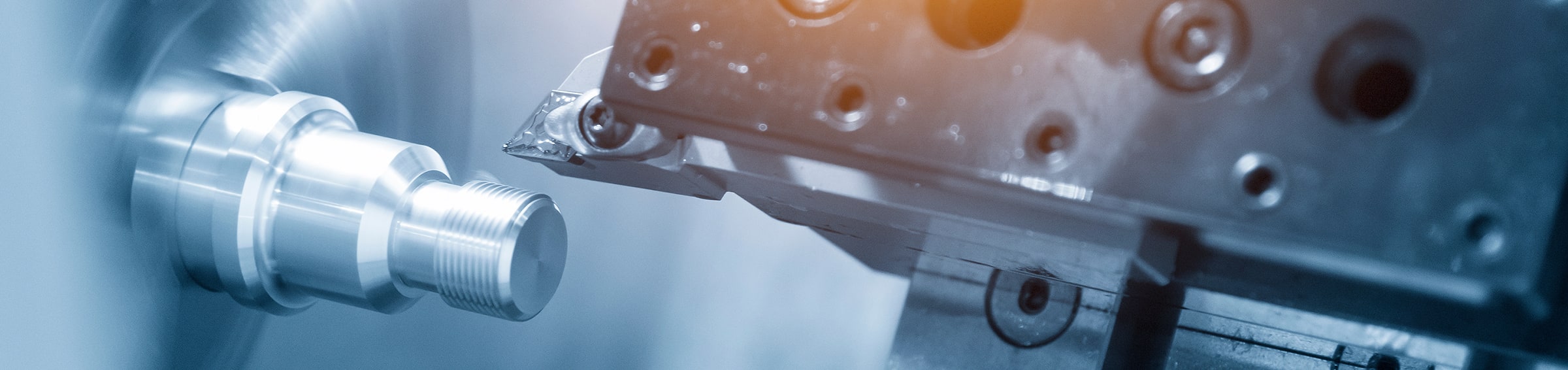
加工技術 column
C2800黄銅の特性とは?旋盤加工における利点と注意点
旋盤加工において、素材の特性を理解することは極めて重要です。特にC2800黄銅は、その特性と加工性から多くの業界で利用されています。「C2800黄銅について詳しく知りたい」「旋盤加工の際のコツや注意点は何か?」といった疑問を抱えている方に向けて、このガイドをお届けします。
C2800黄銅は、銅と亜鉛の合金で、優れた加工性と耐腐食性を兼ね備えています。これにより、旋盤加工においても高い精度での加工が可能。また、その美しい金色の外観は、装飾的な用途にも最適です。しかし、扱う際にはいくつかの注意点も存在します。
本記事では、C2800黄銅の特性を詳しく解説し、旋盤加工における利点や効率的な加工方法、そして注意点についてもお伝えします。これから旋盤加工を行う方々や、C2800黄銅に興味のある方々にとって、役立つ情報が満載です。ぜひ最後までお読みいただき、実践に役立ててください。
1. C2800 黄銅の特性と旋盤加工時のコツ
C2800 黄銅は、銅と亜鉛の合金で、加工性や耐食性に優れた素材です。以下に、C2800黄銅の特性や旋盤加工時のコツについて説明します。
1-1. C2800 黄銅の材質特性
- 成分: C2800は、主に銅と亜鉛を基にした合金で、亜鉛の含有量が約30%程度です。
- 加工性: 高い加工性を持ち、切削や機械加工が容易で、特に精密部品の製造に適しています。
- 耐食性: 良好な耐食性を持ち、特に湿気や腐食性の環境でも優れた耐久性を発揮します。
- 強度と硬度: 強度と硬度がバランスよく、特に日常的な使用においては安定した性能を示します。
1-2. C2800 黄銅の規格と選び方
- 規格: C2800はJIS規格やASTM規格で提供され、使用する用途に応じて最適な規格を選ぶ必要があります。
- 選び方: 加工方法や用途に応じて、強度や加工性、耐食性のバランスを考慮して選定します。例えば、精密部品には加工性を重視し、耐久性が求められる部品には耐食性を重視することが一般的です。
1-3. C2800 黄銅の物理的性質と応用
- 物理的性質: C2800黄銅は、優れた熱伝導性や電気伝導性を持ち、これにより電気機器や熱機器に広く利用されます。
- 応用: 電子機器、装飾品、精密部品、建材など多岐にわたる用途に対応しており、特に精密加工や美観が求められる分野での使用が多いです。
2. C2720の特性と利用方法
C2720は銅合金の一種で、特定の用途で優れた性能を発揮します。
2-1. C2720の材質特性
- 成分: C2720は、銅と亜鉛を主成分とし、亜鉛含有量が20%程度の合金です。
- 特徴: 比較的高い耐食性を持ち、特に海洋環境や湿気の多い環境でも使用可能です。
- 加工性: C2720は加工が容易であり、切削加工や成形加工がスムーズに行えます。
2-2. C2720の加工方法と注意点
- 加工方法: C2720は旋盤やフライス盤による加工が可能で、精密な切削や仕上げが求められる部品に使用されます。
- 注意点: 加工時には適切な切削条件(回転速度や送り速度)の設定が重要です。過度な温度上昇や工具の摩耗を避けるため、切削液の使用が推奨されます。
3. 真鍮の切削加工技術
真鍮は銅合金の一種で、切削加工の際に特有の技術が求められます。以下に、真鍮の切削加工に関する基本技術とポイントを説明します。
3-1. 切削加工の基本技術
- 切削工具の選定: 真鍮加工には、鋭利な切削工具を使用することが重要です。特に高速度鋼や超硬工具が適しています。
- 切削条件の設定: 真鍮は加工が比較的容易な材料ですが、適切な切削速度や送り速度を設定しないと、仕上がりに影響を与える可能性があります。
- 切削液の使用: 切削液は、工具の冷却と摩耗防止に重要です。また、切削中の表面仕上げにも影響を与えるため、適切な選択が必要です。
3-2. 真鍮の切削加工におけるポイント
加工時のトラブル: 真鍮は比較的加工しやすい素材ですが、過度な熱生成や工具の摩耗に注意が必要です。切削条件を最適化し、トラブルを回避しましょう。
仕上げの重要性: 真鍮は表面仕上げが重要であり、特に精密部品や装飾品の場合、良好な仕上がりが求められます。加工後の研磨や仕上げ作業を適切に行うことで、仕上げ精度を高めることができます。
4. C2801の旋盤加工における真鍮素材の特性
C2801は、良好な加工性と優れた機械的性質を持つ真鍮の一種で、旋盤加工においても特に有効な材料です。以下にC2801の特性と加工時のコツについて説明します。
4-1. C2801の特性と加工技術
- 材質特性: C2801は、銅と亜鉛を主成分とした真鍮で、亜鉛含有量が約30%程度です。加工が容易で、切削性、延性、強度のバランスが良好です。
- 機械的性質: 強度や硬度のバランスが良く、耐食性に優れています。特に耐摩耗性と耐腐食性が求められる部品に適しています。
- 加工技術: 旋盤加工時には、適切な回転速度や切削条件を設定し、工具の摩耗を抑制しながら精密加工を行うことが重要です。さらに、切削液を使用することで熱の発生を抑え、表面仕上がりを良くすることができます。
4-2. C2801の旋盤加工のコツ
- 切削速度の最適化: C2801の旋盤加工では、適切な切削速度を設定することが重要です。過度な切削速度は、工具の摩耗を早め、仕上げ精度に影響を与える可能性があります。
- 工具の選定: 超硬工具やコーティングされた工具が適しています。これにより、長時間の加工にも耐えられるだけでなく、安定した仕上がりが得られます。
- 切削液の使用: 切削液は温度上昇を防ぎ、加工中の摩擦を減らすために使用します。また、仕上げ時には清浄な切削液を使用して、表面を滑らかに保つことができます。
5. 真鍮C2600の物理的性質と応用
C2600は、真鍮合金の中でも特に一般的に使用される材料で、機械的性質や耐食性に優れています。C2600の物理的性質や応用について解説します。
5-1. C2600の特性と利点
- 成分と特性: C2600は、主に銅と亜鉛から成る合金で、亜鉛含有量が30%程度です。この合金は、強度が高く、加工性に優れ、さらに耐食性も良好です。
- 耐食性: 特に湿気や酸性環境下での耐食性が良く、これにより多くの産業用途において広く使用されています。
- 加工性: 切削や加工が非常にしやすく、精密部品や機械部品、装飾品などさまざまな用途で使用されています。
5-2. C2600の応用事例
装飾品: 美しい金色の外観を持つため、ジュエリーや装飾品の材料としても広く使用されています。
電子機器: C2600は電気的特性も良好なため、電子機器の接点やコネクタ部品として使用されることがあります。
精密機器: 高い耐摩耗性と強度を持ち、精密機器の構造部品やギア、歯車などに利用されます。
まとめ
C2800黄銅は優れた耐腐食性と加工性を持ち、旋盤加工に適しています。強度と延性が高く、精密部品の製造に理想的です。しかし、熱処理による変形や、切削条件の設定に注意が必要です。適切な工具と冷却を使用することで、加工精度を向上させることができます。
黄銅の旋盤加工における最適条件とは?
「黄銅の旋盤加工を行いたいけれど、最適条件が分からない…」と悩んでいるあなたへ。加工精度や仕上がりにこだわる職人や技術者にとって、材料の特性を理解し、適切な条件を見つけることは非常に重要です。この「黄銅の旋盤加工における最適条件」のガイドでは、C3604黄銅の特徴を踏まえた理想的な加工方法やポイントを詳しく解説します。
この記事は、以下のような方に最適です。
- 黄銅の旋盤加工を始めたばかりの技術者
- より高精度な加工を目指す職人
- 黄銅の特性とその加工法を学びたい方
正しい加工条件を理解することで、作業の効率を高め、製品の品質を向上させることができます。最適な条件を見つけ、あなたの技術を更に磨きましょう。このガイドを通じて、黄銅の旋盤加工の世界がより身近なものになることを願っています。
1. C3604 黄銅の旋盤加工での最適条件とは
C3604黄銅はその優れた加工性と強度から、旋盤加工での使用に適した材料です。最適な条件を設定することで、高品質な仕上がりを実現することができます。
1-1. C3604材の特性
- 優れた加工性: C3604黄銅は、優れた切削性を持っており、複雑な形状でも容易に加工できます。
- 耐腐食性: ある程度の耐腐食性を持っており、様々な環境で使用可能です。
- 良好な強度と耐摩耗性: 高い強度と耐摩耗性を有しており、機械部品や装置に適しています。
1-2. 加工における重要な要素
- 切削速度: 適切な切削速度を選ぶことが、仕上がりの精度や工具寿命に直結します。C3604黄銅の加工時には適切な速度を設定し、熱の発生を抑えます。
- 切削液の使用: 切削液を適切に使用することで、工具の冷却や摩擦の低減が可能となり、加工精度が向上します。
- 工具の選定: 黄銅の加工には、鋭利な工具を選ぶことが重要です。鋭利な工具で切削することで、切削面が滑らかになり、工具の摩耗も抑えられます。
1-3. 最適条件の設定方法
- 切削速度の設定: C3604黄銅の適切な切削速度は、通常30~50 m/minの範囲で設定します。過度な切削速度を避け、安定した加工を心がけます。
- 送り速度の調整: 送り速度は、材料の硬さや加工内容に応じて調整し、精度の高い仕上がりを実現します。
- 切削深さの管理: 一度の切削で大きな深さを削るのではなく、少しずつ削っていくことで仕上がりをきれいに保ちます。
2. C3604 黄銅の旋盤加工における基礎知識
C3604黄銅を旋盤加工する際には、基本的な知識と適切な機材の選定が重要です。
2-1. 旋盤加工の基本概念
- 旋盤加工とは: 旋盤は、回転するワークに対して工具を送り込み、切削していく加工方法です。外径や内径、ねじ切りなど、さまざまな形状を加工することができます。
- 主な加工方法: C3604黄銅の旋盤加工では、外径切削、内径切削、面取り、ねじ切りなどが一般的です。特に精密な仕上げが求められる部品に使用されます。
2-2. 旋盤の種類と選び方
- 汎用旋盤: 標準的な旋盤で、多くの部品加工に適しています。C3604黄銅を使用する場合、汎用旋盤で十分に対応できます。
- CNC旋盤: より複雑な形状や高精度な加工が求められる場合は、CNC(コンピュータ数値制御)旋盤を使用することで、精度が高い加工が可能です。
2-3. 加工工具の選定
切削刃先形状: 切削の安定性を保つためには、適切な刃先形状を選定することが重要です。鋭利な刃先で加工することで、仕上がりが滑らかになります。
超硬工具: C3604黄銅のような黄銅合金を加工する場合、超硬工具を使用することが一般的です。耐摩耗性が高く、長寿命で精度の高い加工が可能です。
3. C3604 黄銅の旋盤加工での注意点
C3604黄銅を旋盤加工する際には、いくつかの注意点を考慮することが、品質を高めるために重要です。
3-1. 加工中のトラブルと対策
- トラブル1: 過剰な熱発生
- 原因: 切削速度が高すぎたり、切削液が不十分な場合に熱が過剰に発生することがあります。
- 対策: 適切な切削速度と送り速度を設定し、切削液を十分に使用して熱を抑えることで、過熱を防ぎます。
- トラブル2: 刃先の摩耗
- 原因: 長時間の使用や不適切な切削条件により、刃先が早く摩耗することがあります。
- 対策: 刃先の摩耗を定期的に確認し、必要に応じて交換します。切削条件を最適化することも重要です。
- トラブル3: 仕上げ面の粗さ
- 原因: 不適切な工具選定や切削条件によって、仕上がり面が粗くなることがあります。
- 対策: 精密な工具と安定した加工条件を使用することで、仕上がりの滑らかさを確保します。
3-2. 切削液の重要性
- 冷却作用: 切削液は、加工中に発生する熱を吸収し、工具やワークの温度を適正範囲に保ちます。適切な冷却がないと、過熱による仕上がり不良や工具寿命の低下が発生します。
- 潤滑作用: 切削液には潤滑作用もあり、工具とワークとの摩擦を減少させ、切削性能を向上させます。適切な切削液の使用により、摩耗を抑え、より精密な加工が可能になります。
- 腐食防止: 特に黄銅などの金属を加工する場合、切削液に含まれる化学成分が、ワークの表面に腐食を引き起こす可能性があるため、腐食防止の役割を果たすものを選定することが重要です。
3-3. 加工後の仕上げ処理
- バリ取り: 旋盤加工後にはバリが発生することがあるため、バリ取り作業が必要です。これにより、製品の精度や外観が向上します。
- 研磨: 仕上げ面をさらに滑らかにするためには、研磨を施すことが一般的です。これにより、製品の品質が向上し、外観も良好になります。
- 表面処理: 加工後に表面処理を行うことで、耐食性や耐摩耗性が向上します。特に黄銅のような材料には、メッキ処理や酸化処理を施すことが推奨されます。
4. C3604 黄銅の機械的性質
C3604黄銅は、その機械的性質において優れた特性を持っており、様々な用途に対応しています。
4-1. 真鍮の強度と硬度
- 強度: C3604黄銅は優れた引張強度を持ち、耐荷重性に優れています。これにより、機械部品や構造部品として利用されています。
- 硬度: 真鍮は比較的柔らかい金属であり、硬度が低いため加工が容易です。しかし、その柔軟性も特性の一部として重要です。
4-2. 耐食性と耐摩耗性
- 耐食性: C3604黄銅は、海水や湿度の高い環境でも耐食性を発揮します。これにより、腐食に対する耐性が求められる環境での利用に適しています。
- 耐摩耗性: 銅合金である黄銅は摩耗に強い性質を持っています。耐摩耗性が高いため、長期間にわたり安定した性能を発揮します。
4-3. 加工性の評価
工具寿命の延長: 黄銅の加工時は、適切な切削条件と切削液の使用により、工具寿命が延び、コスト削減と生産性向上が実現できます。
良好な加工性: C3604黄銅は、金属加工業界で非常に優れた加工性を誇り、精密加工が容易に行えます。切削性が良好で、複雑な形状にも対応可能です。
まとめ
黄銅の旋盤加工における最適条件は、切削速度、送り速度、工具の材質と形状に依存します。切削速度は一般的に30~60 m/minが推奨され、送り速度は0.1~0.3 mm/revが効果的です。工具には耐摩耗性の高い材料を選び、冷却液の使用も重要です。これにより、加工精度と表面品質が向上します。
砲金旋盤加工ガイド:特性と注意点を徹底解説
砲金旋盤加工に興味があるけれど、「どんな特性があって、加工時には何に気を付ければいいのか分からない…」という悩みを抱えていませんか?そんなあなたのために、今回は「砲金旋盤加工ガイド」をお届けします。
この記事では、砲金の特性や、その特性を活かした旋盤加工の注意点について詳しく解説します。砲金が持つ優れた耐食性や機械的特性、加工時に気を付けるべきポイントについて知識を深めることができるでしょう。初心者から経験者まで、幅広い層の方々に役立つ情報を提供しますので、ぜひ最後までお付き合いください。あなたの加工スキルを向上させ、より良い成果を得る一助となることを願っています。
1. 砲金の特性と旋盤加工時に注意すべき点
砲金は銅合金の一種で、優れた機械的特性や耐摩耗性を持ち、幅広い分野で使用されています。旋盤加工時における砲金の特性を理解し、適切な加工方法を選ぶことが重要です。
1-1. 砲金とは何か
- 砲金は、主に銅とスズを含む合金で、古くから鋳物や部品加工に使用されてきました。銅の強度とスズの耐摩耗性を活かした合金です。
- 砲金は、耐食性が高く、摩耗に強いため、機械部品やエンジン部品、船舶部品など、厳しい環境で使用されることが多いです。
1-2. 砲金の特性
- 耐摩耗性: 砲金は摩耗に強く、長期間使用される部品に適しています。
- 耐食性: 銅合金として非常に高い耐食性を持ち、海水や化学薬品などに耐えることができます。
- 加工性: 鋳造性が高く、切削加工にも適しています。特に旋盤加工で優れた結果を得やすいです。
- 強度と硬度: 強度と硬度は高く、機械部品として必要な性能を持っていますが、硬度が高すぎると切削性が悪化することもあります。
1-3. 砲金と他の金属の違い
- 砲金と黄銅: 砲金はスズを含む銅合金で、黄銅は主に亜鉛を含む銅合金です。砲金は耐摩耗性や耐食性が高い一方、黄銅は加工性や強度が特徴です。
- 砲金と鋼材: 鋼は強度が高く、硬度も優れていますが、砲金は加工性や耐食性で勝るため、用途に応じて使い分けられます。
1-4. 砲金の利点と欠点
- 利点:
- 高い耐摩耗性と耐食性
- 優れた鋳造性と加工性
- 長寿命で耐久性が高い
- 欠点:
- 強度が鋼には劣る
- 高価であることが多い
- 切削時に冷却が不十分だと工具摩耗が進行しやすい
2. 砲金の特性と旋盤加工の技術
砲金は旋盤加工に適していますが、特定の技術や条件が必要です。適切な加工技術を採用することで、高精度な部品を効率良く製造できます。
2-1. 旋盤加工の基本技術
- 切削速度の設定: 砲金は比較的柔らかい金属ですが、適切な切削速度で加工しないと、摩耗や熱の発生を抑えられません。切削条件を最適化することが必要です。
- 工具の選定: 切削工具は砲金の特性に合わせて選定します。高精度な仕上げが必要な場合は、超硬工具やコーティングされた工具が適しています。
2-2. 砲金の切削加工方法
- 粗加工: 粗加工では大きな切削量を扱うため、刃先がしっかりした工具を使用します。切削速度を適切に調整し、振動や工具の摩耗を防ぎます。
- 仕上げ加工: 仕上げ加工は精度が求められるため、刃先が鋭い工具を使用します。軽い切削負荷で精密な仕上げを行い、表面粗さを最小限に抑えます。
2-3. 旋盤加工における工具の選定
- 超硬工具: 高硬度の砲金を切削する際には超硬工具が最適です。耐摩耗性が高く、長寿命を持ちます。
- コーティング工具: TiNやTiAlNコーティングを施した工具は、高温での加工にも耐えるため、効率的な加工が可能です。
- 研削工具: 精密な仕上げが必要な場合には、研削工具を使用して表面を滑らかに仕上げます。
3. 旋盤加工時に注意すべき点
砲金の旋盤加工では、加工精度や工具の選定が特に重要です。加工中のトラブルを防ぐために、注意すべきポイントを確認しておきましょう。
3-1. 加工条件の設定
- 適切な切削速度: 砲金は適切な切削速度を設定することで、加工効率と工具寿命を最大化します。過度な切削速度は工具摩耗を早め、仕上がりが悪化する原因になります。
- 切削深さの調整: 切削深さが深すぎると、工具に過負荷がかかり、表面の仕上がりが悪くなる可能性があります。加工する部品に最適な切削深さを設定することが重要です。
3-2. 切削液の選び方
- 冷却性能: 砲金の加工では、切削液の冷却性能が非常に重要です。冷却不足の場合、工具摩耗が進行しやすくなり、加工精度が低下します。
- 切削液の種類: 水溶性の切削液や油性の切削液がありますが、砲金の加工には水溶性の切削液が一般的に適しています。加工中の温度管理にも役立ちます。
3-3. 加工中のトラブルとその対策
表面粗さの不良: 表面が粗く仕上がってしまう場合、切削条件や工具選定を再評価します。また、仕上げ加工時の切削負荷を減らすことも効果的です。
工具摩耗: 砲金の加工では工具の摩耗が早く進むことがあります。摩耗が激しい場合、切削条件の再設定や工具交換を検討します。
4. 砲金の特性を活かした成功事例
砲金はその優れた耐摩耗性や耐食性、加工性を活かし、さまざまな産業で成功事例を生んでいます。これらの事例は、砲金の特性を最大限に活用した設計や製造プロセスが成功を導いた結果です。
4-1. 産業別の成功事例
- 自動車産業: 砲金はエンジン部品やポンプ、ギアなどに使用され、特に摩耗や腐食に強いことが求められる部品で多く利用されています。例えば、自動車の冷却系統や燃料系統において、長寿命を提供する部品が求められます。
- 船舶産業: 船舶のスクリューやプロペラ、海水冷却部品に砲金が使用され、海水による腐食から守られています。砲金の耐食性が船舶部品の長期運用に貢献しています。
- 航空産業: 高温や腐食の厳しい環境で使用される航空機の部品にも砲金が利用されており、特にエンジンや機体の一部で使用されることが多いです。
4-2. 砲金を使用した製品の紹介
- ポンプ部品: 高耐食性と高耐摩耗性が求められるポンプのインペラやシール部品に砲金が使用されています。特に、海水を扱うポンプでは砲金がその耐食性を発揮します。
- 歯車やベアリング: 高摩耗性を持つ歯車やベアリングにも砲金は使用されており、長寿命で高い精度が求められる機械部品に最適です。
5. 適切な銅材料の選び方
銅合金の選定は、使用環境や要求される特性に基づいて慎重に行う必要があります。特に、砲金や真鍮など、異なる銅合金の特性を理解し、最適な選定をすることが重要です。
5-1. 材料選定の基準
- 強度: 使用される部品に必要な強度を満たす材料を選びます。高強度を必要とする場合は、砲金や青銅などが選ばれます。
- 耐摩耗性: 長期間使用する部品や摩耗の激しい環境では、耐摩耗性の高い材料を選びます。砲金は摩耗に強く、機械部品に適しています。
- 耐食性: 海水や化学薬品が関わる環境では、耐食性の高い材料が重要です。砲金や黄銅は耐食性に優れており、これらの環境で使用されます。
5-2. 砲金と真鍮の選び方
- 砲金: 耐摩耗性と耐食性が求められる環境では、砲金が最適です。特に、高温環境や海水など過酷な条件で使用される部品には砲金が適しています。
- 真鍮: 真鍮は加工性が高く、比較的軽い負荷の環境で使用される部品に適しています。低摩耗性が求められる部品や装飾部品には真鍮がよく使用されます。
6. 金属加工の基礎知識
金属加工にはさまざまな方法がありますが、それぞれの方法に特徴と利点があります。基礎的な知識を持つことで、加工方法の選定がより効果的になります。
6-1. 切削加工のメリット
- 高精度: 切削加工は非常に高い精度を持つため、精密部品の製造に向いています。微細な形状を作成することが可能です。
- 多様性: 切削加工は、金属の種類に関わらず広く適用できるため、さまざまな材料の部品製造に使用されます。
- 高効率: 複雑な形状や高精度な部品を大量生産することができるため、コスト削減にも寄与します。
6-2. 金属加工の種類と特徴
鋳造加工: 大きな部品や複雑な形状の製造に使用され、金型を使って金属を溶かし、型に流し込む方法です。
旋盤加工: 円筒形の部品を作成するための加工方法で、高い精度と滑らかな表面仕上げが可能です。
フライス加工: 複雑な形状や精密な切削が必要な場合に使用される加工方法で、広範囲な用途があります。
研削加工: 高精度な仕上げが必要な場合に使用され、非常に高い表面仕上がりが得られます。
まとめ
砲金旋盤加工は、優れた耐摩耗性と加工性を持つ材料を使用した精密加工技術です。特性としては、耐腐食性や強度が挙げられますが、高温には弱い点も注意が必要です。加工時は、適切な切削条件を設定し、工具の選定にも気を配ることが重要です。これにより、品質の高い製品を効率的に生産できます。
精密金属部品製造の品質基準とは?依頼前に確認すべきポイント
精密金属部品の製造を依頼しようと考えたとき、どのような品質基準を求めるべきか迷うことはありませんか?特に、部品の精度や耐久性が重要な役割を果たす業界においては、品質の確保が不可欠です。このガイドでは、「精密金属部品製造の品質基準」について詳しく解説し、依頼前に確認すべきポイントをお伝えします。
この文章は、以下のような疑問を持つ方々に向けています。
- 精密金属部品の品質をどのように評価すればよいのか?
- 依頼先の製造業者にどのような品質基準を確認すれば安心できるのか?
- 質の高い部品を得るために必要なステップは何か?
精密金属部品の製造では、品質管理が成功の鍵を握ります。本記事では、業界でのベストプラクティスや、依頼時に重視すべき品質基準を本格的に探ります。これを読めば、安心して依頼できる製造パートナーを見つける手助けとなることでしょう。さあ、一緒に品質について深堀りしていきましょう。
1. 精密金属部品の製造を依頼する際に求めるべき品質
精密金属部品の製造を依頼する際には、部品の精度や耐久性を確保するために、高い品質基準を設けることが重要です。以下の方法で品質の確認を行います。
1-1. 精密金属部品の品質管理の重要性
- 品質の一貫性:
- 生産過程での品質管理は部品の一貫した精度を保証するために不可欠です。異常が発生する前に問題を検出し、修正を行うことが重要です。
- 信頼性の向上:
- 高品質な部品を製造することにより、最終製品の信頼性を向上させ、顧客の満足度を高めます。
- コスト削減:
- 品質管理により、不良品の発生を防ぎ、リワークやスクラップのコストを削減できます。
1-2. 品質管理の具体的な方法
- 統計的品質管理(SQC):
- 工程内でのデータ収集と分析を行い、品質の問題が発生する前に対処する手法です。コントロールチャートを使用して、製造工程を監視します。
- FMEA(故障モード影響分析):
- 製造工程の各段階で発生しうるリスクを特定し、それに対する対策を講じます。予防的な手法として有効です。
- ISO 9001認証:
- 国際標準に基づいた品質管理システムを導入し、品質を一貫して管理するための枠組みを提供します。
1-3. 品質基準と認証の確認
- 国際規格(ISO):
- 精密金属部品の製造には、ISO 9001やISO 13485などの規格に準拠した品質管理が求められます。これらの認証を確認することで、品質の信頼性を担保できます。
- 業界標準の遵守:
- 航空、医療、半導体など特定の業界には、独自の品質基準があります。これらに準拠することで、特定の市場向けの高品質な製品を提供できます。
- トレーサビリティの確保:
- 部品の製造履歴や使用した材料などを追跡できる体制を整えることで、万が一の不具合発生時にも迅速に原因を追及できます。
2. 精密金属部品の製造を依頼する際に求めるべき品質に適した測定器の選び方
精密金属部品の品質管理には、適切な測定器の選定が不可欠です。測定器の選び方を以下に示します。
2-1. 測定器の種類と特徴
- 三次元測定機(CMM):
- 部品の寸法や形状を非常に高精度で測定するための装置です。多軸で部品を測定できるため、複雑な形状の部品にも対応可能です。
- デジタルノギス:
- 小型部品や簡単な形状の部品の測定に適した工具です。高精度で簡単に使用でき、頻繁に利用されます。
- 表面粗さ測定機:
- 部品の表面の粗さを測定する機器で、特に仕上げが重要な部品に使用されます。表面品質の管理に役立ちます。
- 顕微鏡:
- 微細な表面や寸法を高倍率で確認できるため、微細加工や研磨後の仕上がり確認に使用します。
2-2. 測定器の選び方
- 測定精度と範囲の確認:
- 部品の要求精度に応じて、測定器の精度や測定範囲を選定します。精度が高い機器を選ぶことで、品質の確保が可能です。
- 使用環境の考慮:
- 測定器が使用される環境に応じて、耐久性や温度、湿度に対する適応力を考慮します。過酷な環境下でも安定した測定を行える機器を選ぶことが重要です。
- 操作の簡便さ:
- 測定器の操作性が高いことも重要です。熟練した技術者だけでなく、誰でも使える直感的な操作ができる測定器が望ましいです。
2-3. 測定器の使い方と注意点
精密金属部品の品質管理には、適切な測定器の選定が不可欠です。測定器の選び方を以下に示します。
校正と定期的な点検:
測定器は定期的に校正を行い、その精度を確認する必要があります。校正された状態で使用することが信頼性の確保に繋がります。
使用前後の清掃と保管:
測定器を使用する前後に清掃を行い、汚れや異物を取り除くことで、測定精度を保つことができます。また、使用後の適切な保管方法も大切です。
操作マニュアルの遵守:
測定器の取扱説明書に記載された操作方法を遵守し、正しい手順で測定を行います。誤った操作は精度に影響を及ぼす可能性があります。
3. 工作機械を用いた精密部品製造のプロセス
工作機械を使用して精密部品を製造するプロセスは、高精度な部品を確保するために重要です。適切な工作機械の選定と工程管理が品質向上に繋がります。
3-1. 工作機械の種類と役割
- 旋盤: 部品を回転させながら切削を行う機械で、円形部品や回転軸を持つ部品の加工に使用されます。精密な外形加工が可能です。
- フライス盤: 回転する工具を使って部品を削る機械で、平面や溝、穴の加工に適しています。多方向からの加工が可能です。
- マシニングセンター: 旋盤とフライス盤の機能を兼ね備えた工作機械で、複雑な形状の部品を1台で加工できる利点があります。
- 放電加工機(EDM): 電気放電を使って金属を加工する機械で、非常に硬い材料や複雑な形状の部品の加工が可能です。
- 研削盤: 精密な表面仕上げを行うための機械で、特に高精度な寸法や滑らかな表面仕上げが求められる部品に使用されます。
3-2. 精密部品製造の流れ
- 設計: 初めにCAD/CAMソフトを使って部品の設計を行います。設計時には材料特性や加工性を考慮する必要があります。
- 素材選定: 部品に適した材料を選定します。精密部品には、耐摩耗性や強度が求められるため、適切な金属や合金が選ばれます。
- 加工準備: 加工機械を設定し、工具や治具を準備します。部品の寸法や形状に応じて最適な加工方法を選択します。
- 加工: 選定された工作機械で部品の加工を行います。精密な加工が求められるため、切削条件や加工順序を最適化します。
- 仕上げ: 研削や放電加工で仕上げを行い、部品の寸法精度や表面仕上げを確認します。
- 検査: 完成した部品を各種測定機器で検査し、設計通りの精度が出ているかを確認します。問題があれば、再加工を行います。
4. 金属加工を依頼する際の業者選びのポイント
金属加工を依頼する業者選びは、製品の品質に直接影響を与えるため、慎重に行うべきです。信頼できる業者を選ぶためのポイントを以下に示します。
4-1. 業者の信頼性の確認
- 認証の確認: ISO 9001などの品質管理に関する認証を保有している業者は、一定の品質基準を維持している証拠です。
- 企業の歴史と実績: 業者の歴史や長年の経験は、製造品質や対応力において重要な指標です。安定した実績のある企業を選びましょう。
- アフターサービス: 納品後のサポート体制や不具合対応の迅速さも重要な要素です。
4-2. 過去の実績と顧客の声
- 過去の納品事例: 業者のウェブサイトやパンフレットで過去の実績を確認します。類似の部品や業界での経験が豊富であれば、安心して依頼できます。
- 顧客の声: 他の顧客からのフィードバックや評価を確認することで、業者の信頼性や品質に対する評価が分かります。顧客満足度が高い業者を選ぶことが重要です。
4-3. 提供されるサービスの内容
品質管理体制: 加工の精度や品質を保証するために、業者がどのような品質管理体制を採用しているかを確認します。検査体制やトレーサビリティの確保が求められます。
製造プロセスの透明性: 業者がどのような製造プロセスを採用しているかを確認します。自社の要求に応じて柔軟に対応できるか、透明性があるかをチェックしましょう。
納期とコストの提案: 明確な納期と適切なコスト提案を行う業者を選びます。納期遅延や過度なコストは後々問題になるため、事前に確認することが重要です。
まとめ
精密金属部品製造の品質基準は、寸法精度、表面仕上げ、材質特性、熱処理、検査方法などが含まれます。依頼前には、これらの基準を明確にし、製造業者とのコミュニケーションを密にすることが重要です。また、過去の実績や認証を確認し、信頼性を確保することも忘れずに。
黄銅部品の品質向上!検査精度を高めるための実践的な技術
黄銅部品は、さまざまな産業で広く使用されている重要な材料ですが、その品質が求められる場面は多岐にわたります。「黄銅部品の品質向上!検査精度を高めるための実践的な技術」というタイトルには、そんな皆さんの悩みを解決するための知識が詰まっています。
「どのようにして黄銅部品の検査精度を向上させることができるのか?」と考える製造業の担当者や技術者の方々に向けて、この記事では具体的な手法や技術的なポイントを詳しく解説します。品質管理や製品の信頼性向上に関心のある方々にとって、この記事が実用的なヒントを提供できれば幸いです。
検査精度が向上すれば、製品の不良率を低下させることができ、ひいては顧客満足度の向上にも寄与します。それでは、黄銅部品の検査精度を向上させるための具体的な技術や方法を一緒に見ていきましょう。あなたの作業現場に新たな価値をもたらす情報が満載です。
1. 黄銅部品の検査精度を向上させる方法
黄銅部品の製造においては、検査精度の向上が品質確保に直結します。以下の方法で検査精度を向上させることが可能です。
1-1. 黄銅部品の量産における失敗を避けるためのポイント
- 設計段階での精密化:
- 設計時に公差を厳密に設定し、使用する機器や加工技術に合わせた適切な規格を選定します。
- 加工前の部品確認:
- 量産前に試作品を作成し、検査を行うことで、量産中の不具合を事前に予測し、改善点を見つけることができます。
- 品質管理システムの確立:
- 品質管理の体制を整え、各工程でのチェックリストや基準を設け、トラブルの早期発見を目指します。
1-2. NC切削の効率を向上させるためのテクニック
- 最適な工具と切削条件の選定:
- 使用する工具の選定や回転速度、送り速度など、NC機械の設定を最適化し、効率的に加工を進めます。
- 工具の管理と交換タイミング:
- 定期的に工具の状態をチェックし、摩耗や劣化が進んだ場合には速やかに交換します。これにより、精度が維持され、品質のばらつきを防げます。
- プログラムの最適化:
- 加工プログラムを最適化して、無駄な動きを減らし、効率よく加工できるようにします。これにより、加工時間を短縮し、コスト削減にもつながります。
1-3. 加工精度を高めるための具体的な手法
- 高精度な測定機器の使用:
- 精度が要求される部品の場合、3D測定機やCNC測定機を使用し、細部まで精密に測定します。これにより、加工後の検査精度が向上します。
- 温度管理の徹底:
- 加工中や加工後の部品が熱によって変形しないよう、温度管理を行います。冷却装置を導入し、適切な温度範囲内で加工を行うことが大切です。
- 手作業と機械加工の組み合わせ:
- 機械加工だけでなく、仕上げ段階で手作業を加えることで、微細な調整が可能となり、最終的な精度を高めることができます。
1-4. コスト削減と強度維持の両立方法
- 材料の選定と加工方法の最適化:
- 適切な材料を選ぶことで、強度を維持しながらコストを抑えることができます。また、最適な加工方法を選択することで、無駄なコストを削減できます。
- 高効率な機械導入:
- 新しい技術や高効率な加工機を導入することで、加工時間の短縮とエネルギーの節約が可能となり、コスト削減に貢献します。
- 一貫生産ラインの導入:
- 一貫した生産ラインを整えることで、無駄な工程を削減し、強度の維持とコスト削減を同時に実現できます。
1-5. 加工中の傷を除去するための効果的なアプローチ
加工後に表面を確認し、万が一傷が発生している場合には、修正作業を行います。これにより、品質を保持できます。
表面仕上げの工夫:
加工後の表面仕上げを工夫することで、傷の除去や表面の平滑化が可能です。例えば、研磨やブラスト処理などが有効です。
傷防止のための工具選定:
適切な工具を選ぶことで、加工中の傷の発生を防ぎます。特に、工具の材質やコーティングを慎重に選び、加工条件を調整します。
加工後の点検と補修:
加工後に表面を確認し、万が一傷が発生している場合には、修正作業を行います。これにより、品質を保持できます。
まとめ
黄銅部品の品質向上には、検査精度の向上が不可欠です。実践的な技術として、画像処理技術や非破壊検査、統計的プロセス制御が挙げられます。これらを活用することで、欠陥の早期発見や製品の一貫性を確保し、全体的な生産性を向上させることが可能です。
銅合金加工を進化させる!精度向上のためのテクニックとポイント
銅合金は、電気伝導性や耐腐食性が求められる様々な場面で重要な役割を果たしています。しかし、その加工においては高い精度が要求されることが多く、技術者たちは常に新しいテクニックや方法を模索しています。「銅合金加工を進化させる!」というテーマのもと、あなたはおそらく「どうすればこの加工精度を向上させることができるのか?」と考えているかもしれません。
この記事では、銅合金の精度向上に焦点を当て、実践的な加工技術やポイントを詳しく解説します。特に、加工の現場で役立つ具体的なテクニックや、最新の技術動向についても触れる予定ですので、これから銅合金加工に挑戦したい方や、さらなるスキルアップを目指す方には必見の内容です。
銅合金の加工は単なる技術だけではなく、材料の特性を理解することが成功の鍵でもあります。あなたの加工スキルを一歩先へ進めるための知識を、ぜひこの記事で身につけてください。
1. 銅合金の精度向上のための加工技術とは
銅合金の加工精度を向上させるためには、適切な加工技術と条件設定が欠かせません。精度の高い加工は、部品の性能や寿命に大きな影響を与えます。
1-1. 銅合金の加工精度を高めるための基本原則
- 工具の選定:
- 銅合金には、耐摩耗性と耐熱性が求められます。超硬工具やコーティングツールを使用することで、工具の寿命を延ばし、安定した加工が可能になります。
- 切削条件の設定:
- 適切な回転数、送り速度、切削深さを設定することが重要です。これにより、過剰な摩耗を防ぎ、精度を保つことができます。
- 冷却と潤滑の管理:
- 銅合金は熱伝導性が高いため、加工中に発生する熱を適切に管理することが必要です。冷却材や潤滑剤を効果的に使用することで、熱による変形や工具摩耗を防ぎます。
1-2. 最新の加工技術とその効果
- CNC加工技術:
- 数値制御(CNC)による精密な加工は、銅合金においても非常に効果的です。高精度の位置決めと制御により、微細な加工が可能になります。
- レーザー加工:
- レーザー加工は、非常に高い精度で銅合金の切断や穴あけを行うことができます。金属の熱膨張を最小限に抑えることができ、微細な部品の加工に適しています。
- 放電加工(EDM):
- 放電加工は硬い銅合金の精密加工に適しています。微細な形状の加工や深い穴あけが可能で、複雑な形状にも対応できます。
2. 銅を加工する際に注意すべきポイント
銅合金は加工が容易である一方、適切な条件で行わないと精度が落ちたり、工具寿命が短くなることがあります。加工時に注意すべきポイントを確認しましょう。
2-1. 材料特性の理解
- 熱伝導性の高さ:
- 銅合金は熱伝導性が高いため、加工中に熱が集中しやすく、工具や部品が過熱しやすいです。冷却や潤滑を適切に行い、過熱を防ぐことが大切です。
- 軟らかさと摩耗:
- 銅合金は比較的軟らかい材料であり、工具に対する摩耗が激しくなることがあります。これを防ぐために、適切な工具を選ぶと共に、切削条件を最適化することが必要です。
2-2. 加工条件の最適化
適切な切削油や冷却剤を選定することで、加工中の温度上昇を抑え、加工精度を向上させるとともに、工具寿命を延ばすことができます。特に銅合金のような熱伝導性が高い材料には、冷却効率の良いものを使用することが効果的です。
切削速度と送り速度の調整:
銅合金の加工時には、切削速度を高く設定することで、表面仕上げの品質が向上します。しかし、送り速度を適切に調整しないと表面が荒れたり、工具の寿命が短くなる原因になります。
切削油の選定:
適切な切削油や冷却剤を選定することで、加工中の温度上昇を抑え、加工精度を向上させるとともに、工具寿命を延ばすことができます。特に銅合金のような熱伝導性が高い材料には、冷却効率の良いものを使用することが効果的です。
3. 銅合金の微細加工技術の活用法
銅合金の微細加工は、高精度な部品を必要とする分野で重要です。微細加工技術を適切に活用することで、銅合金の加工精度や効率を大幅に向上させることができます。
3-1. 微細加工技術の種類
- レーザー加工:
- 高精度で微細な形状を作成するために使用されるレーザー加工は、銅合金にも適しています。光の集束を利用して、非常に細かい穴やスリットを作成できます。
- EDM(放電加工):
- 放電加工は、電気的な放電を使用して金属を除去します。非常に硬い銅合金でも微細な形状を作成することが可能で、複雑な形状の部品にも対応できます。
- CNCミーリング:
- 数値制御による精密な切削が可能なCNCミーリング技術は、銅合金の微細加工においても利用され、非常に高い精度で仕上げられます。
- マイクロ切削:
- 微細な工具を使用して、精密な部品を加工する方法です。ナノレベルの精度を要求される場合にも利用されます。
3-2. 微細加工による精度向上の事例
- 精密電子部品の製造:
- 微細加工技術を駆使することで、銅合金製の電子部品や基板に非常に細かい配線や穴を作成することができます。これにより、電子機器の小型化や性能向上が可能になります。
- 医療機器の精密部品:
- 銅合金を使用した医療機器の部品においても、微細加工技術が活用されています。細い管や精密なスリット加工を通じて、高精度な部品が作成されています。
4. 銅の穴あけ加工が難しい理由とその対策
銅合金の穴あけ加工は、他の金属に比べて難易度が高い場合があります。これは、銅の特性や加工中に発生する問題に起因しています。
4-1. 穴あけ加工の難しさの要因
- 熱伝導性の高さ:
- 銅は熱伝導性が非常に高いため、加工中に発生した熱が迅速に工具や加工部品に伝わります。このため、工具が過熱しやすく、摩耗や変形を引き起こすことがあります。
- 材料の柔らかさと塑性変形:
- 銅合金は比較的柔らかく、加工中に材料が変形しやすいです。このため、穴あけ時にバリが発生したり、穴がきれいに開かないことがあります。
- 切削力の発生:
- 穴あけ時に必要な切削力が大きく、工具にかかるストレスが高くなります。このため、工具の摩耗が進みやすく、加工精度が低下する可能性があります。
4-2. 効果的な対策方法
銅合金専用の切削工具を使用することで、加工時の摩耗を抑え、穴あけ精度を高めることが可能です。特に、超硬工具やコーティングされた工具を選ぶことが有効です。
冷却と潤滑の強化:
適切な冷却剤や潤滑剤を使用することで、加工中の熱の発生を抑え、工具の摩耗や材料の過熱を防ぐことができます。また、冷却を効果的に行うことで、穴あけ精度が向上します。
低速での穴あけ:
銅合金の穴あけは、適切な回転数を設定し、低速で行うことで、熱の蓄積を防ぎ、精度を向上させることができます。
特殊な穴あけ工具の使用:
銅合金専用の切削工具を使用することで、加工時の摩耗を抑え、穴あけ精度を高めることが可能です。特に、超硬工具やコーティングされた工具を選ぶことが有効です。
まとめ
銅合金加工の精度向上には、適切な工具選定、切削条件の最適化、冷却剤の活用が重要です。また、加工前の材料検査や、加工後の品質管理も欠かせません。これらのテクニックを駆使することで、効率的かつ高精度な製品を実現できます。
旋盤の設定で差をつける!砲金加工に最適な調整方法とは?
あなたは「砲金加工を行う際に、旋盤の設定がうまくできない…」と悩んでいませんか?そんな方々のために、今回は「砲金加工における旋盤の最適設定」について徹底解説します。
この文章は以下のような方々に向けています:
- 砲金加工の技術を向上させたいが、何から始めればいいのか分からない。
- 旋盤の設定についての知識を深め、加工精度を向上させたい。
- 成果を最大化するための旋盤の調整方法を知りたい。
砲金はその特性から、多くの産業で重宝されていますが、加工においては高度な技術が求められます。旋盤の設定一つで製品の仕上がりが大きく変わるため、最適な調整方法を身につけることが非常に重要です。
この記事では、砲金加工における旋盤の設定方法を詳しく解説し、皆さんが必要とする知識を提供します。さあ、一緒に高精度な加工技術を身につけて、加工現場で差をつけていきましょう!
1. 砲金加工における旋盤の最適設定
砲金加工においては、適切な旋盤設定と技術を活用することが、精度の高い仕上げを実現するための鍵となります。ここでは、砲金を旋盤で加工する際の最適設定について解説します。
1-1. 砲金加工における適切な切削バイトの選び方
- 切削バイトの選定:
- 砲金の加工には、硬度が高く耐摩耗性に優れた切削バイトを選ぶことが重要です。
- 超硬工具: 高精度が求められる場合、超硬工具を使用することで長寿命と優れた加工精度を確保できます。
- コーティング工具: 切削バイトにコーティングを施すことで、耐熱性と耐摩耗性を向上させることができます。
1-2. 真鍮、黄銅、砲金の違いとそれぞれの用途
- 真鍮:
- 銅と亜鉛の合金。主に装飾品や楽器部品、配管に使用される。
- 加工性が良好で、一般的な用途に適しています。
- 黄銅:
- 真鍮に近いが、亜鉛が高含有の合金。機械部品や電子機器の接続部品として使用されます。
- 耐食性と加工性が特徴。
- 砲金:
- 銅とスズを基にした合金。耐食性と耐摩耗性が求められる部品に使用されます。
- 特に船舶や自動車部品、機械装置など、摩耗の多い環境に最適です。
1-3. NC旋盤での銅合金の仕上げ技術
- NC旋盤の活用:
- 銅合金の仕上げには、NC旋盤を使用することで高い精度を実現します。特に複雑な形状を一度に加工できるため、効率が良いです。
- 回転数と送り速度: 銅合金の加工には、適切な回転数と送り速度を設定し、仕上げ面の精度を高めます。
1-4. 銅合金の旋盤加工における切削のポイント
- 切削油の使用: 銅合金は高い熱伝導性を持っているため、切削時に熱が発生しやすいです。切削油を適切に使用し、熱を効果的に放散させることが重要です。
- 送り速度と切削深さ: 切削深さはあまり大きくせず、送り速度は適切に調整して、安定した加工を行います。
1-5. 旋盤加工における成功事例と注意点
成功事例:
高精度な軸部品の加工で、適切な回転数、送り速度、切削バイトの選定によって、非常に精密な仕上げを実現した事例があります。
注意点:
工具の選定: 適切な切削工具を使用しないと、表面仕上げが粗くなることがあります。工具の交換時期を見極め、品質を保つようにしましょう。
熱の管理: 銅合金は熱を持ちやすく、加工時に変形や工具の摩耗が進むことがあるため、冷却方法をしっかりと管理することが必要です。
まとめ
砲金加工において、旋盤の設定は品質向上に不可欠です。最適な切削速度や送り速度を選定し、工具の摩耗を最小限に抑えることが重要です。また、冷却液の適切な使用や振動の管理も加工精度を高める要素です。これらの調整を行うことで、効率的かつ高品質な仕上がりが実現できます。
黄銅部品の検査基準とは?品質を保つための重要なポイント
黄銅部品は、様々な産業で広く使用されていますが、その品質が製品全体の信頼性やパフォーマンスに大きく影響します。「黄銅部品の検査基準について理解したいけれど、何から始めればいいのか分からない」という方も多いのではないでしょうか。あなたがもし、黄銅部品の製造や品質管理に携わっているなら、このガイドはぜひお役立てください。
この記事では、黄銅部品の検査基準の基本から、その重要性、さらには品質を維持するためのポイントに至るまで、必要な情報を詳しく解説します。品質管理は単なるプロセスではなく、顧客の信頼を築くための重要な要素です。この情報を通じて、あなたの製品が市場で競争力を持つために必要な知識を身につけましょう。黄銅部品の検査基準を理解することで、より良い製品作りに向けた第一歩を踏み出すことができるでしょう。
1. 黄銅部品の検査基準とその重要性
黄銅部品の品質を確保するためには、適切な検査基準を設けることが不可欠です。精密加工や電気部品など、用途に応じた基準を設定することで、製品の信頼性を向上させることができます。
1-1. 黄銅部品の検査基準とは
黄銅部品の検査基準には、以下のような項目が含まれます。
- 寸法検査(公差の確認、CNC加工後の精度測定)
- 表面検査(傷や打痕の有無を目視確認)
- 材料成分検査(成分分析機器を使用して適切な合金比率か確認)
- 機械的特性検査(硬度試験、引張強度試験など)
- 導電性試験(電気部品用途の場合、導電率の測定)
1-2. 検査基準が重要な理由
黄銅部品の検査基準を厳格に設定する理由は以下のとおりです。
- 品質の均一性を確保するため
- 同じ製品でも加工誤差が生じるため、基準を設けてばらつきを抑える
- 耐久性を向上させるため
- 適切な材料特性や加工精度を保つことで、長期間の使用に耐える部品を作る
- 安全性の確保
- 電気部品や機械部品に使用される場合、不良品が故障や事故を引き起こす可能性がある
2. 黄銅と真鍮の違い
黄銅と真鍮は同じ銅合金の一種ですが、成分や性能が異なるため、用途によって使い分けられます。
2-1. 黄銅と真鍮の成分の違い
項目 | 黄銅 (Brass) | 真鍮 (Brass) |
---|---|---|
主成分 | 銅 (Cu) + 亜鉛 (Zn) | 銅 (Cu) + 亜鉛 (Zn) + その他元素(鉛、スズ など) |
亜鉛含有率 | 5%~40% | 5%~40%(一般的に鉛やスズを含む) |
その他成分 | – | 鉛(快削性向上)、スズ(耐食性向上) |
2-2. 性能と用途の違い
- 黄銅の特徴と用途
- 軟らかく、加工しやすい
- 電気・電子部品、装飾品、楽器に使用
- 真鍮の特徴と用途
- 鉛を含むため、快削性が向上
- 水道管部品、バルブ、ギアなどに使用
3. 目視検査の具体的な方法
目視検査は簡易的かつ重要な検査方法であり、表面の傷や異物混入を確認するために行われます。
3-1. 目視検査の手順
- 適切な照明の下で検査(明るさ1,000ルクス以上が推奨)
- 部品を回転・角度を変えながら確認(反射光で傷を確認)
- 異常があればマーキング(傷の場所を特定し、詳細な測定へ)
- 基準と照らし合わせて合否判定(基準外なら追加検査や再加工)
3-2. 目視検査における課題と解決策
- 課題①:検査精度のばらつき
- 解決策:チェックリストを作成し、標準化する
- 課題②:微細な傷や異常の見落とし
- 解決策:拡大鏡やLEDライトを使用し、詳細確認を行う
- 課題③:検査員の疲労による判断ミス
- 解決策:一定時間ごとに休憩を取り、集中力を維持する
これらの対策を講じることで、目視検査の精度を向上させ、黄銅部品の品質を安定させることができます。
4. 外観検査の基準の確立
外観検査は、黄銅部品の品質を保証するために重要なプロセスの一つです。加工精度が高くても、表面の傷や欠陥があると製品の信頼性が損なわれるため、明確な基準を設定することが不可欠です。
4-1. 外観検査の重要性
- 製品の品質を一定に保つ
表面仕上げや傷の有無を統一することで、製品の品質を均一化する - 顧客満足度の向上
目に見える欠陥を取り除くことで、クレームや返品を防止できる - 加工工程の改善につなげる
検査結果をもとに加工プロセスの見直しが可能になる
4-2. 外観検査の基準設定のポイント
- 表面の傷や凹みの許容範囲
目視や拡大鏡を用いて、傷の深さや大きさを規定 - 変色や酸化の許容範囲
経年変化で変色しやすいため、納品時点での基準を定める - 仕上げの均一性
研磨やコーティングの仕上がりにばらつきがないか確認 - 異物の混入防止
加工時の油や粉塵の付着がないかをチェック - 測定方法の標準化
LED照明下での検査や一定距離からの観察を統一ルールとして設定
5. 黄銅の特性と用途
黄銅は、その物理的特性と優れた加工性により、幅広い分野で使用されています。
5-1. 黄銅の物理的特性
- 比重:8.4~8.7
- 引張強度:200~600 MPa(成分や加工方法による)
- 伸び:10~50%(柔軟性が高い)
- 導電率:銅の約20~30%
- 耐食性:空気中や淡水では良好、塩水環境ではやや劣る
- 熱伝導率:100~150 W/(m・K)(銅より低いが、一般的な金属より高い)
- 加工性:切削性、プレス加工性に優れる
黄銅は亜鉛の割合によって硬さや強度が変わるため、用途に応じた合金を選択することが重要です。
5-2. 黄銅の主な用途
- 機械部品・工業用途
歯車、バルブ、軸受などの摩擦部品
水道管継手やポンプ部品 - 電気・電子部品
端子、コネクター、スイッチ
導電性と加工性を活かした用途 - 装飾品・デザイン用途
建築金物(ドアノブ、手すり)
楽器(トランペット、サックス) - その他の用途
時計や筆記具の部品
銅メダルやコインなど
黄銅は、耐食性と加工性を両立した材料であり、精密部品から装飾用途まで幅広く活用されています。
まとめ
黄銅部品の検査基準は、品質を確保するために重要です。主要なポイントには、寸法精度、表面仕上げ、機械的特性、耐食性の確認が含まれます。また、材料の均一性や組成分析も重要で、これにより信頼性の高い製品を提供できます。定期的な検査と適切な管理が品質維持に繋がります。
黄銅の旋盤加工の基礎知識と効率的な切削技術とは
「黄銅の旋盤加工について学びたいけれど、何から始めればいいのかわからない……」そんな悩みを抱えている方はいませんか?この記事では、そんなあなたのために黄銅の旋盤加工の基本的な知識と効率的な切削技術について詳しく解説します。
黄銅は美しい金属光沢を持ち、加工性にも優れた素材ですが、旋盤加工には特有の技術が求められます。効率的な切削技術を理解することで、作品のクオリティを向上させるだけでなく、生産性も高めることができるのです。
この記事を読むことで、黄銅の旋盤加工の基礎を理解し、自信を持って作業に取り組むことができるようになるでしょう。初心者から経験者まで、幅広い方々に役立つ内容を用意していますので、ぜひ最後までお読みください。黄銅の旋盤加工をマスターするための第一歩を踏み出しましょう!
黄銅の旋盤加工:効率的な切削技術とは
黄銅は、金属加工において非常に重要な素材であり、特に旋盤加工においてその加工性の良さが大きな利点となります。ここでは、黄銅の特性や旋盤加工の重要性、効率的な切削技術について解説し、さらに快削黄銅を使った生産性向上の方法についても触れます。
黄銅の特性と旋盤加工の重要性
黄銅は、主に銅と亜鉛の合金であり、その特性には以下のようなものがあります:
- 良好な加工性:黄銅は非常に加工しやすく、旋盤加工において優れた性能を発揮します。切削速度が比較的高く、加工中の温度も安定しています。
- 耐摩耗性:摩耗に強いため、旋盤加工後の部品が長寿命で使用されることが多いです。
- 優れた耐食性:特に湿気の多い環境でも腐食しにくく、耐食性を必要とする部品に最適です。
旋盤加工は、黄銅のこの特性を活かし、精密な部品製造や高い生産性を求める場面で重要な役割を果たします。
効率的な切削技術の基本原則
効率的な切削技術を実現するためには、いくつかの基本的な原則があります:
- 切削条件の最適化:切削速度、送り速度、切削深さの最適なバランスを取ることで、加工精度を保ちながら生産性を向上させることができます。
- 切削油の使用:切削油や冷却液の適切な使用は、切削温度を下げ、工具の寿命を延ばすだけでなく、加工面の仕上がりにも良い影響を与えます。
- 工具の適切な選定:工具の選定は、切削効率を大きく左右します。黄銅に最適な切削工具を使用することで、加工精度を維持しながら効率的に作業が進められます。
これらの原則を守ることで、無駄な手間や時間を省き、効率的な加工が可能になります。
切削工具の選定とその影響
切削工具の選定は、黄銅の旋盤加工において非常に重要です。以下のポイントが重要です:
- 材質とコーティング:黄銅に最適な工具材質としては、硬度が高く耐摩耗性に優れた材質を選ぶことが推奨されます。また、コーティングを施すことで、摩耗を減らし、加工精度を保ちやすくなります。
- 工具形状:切削工具の形状(例えば、刃先の角度や形状)も重要で、これが適切でないと、切削中に工具が早く摩耗し、精度が落ちる可能性があります。
- 工具の保守と管理:工具の状態を定期的にチェックし、必要に応じて交換や研磨を行うことが、効率的な加工を維持するためには欠かせません。
適切な工具を選定し、メンテナンスを行うことで、加工精度と生産性の向上が期待できます。
時間を短縮するための快削黄銅の加工方法
快削黄銅は、一般的な黄銅よりも加工性が良く、時間を短縮するために非常に有効な素材です。以下では、快削黄銅を使った効率的な加工方法を紹介します。
快削黄銅の特性と利点
快削黄銅は、通常の黄銅よりも切削性が大幅に向上しており、以下の特性があります:
- 低い切削力:切削時に発生する力が少なく、工具の負担を減らすことができます。
- 良好な仕上がり:加工後の表面仕上がりが滑らかで、追加の仕上げ作業が少なくて済みます。
- 工具寿命の延長:切削性が良いため、工具が長持ちし、頻繁な交換が不要です。
これらの利点により、快削黄銅は大量生産において特に効果的です。
加工条件の最適化
快削黄銅を使った加工では、以下の条件を最適化することで、さらに生産性を向上させることができます:
- 切削速度の向上:快削黄銅は高い切削速度での加工が可能であるため、速度を上げることで生産性を向上させます。
- 適切な切削油の使用:切削油を適切に使用することで、温度上昇を防ぎ、工具の摩耗を抑制します。
- 高精度な機械設定:高精度な旋盤を使用し、加工精度を確保することが、無駄をなくし、時間短縮に繋がります。
これらの条件をうまく調整することで、加工効率を最大限に引き出せます。
生産性向上のための工夫
生産性を向上させるためには、以下のような工夫が有効です:
- 一度の設定で複数部品を加工する:ワークを複数セットして、1回の加工で複数部品を仕上げることができます。
- 自動化の導入:機械の自動化を進めることで、作業の手間を減らし、さらに効率的に加工を進められます。
- 定期的な機械メンテナンス:機械の調子を常に良好に保つことで、安定した加工が可能となり、生産性が向上します。
これらの工夫を取り入れることで、より効率的な生産が実現します。
真鍮素材の特性と加工技術の理解
真鍮は、黄銅に似た特性を持ちますが、化学的特性や加工の挙動においては異なる点があります。真鍮の特性とその加工技術について理解することが、効果的な部品製作に繋がります。
真鍮の化学的特性
真鍮は、銅と亜鉛の合金であり、以下のような化学的特性があります:
- 優れた耐食性:湿気や酸化環境でも比較的腐食しにくく、特に海洋環境などでの使用に向いています。
- 高い導電性:電気を良く通し、電子機器などの部品に使用されることが多いです。
- 加工性:切削性が良く、精密な加工が可能であり、複雑な形状を作るのに適しています。
これらの特性を理解し、適切な加工方法を選ぶことが重要です。
加工における真鍮の挙動
真鍮は、加工中に以下のような挙動を示します:
- 加工中の膨張:真鍮は加熱されると膨張するため、加工時には熱の影響を最小限に抑える必要があります。
- 表面仕上がり:表面が非常に滑らかで仕上がりが良いため、追加の仕上げ加工が少なくて済むことがあります。
これらの挙動を考慮して、加工中の温度管理や工具選定が重要となります。
加工技術の選択肢
真鍮の加工においては、以下のような技術が選択肢としてあります:
- 旋盤加工:高い精度が求められる部品に最適で、真鍮の特性を活かした精密加工が可能です。
- フライス加工:複雑な形状を作るために使われ、非常に高精度な部品を作成できます。
- 鋳造:大量生産や複雑な形状を作る際に有効です。
適切な加工技術を選定することで、真鍮素材の特性を最大限に活かした部品が作成できます。
タップ加工やフライス加工の効率向上
タップ加工やフライス加工は、精密部品の製造において欠かせない工程です。これらの加工技術を効率的に行うことで、品質を維持しながら生産性を大きく向上させることができます。ここでは、それぞれの加工方法における効率向上のための基本的な手法やポイントを解説します。
タップ加工の基本と注意点
タップ加工は、内ネジを加工するための工程であり、精度の高いねじを作るためには適切な加工条件が重要です。基本的な注意点は以下の通りです:
- タップの選定:材料に適したタップを選ぶことが重要です。硬い材料には硬質コーティングが施されたタップを使用し、金属の特性に応じたサイズのタップを選びます。
- 回転数と送り速度の設定:回転数は、タップの種類と材料に合わせて最適に設定します。高速で回転させることで効率的な加工が可能になりますが、過剰な回転数はタップの摩耗を早めるため、バランスが重要です。
- 適切な冷却剤の使用:冷却剤はタップの寿命を延ばし、切削熱を下げる役割を果たします。使用する冷却剤は、材料に合わせて選定することが必要です。
フライス加工の効率的な手法
フライス加工は、様々な形状を加工するための方法であり、高精度が要求されることが多いです。効率的にフライス加工を行うための方法として、以下の手法が有効です:
- 適切な切削条件の設定:切削速度、送り速度、切削深さのバランスを適切に調整します。切削速度を最適化することで、加工時間を短縮し、工具の寿命を延ばします。
- 工具の選定:フライス加工では、工具の選定が非常に重要です。材料や加工する形状に応じて、コーティングされた工具や高硬度の工具を選ぶことが、加工効率を高める鍵となります。
- ワークの固定方法:ワークの固定が不安定だと、加工精度が低下し、加工時間も無駄になります。しっかりとした固定を行うことで、効率的に加工が進められます。
加工精度を高めるためのポイント
加工精度を高めるためには、以下のポイントを意識することが重要です:
- 機械の設定とメンテナンス:機械の精度を保つために、定期的なメンテナンスを行い、設定を正確に行うことが必要です。
- 工具の摩耗管理:工具が摩耗すると、加工精度が低下します。定期的に工具の状態をチェックし、早期に交換や再研磨を行うことが重要です。
- 測定機器の使用:加工後に高精度な測定機器を使用して、部品の寸法を確認することで、精度の高い加工が実現します。
真鍮の切削加工における最適な条件と注意点
真鍮は、加工性が良い素材として知られていますが、適切な加工条件を設定することで、より効率的で精度の高い加工が可能になります。以下では、真鍮の切削加工における最適な条件と注意点を解説します。
切削速度と送り速度の設定
真鍮を加工する際には、切削速度と送り速度の設定が非常に重要です:
- 切削速度:真鍮は比較的柔らかいため、高速で切削することが可能です。適切な切削速度を選定することで、加工時間を短縮できますが、過剰な速度設定は工具の摩耗を早めるため、適度な速度で行うことが推奨されます。
- 送り速度:送り速度は、材料の硬さや工具の種類に応じて設定します。適切な送り速度を設定することで、加工中の温度上昇を抑え、工具の寿命を延ばすことができます。
冷却剤の選定と使用方法
冷却剤は、切削加工中の温度を下げ、加工精度を保つために重要な役割を果たします。真鍮においては、以下のような冷却剤の選定と使用方法が効果的です:
- 水溶性冷却剤:真鍮の切削においては、水溶性冷却剤を使用することが多いです。冷却効果が高く、工具の摩耗を抑える効果があります。
- 油性冷却剤:高温が発生する加工には、油性冷却剤が有効です。油性の冷却剤は、摩耗を抑えつつ、切削面を滑らかに仕上げることができます。
冷却剤は、加工条件に合わせて選定し、適切に使用することが重要です。
加工後の仕上げと検査
加工後の仕上げ作業と検査は、部品の精度を保つために必要不可欠です:
- 仕上げ作業:加工後の仕上げ作業としては、研磨やバリ取りなどが行われます。特に真鍮は、表面仕上がりが重要であり、滑らかな仕上げをすることで部品の品質が向上します。
- 検査:加工後には、寸法や形状の検査を行い、基準を満たしているか確認することが必要です。精密な測定機器を使用して、誤差を最小限に抑えるようにします。
これらの工程をしっかりと行うことで、真鍮の切削加工における品質を確保できます。
まとめ
黄銅の旋盤加工では、適切な工具選定と切削条件が重要です。切削速度や送り速度を最適化することで、効率的な加工が可能になります。また、冷却剤の使用や切削工具の材質も、加工精度や工具寿命に影響を与えるため、慎重に選ぶことが求められます。
砲金部品制作の依頼方法と押さえておきたい注意点
砲金部品の制作を考えているものの、「どのように依頼すればいいのか、何に注意すればいいのかが分からない……」というお悩みを抱えている方はいませんか?そんなあなたのために、「砲金部品制作の依頼方法と押さえておきたい注意点」というガイドを用意しました。
このガイドは、次のような方々に最適です。
- 砲金部品を制作したいが、具体的な依頼手順が分からない。
- 制作依頼をする際に注意すべきポイントを知りたい。
- 依頼した部品の品質を確保するために必要な知識が欲しい。
砲金部品は耐久性や加工性に優れ、さまざまな産業で利用されていますが、制作プロセスには多くの要素が関与します。間違った依頼方法や無知からくる注意不足は、品質やコストに悪影響を及ぼす可能性があります。このため、正しい情報をもとに依頼を行うことが非常に重要です。
今回は、砲金部品制作の流れや具体的な依頼方法、さらに注意すべきポイントについて詳しく解説し、あなたの制作依頼を成功へと導くお手伝いをします。さあ、一緒に砲金部品制作の世界へ足を踏み入れてみましょう!
砲金部品の制作依頼方法と注意点
金属部品の制作を依頼する際、特に砲金や真鍮といった素材について理解を深めることが重要です。以下では、砲金部品の制作に関する依頼方法や注意点を詳しく解説します。
砲金と真鍮の違いについて
砲金と真鍮は、どちらも金属加工に使用される材料ですが、いくつかの特徴的な違いがあります。
- 砲金:
- 主成分は銅に錫(スズ)を加えた合金です。
- 高い耐摩耗性、耐食性を持ち、特に高負荷の機械部品に使用されます。
- 使用例:機械部品、船舶のパーツ、バルブなど。
- 真鍮:
- 銅と亜鉛の合金です。
- 加工性が良く、金属としての美しい金色が特徴です。
- 使用例:装飾品、楽器部品、電気接点など。
これらの違いを理解し、目的に合わせた素材選びが重要です。
金属加工の依頼方法
金属加工を依頼する際には、まず依頼する業者を選定することが重要です。以下は金属加工の依頼手順です:
業者の選定:
- 砲金や真鍮の加工に特化した業者を選びましょう。過去の実績や口コミをチェックするのがポイントです。
依頼内容の明確化:
- 依頼する部品の用途、サイズ、形状など、具体的な仕様を伝えます。
- 特に加工精度や納期など、重要な要件を明確にしておきましょう。
図面の提出:
- 可能であれば、設計図や図面を提出することが望ましいです。図面があれば、より正確な見積もりと製作が可能です。
お見積りの流れと依頼の手順
金属加工の依頼時には、見積もりの流れを把握しておくことが重要です。
見積もり依頼:
- 加工業者に依頼内容を伝え、見積もりを依頼します。この際、図面や詳細な仕様を一緒に送ることで、より正確な見積もりが得られます。
見積もりの確認:
- 提出された見積もりを確認し、価格、納期、加工精度に問題がないかチェックします。
- 価格交渉が可能な場合もあるので、納得できる内容に調整を依頼することもできます。
発注と契約:
- 見積もり内容に納得したら、発注契約を結びます。発注書には、納期や支払い条件などの重要事項を記載します。
制作開始:
- 契約後、金属加工が開始されます。納期に間に合うよう進捗を確認することが大切です。
真鍮の切削加工の具体的な情報
真鍮の切削加工には特有の技術が求められます。以下は、真鍮の切削加工に関する具体的な情報です:
- 切削加工の特徴:
- 真鍮は比較的柔らかい金属であり、加工が容易です。しかし、冷却材を適切に使用しないと、加工中に焼けてしまうことがあります。
- 使用される工具:
- 高速鋼(HSS)や超硬工具が使用され、精密な切削が求められます。
- 仕上げ方法:
- 真鍮は切削後に美しい仕上がりが期待できる金属の一つです。仕上げ工程として、研磨や表面処理を行い、製品の品質を高めます。
個人で金属加工を依頼する際の注意点
個人で金属加工を依頼する際は、いくつかの注意点があります。以下の点を踏まえて依頼を行いましょう:
業者選びの重要性:
- 大手の工場ではなく、専門的な金属加工業者を選ぶことが大切です。金属の種類や加工技術に精通している業者に依頼しましょう。
明確な仕様書の作成:
- 必要な部品の仕様(サイズ、形状、材質)をきちんと記載した仕様書を準備しましょう。図面があると、よりスムーズに進行します。
予算の設定:
- 予算が限られている場合は、最初に予算を伝え、コスト内で製作可能な範囲を確認しておくことが重要です。
納期の確認:
- 依頼する際に納期も必ず確認します。特に急ぎの場合、納期に関する合意を明確にしておくことが大切です。
品質管理の確認:
- 最終的な製品の品質に関する基準(寸法精度、表面仕上げ、耐久性など)を確認し、求める品質が保証されるように依頼します。
コミュニケーションの重要性:
進捗状況や問題が発生した場合の迅速な連絡体制を確認し、スムーズなやり取りができるようにしましょう。
まとめ
砲金部品制作の依頼は、まず仕様書を明確にし、必要な寸法や材質を伝えます。信頼できる業者を選び、過去の実績を確認することが重要です。また、納期やコストについても事前に合意し、コミュニケーションを密に保つことで、トラブルを防ぎます。