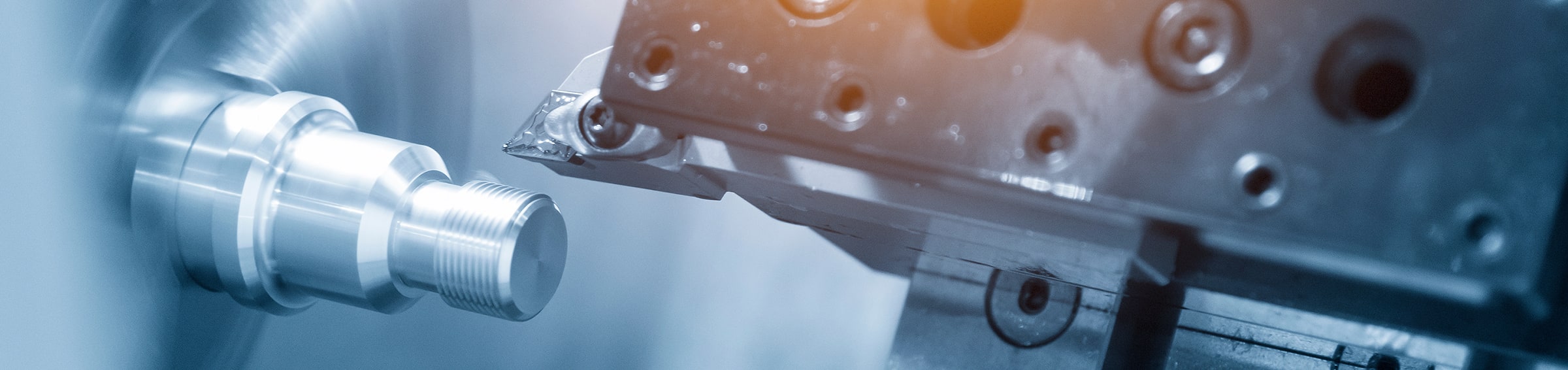
コラム column
六四黄銅の基本知識:C2800・C2801・C2802の特徴と用途
六四黄銅は、金属材料の中でも特に注目を浴びている合金の一つです。C2800、C2801、C2802という三つの異なるグレードが存在し、それぞれが特有の特徴と用途を持っています。あなたは「六四黄銅について知りたいけれど、どこから始めれば良いのかわからない」と悩んでいませんか?本記事では、そんな疑問にお答えし、六四黄銅の基本知識を詳しく解説します。
もしあなたが、六四黄銅の定義や、C2800、C2801、C2802の違い、さらにはそれぞれの用途について学びたいのであれば、この記事がぴったりです。例えば、C2800は高い加工性と耐食性を持ち、電気機器などに広く使用されています。一方でC2801は強度と耐腐食性に優れており、自動車部品や建築資材としても人気があります。C2802に至っては、その特性から水廻りの設備にも適した素材として知られています。
このように、それぞれのグレードには独自の利点があり、用途に応じて選択することが重要です。この記事を通じて、あなたも六四黄銅の全貌を理解し、実際の活用方法を見つける手助けができれば幸いです。さあ、一緒にこの魅力的な合金の世界を探ってみましょう!
1. 六四黄銅 C2800 C2801 C2802 とは
1-1. 六四黄銅の基本情報
六四黄銅とは、銅と亜鉛を主成分とする合金で、C2800、C2801、C2802の3つの種類があります。これらはそれぞれ少しずつ成分が異なり、特性や用途も変わります。例えば、C2800は耐食性が高く、主に配管やバルブに使われます。C2801は加工がしやすく、電気部品や機械部品に適しています。C2802は強度があり、建築用の部材に使われることが多いです。
このように、六四黄銅はさまざまな用途に応じて選ばれています。特に、耐久性や加工性が求められる場面で重宝されています。これらの特徴から、六四黄銅は多くの産業で重要な材料となっているのです。
1-2. 六四黄銅の成分と特性
六四黄銅は、銅と亜鉛からできた合金で、C2800、C2801、C2802という種類があります。これらは、銅が64%と亜鉛が36%の割合で混ざっており、特に耐腐食性や加工性に優れています。例えば、C2800は主に配管やバルブに使われ、C2801は電気部品に適しています。C2802は、装飾品や楽器にも利用されることがあります。これらの特性から、六四黄銅はさまざまな用途で重宝されています。六四黄銅はその優れた特性により、私たちの生活の中で重要な役割を果たしている金属の一つです。
2. 六四黄銅 C2800 C2801 C2802 の特徴
2-1. C2800の特徴
六四黄銅は、C2800、C2801、C2802という種類があります。これらは、銅と亜鉛を主成分とする合金で、特に耐食性や加工性に優れています。例えば、C2800は、優れた耐腐食性を持ち、主に配管やバルブに使われます。C2801は、電気伝導性が高く、電気部品に適しています。そしてC2802は、強度が高く、機械部品に使われることが多いです。これらの特徴から、六四黄銅はさまざまな産業で重宝されています。六四黄銅はその特性によって、幅広い用途があり、私たちの生活に欠かせない材料となっています。
2-2. C2801の特徴
六四黄銅は、C2800、C2801、C2802という3つの種類があります。これらは、銅と亜鉛の合金で、特に強度が高く、耐腐食性にも優れています。C2800は、主に配管やバルブに使われ、C2801は、電気部品や装飾品に適しています。C2802は、機械部品や工具に使われることが多いです。
これらの特徴から、六四黄銅はさまざまな用途で重宝されています。例えば、C2801は美しい光沢を持っているため、ジュエリーやインテリアに使われ、見た目を楽しむことができます。また、C2800は耐久性があるため、長く使える製品に適しています。
六四黄銅は、その特性から多様な分野で利用されており、非常に重要な素材です。
2-3. C2802の特徴
六四黄銅とは、銅と亜鉛の合金で、特にC2800、C2801、C2802という種類があります。これらは非常に強く、耐腐食性が高いため、様々な用途に使われています。例えば、C2800は電気機器の部品に使われ、C2801は水道管やバルブに適しています。そして、C2802は特に機械部品や装飾品に利用されます。これらの特徴から、六四黄銅は日常生活の中で重要な役割を果たしています。六四黄銅のC2800、C2801、C2802は、それぞれの特性を活かして、私たちの生活を支える様々な製品に使われているのです。
3. 六四黄銅 C2800 C2801 C2802 の用途
3-1. 一般的な用途
六四黄銅は、C2800、C2801、C2802という種類があり、それぞれに特徴と用途があります。まず、六四黄銅は銅と亜鉛の合金で、特に耐腐食性が高いです。このため、船舶や水道管など、水に触れる場所でよく使われます。例えば、C2800は加工がしやすく、部品や装飾品に適しています。一方、C2801は強度が高く、機械部品に利用されることが多いです。C2802は電気伝導性に優れており、電気機器に使われます。これらの特徴から、六四黄銅は多くの産業で重宝されています。六四黄銅はその特性により、さまざまな用途で活躍している重要な材料です。
3-2. 特殊な用途
六四黄銅は、C2800、C2801、C2802という種類があります。これらは特に耐食性が高く、加工もしやすい金属です。例えば、C2800は電気部品や配管に使われ、C2801は楽器や装飾品に適しています。C2802は、さらに強度が求められる場所で使われます。これらの特性から、六四黄銅はさまざまな用途で重宝されています。
なぜ六四黄銅が重要かというと、私たちの生活に密接に関わる製品に使われているからです。例えば、私たちが使う水道の配管や、楽器の音色もこの金属によって支えられています。これにより、私たちの生活はより便利で豊かになります。
六四黄銅はその特性から、私たちの日常生活に欠かせない素材なのです。
4. 六四黄銅 C2800 C2801 C2802 の加工方法
4-1. 加工技術の概要
六四黄銅は、C2800、C2801、C2802の3つの種類があります。これらは、銅と亜鉛を主成分とする合金で、特に耐腐食性に優れています。六四黄銅の特徴は、加工がしやすく、強度が高いことです。例えば、C2800は、主にパイプやバルブに使われ、C2801は、電気部品に適しています。C2802は、装飾品や楽器に利用されることが多いです。このように、用途が広く、さまざまな産業で重宝されています。六四黄銅は、その特性から多くの場面で活躍する重要な材料です。
4-2. 加工時の注意点
六四黄銅、つまりC2800、C2801、C2802は、特別な金属の一種です。これらは、主に銅と亜鉛からできていて、さまざまな特徴があります。まず、耐腐食性が高く、長持ちするため、屋外で使うものに最適です。例えば、船の部品や水道管などでよく使われています。
また、加工がしやすく、さまざまな形にすることができるため、工業製品にも多く使われています。たとえば、電気機器の部品や装飾品などです。これらの理由から、六四黄銅はとても人気があります。
六四黄銅はその特性から、さまざまな用途に使われる重要な金属です。これからも多くの場面で活躍するでしょう。
5. 六四黄銅 C2800 C2801 C2802 のメリット・デメリット
5-1. メリット
六四黄銅は、C2800、C2801、C2802という種類があり、それぞれに特徴と用途があります。まず、C2800は耐腐食性が高く、主に水道管や配管に使われます。次に、C2801は強度があり、機械部品や電気部品に適しています。C2802は加工がしやすく、装飾品や家具に利用されます。これらの特性から、六四黄銅はさまざまな分野で重宝されています。例えば、C2800の配管は水質を保つために重要で、C2801の部品は自動車などの安全性を高める役割を果たします。このように、六四黄銅は日常生活の中で欠かせない材料です。六四黄銅はその特性によって、私たちの生活を支える重要な役割を果たしています。
5-2. デメリット
六四黄銅は、C2800、C2801、C2802という種類があり、それぞれに特徴と用途があります。まず、C2800は優れた耐食性を持ち、主に配管やバルブに使われます。次に、C2801は加工がしやすく、電気部品や装飾品に適しています。C2802は強度が高く、機械部品や建築材料に使用されることが多いです。
これらの種類は、どれも金属の中でも特に人気があります。なぜなら、耐久性や加工のしやすさが求められる場面で活躍するからです。例えば、C2800の配管は水漏れを防ぎ、C2801の装飾品は美しさを引き立てます。
このように、六四黄銅は様々な分野で重要な役割を果たしており、これからも多くの用途が期待されています。
6. 銅合金の種類とその特性
6-1. 銅合金の基本
六四黄銅(C2800、C2801、C2802)は、銅と亜鉛を主成分とする合金です。この合金は、強度や耐腐食性に優れているため、さまざまな用途で使われています。例えば、C2800は主に配管やバルブに使われ、C2801は電気機器の部品として利用されます。また、C2802は装飾品やアクセサリーに適しています。これらの特性により、六四黄銅は多くの産業で重宝されています。さらに、加工がしやすく、さまざまな形に成形できるため、デザインの自由度も高いです。六四黄銅はその特徴から、建設や電気、デザインの分野で欠かせない材料となっています。
6-2. 他の銅合金との比較
六四黄銅(C2800、C2801、C2802)は、銅と亜鉛の合金で、特に強度と耐腐食性に優れています。この合金は、主に配管や機械部品、装飾品に使われます。例えば、C2800は強度が高く、バルブなどの重要な部品に適しています。一方、C2801は加工しやすく、細かい部品に使われることが多いです。C2802は、特に耐食性が必要な場所、例えば海水に接する部分に最適です。これらの合金は、様々な用途に応じて選ばれるため、非常に便利です。六四黄銅はその特性から多くの産業で重宝されており、私たちの生活を支える重要な素材です。
まとめ
六四黄銅は、主にC2800、C2801、C2802の3つのグレードに分類されます。C2800は優れた加工性を持ち、電気部品に適しています。C2801は耐食性が高く、建築や配管に使用されます。C2802は強度と耐摩耗性があり、機械部品に最適です。各グレードは用途に応じた特性を持ち、多様な産業で利用されています。
七三黄銅C2600とC2680の特性と用途を徹底解説
七三黄銅は、さまざまな産業で広く使用される合金であり、特にC2600とC2680という2つのグレードは、それぞれ異なる特性を持ちながらも多くの用途に対応しています。しかし、これらの合金の特性や利用方法について詳しく理解している人は意外と少ないのではないでしょうか。
「C2600とC2680の特性について知りたい」、「どのような用途に最適なのかを知りたい」と考えているあなたに向けて、このガイドを用意しました。この記事では、七三黄銅の基本的な特性から、それぞれの合金の特徴、さらには最適な使用例までを徹底的に解説します。
この情報を通じて、七三黄銅の重要性や利点を理解し、あなたのプロジェクトやビジネスにどのように活用できるかを見つけ出す手助けができれば幸いです。それでは、一緒に七三黄銅の世界を探っていきましょう。
1. 七三黄銅 C2600 C2680 の基本知識
1-1. 七三黄銅とは何か
七三黄銅は、銅と亜鉛を主成分とする合金で、特にC2600とC2680という種類があります。これらの合金は、特に耐腐食性に優れているため、さまざまな用途で使われています。例えば、C2600は水道管や配管部品に多く使われており、C2680は電子機器や自動車部品に利用されています。このように、七三黄銅は私たちの生活に欠かせない材料です。特に、耐久性が高く、加工がしやすいことから、工業製品に広く使われています。七三黄銅のC2600とC2680は、それぞれ異なる特性を持ち、様々な分野で役立っている重要な材料です。これからも、私たちの生活を支える役割を果たし続けるでしょう。
1-2. C2600 と C2680 の違い
七三黄銅のC2600とC2680は、どちらも金属の一種ですが、それぞれに特徴と使い道があります。まず、C2600は銅の含有量が高く、耐食性に優れています。そのため、配管やバルブなど、水に触れる部分に使われることが多いです。一方、C2680は、C2600よりも強度が高く、機械部品や電子機器の部品に適しています。例えば、C2680は自動車の部品や電気製品に使われることがあります。このように、C2600は主に水に関連する用途に、C2680は強度が求められる用途に使われます。C2600とC2680はそれぞれの特性を活かして、異なる分野で重要な役割を果たしています。
2. 七三黄銅 C2600 C2680 の特性
2-1. C2600 の特性
七三黄銅C2600は、特に強度が高く、耐腐食性に優れています。このため、C2600は多くの産業で使われています。例えば、電子機器の部品や、自動車の部品などです。これらの用途では、部品が壊れにくく、長持ちすることが求められます。また、C2600は加工がしやすく、さまざまな形にすることができるので、設計の自由度も高いです。
一方、C2680は、C2600よりもさらに耐食性が高く、特に海水に強い特性があります。このため、船舶や海洋機器の部品として使われることが多いです。C2680は、過酷な環境でも性能を発揮するため、信頼性が求められる場面で重宝されています。
このように、C2600とC2680はそれぞれ異なる特性を持ち、さまざまな用途で利用されています。
2-2. C2680 の特性
C2680は、七三黄銅の一種で、特に優れた特性を持っています。まず、C2680は耐腐食性が高く、湿気の多い場所でも長持ちします。このため、配管や水道の部品としてよく使われています。また、加工がしやすく、さまざまな形に成形できるため、工業製品にも広く利用されています。例えば、電子機器の部品や、楽器の材料としても人気があります。さらに、C2680は美しい金色の光沢があり、装飾品にも適しています。このように、C2680は多様な用途を持つため、工業や日常生活の中で非常に重要な素材です。C2680はその特性から多くの分野で活躍しており、私たちの生活を支える大切な材料と言えるでしょう。
3. 七三黄銅 C2600 C2680 の用途
3-1. C2600 の主な用途
C2600は、七三黄銅の一種で、さまざまな用途に使われています。まず、この素材は耐腐食性が高く、特に水回りの部品に適しています。例えば、蛇口や配管の部品などでよく見られます。また、C2600は加工がしやすく、細かい形状を作ることができるため、精密機器の部品にも利用されています。さらに、電気伝導性もあるため、電気機器の部品にも使われることがあります。これらの特性から、C2600は非常に多用途な素材として重宝されています。C2600はその優れた耐腐食性や加工性から、さまざまな分野で活躍している重要な素材です。
3-2. C2680 の主な用途
C2680は、七三黄銅の一種で、さまざまな用途に使われています。まず、C2680は耐腐食性が高く、加工がしやすい特徴があります。このため、配管やバルブなどの水回りの部品に多く使われています。具体的には、家庭や工場の水道管、または自動車の冷却系統などで見ることができます。
さらに、C2680は電気伝導性も良いため、電気機器の部品にも適しています。例えば、スイッチやコネクタなどの電子機器に使われ、安定した性能を発揮します。
C2680は耐腐食性や加工性、電気伝導性に優れた材料であり、さまざまな分野で重要な役割を果たしています。これらの特性のおかげで、多くの産業で重宝されているのです。
4. 七三黄銅 C2600 C2680 の成分と性質
4-1. C2600 の成分分析
C2600とC2680は、七三黄銅と呼ばれる金属の種類です。これらの合金は、銅と亜鉛が主な成分で、特にC2600は約70%の銅と30%の亜鉛からできています。これらの合金は、強度が高く、加工しやすいという特性があります。たとえば、C2600は配管やバルブ、C2680は電気部品や装飾品に使われます。これらの用途は、私たちの日常生活に欠かせないものです。例えば、あなたの家の水道管や、携帯電話の部品にも使われているかもしれません。C2600とC2680は、強度と加工性に優れた合金であり、さまざまな場面で私たちの生活を支えています。
4-2. C2680 の成分分析
七三黄銅C2600とC2680は、金属の中でも特に優れた特性を持っています。まず、C2600は耐食性が高く、加工がしやすいため、配管や電気部品に多く使われています。一方、C2680は強度があり、耐摩耗性にも優れているため、機械部品や工具に適しています。具体的には、C2600は水道管や冷却装置に使われ、C2680はギアやベアリングに利用されています。このように、用途によってそれぞれの特性を生かすことができるのです。C2600とC2680は、異なる特性によりさまざまな産業で重要な役割を果たしており、それぞれの用途に応じた使い方が求められています。
5. 七三黄銅 C2600 C2680 の加工方法
5-1. 真鍮加工の基本
七三黄銅C2600とC2680は、特に加工がしやすく、耐腐食性に優れた金属です。これらの特性から、様々な用途で利用されています。まず、C2600は主に配管や電気部品に使われます。これは、強度が高く、加工が簡単だからです。一方、C2680は、より高い耐食性が求められる場面で使われます。例えば、海水にさらされる船の部品などです。これらの金属は、どちらも日常生活に欠かせないアイテムに使われているため、私たちの生活を支えています。七三黄銅C2600とC2680は、それぞれの特性に応じた用途があり、私たちの生活に重要な役割を果たしています。
5-2. C2600 と C2680 の加工の違い
C2600とC2680は、七三黄銅の中でも特に人気のある材料です。これらの銅合金は、それぞれ異なる特性を持ち、さまざまな用途に使われています。まず、C2600は加工がしやすく、電気伝導性も高いため、電子機器の部品や配線に使われることが多いです。一方、C2680は耐腐食性が優れており、特に水に強いので、配管やバルブに適しています。このように、C2600は加工のしやすさから、C2680は耐久性の面で優れています。C2600とC2680はそれぞれの特性を活かして、異なる分野で重要な役割を果たしています。これにより、私たちの生活を支える多くの製品が作られているのです。
まとめ
七三黄銅C2600とC2680は、異なる銅合金で、それぞれ特性と用途が異なります。C2600は優れた加工性と耐食性を持ち、主に配管や電子部品に使用されます。一方、C2680は高強度で耐摩耗性に優れ、機械部品や精密部品に適しています。用途に応じた選択が重要です。
六四黄銅の熱伝導率とは?特性と応用について解説
「六四黄銅という言葉を聞いたことがありますか?その特性や用途について、詳しく知りたいと思いませんか?」というあなたの疑問に、今回はお答えします。
六四黄銅は、銅と亜鉛の合金であり、その特異な特性からさまざまな産業で使用されています。特に、熱伝導率はこの素材の性能において非常に重要なポイントです。しかし、具体的にどのような特性があり、どのような場面で生かされているのかを理解することは難しいかもしれません。
この記事では、六四黄銅の熱伝導率についての基本的な知識から、その応用例までを丁寧に解説していきます。特に、熱伝導率の数値が示す意味や、他の素材との比較を通じて、六四黄銅の持つ魅力を知る手助けをいたします。あなたがこの合金の特性を理解し、実際の使用に役立てるための情報を提供することを目的としています。無限の可能性を秘めた六四黄銅の世界に、一緒に足を踏み入れてみましょう。
1. 六四黄銅 熱伝導率の基本知識
1-1. 六四黄銅とは何か
六四黄銅は、銅と亜鉛を主成分とする合金です。この合金は、優れた熱伝導率を持っているため、さまざまな用途に使われています。特に、熱を素早く伝えることができるので、調理器具や冷却装置に適しています。例えば、鍋やフライパンは、六四黄銅で作られていることが多く、料理をより効率的に行うことができます。また、この合金は耐腐食性もあり、長持ちするため、様々な産業で重宝されています。
六四黄銅はその特性から多くの場面で利用されており、私たちの生活を便利にしています。この合金の特性を理解することで、より良い製品選びができるでしょう。
1-2. 六四黄銅の特性
六四黄銅は、特に熱伝導率が優れている金属です。熱伝導率が高いということは、熱を素早く伝えることができるという意味です。この特性により、六四黄銅はさまざまな用途に使われています。例えば、調理器具や電子機器の部品など、熱を効率よく伝えることが求められる場面で重宝されています。
さらに、六四黄銅は耐腐食性も持っているため、長期間使用しても劣化しにくいのが特徴です。これにより、屋外で使われる設備や水道管などにも利用されています。六四黄銅はその優れた熱伝導率と耐腐食性から、様々な分野で重要な役割を果たしている金属です。
1-3. 六四黄銅の熱伝導率の重要性
六四黄銅の熱伝導率は非常に重要です。まず、熱伝導率とは、物質が熱をどれだけ早く伝えるかを示す値です。六四黄銅は、銅と亜鉛の合金で、熱をよく伝える特性があります。この特性のおかげで、六四黄銅は電子機器や配管など、熱を効率的に管理する必要がある場所でよく使われています。
例えば、電子機器の内部で熱がこもると、故障の原因になります。六四黄銅を使うことで、熱を素早く外に逃がし、機器の寿命を延ばすことができます。また、配管に使うと、温水や冷水を効率よく運ぶことができます。
六四黄銅の熱伝導率は、私たちの生活に欠かせない役割を果たしており、多くの分野での応用が期待されています。
2. 六四黄銅 熱伝導率と他の材料の比較
2-1. 他の銅合金との熱伝導率比較
六四黄銅は、金属の一種で、とても熱を伝えやすい特性があります。この特性は、さまざまな用途に役立っています。まず、熱伝導率が高いということは、料理や暖房に使われる器具に最適です。たとえば、六四黄銅でできた鍋は、食材を均等に加熱できるため、美味しい料理を作るのに役立ちます。また、電子機器の部品としても使われ、熱をスムーズに逃がすことができるので、機器が壊れにくくなります。このように、六四黄銅の熱伝導率は非常に重要です。六四黄銅はその優れた熱伝導率のおかげで、料理や電子機器など、さまざまな分野で活躍しています。
2-2. 六四黄銅とアルミニウムの熱伝導率比較
六四黄銅は、熱をよく伝える特性があります。これは、金属の中でも特に熱伝導率が高いためです。熱伝導率が高いと、熱を素早く広げることができるので、調理器具や冷却装置に使われることが多いです。例えば、鍋やフライパンに使われることがあり、料理が均一に加熱されるのに役立ちます。また、六四黄銅は強度もあり、耐久性が高いので、長く使うことができます。このように、六四黄銅の熱伝導率の高さは、私たちの生活に便利さをもたらしています。六四黄銅は熱を効率よく伝えるため、様々な製品に利用されており、私たちの生活を支えています。
2-3. 六四黄銅の選定基準
六四黄銅は、銅と亜鉛の合金で、特に熱伝導率が高いのが特徴です。熱伝導率が高いということは、熱をよく伝えることを意味します。これが理由で、六四黄銅はさまざまな産業で使われています。例えば、電子機器や熱交換器、さらには配管などの部品に利用されることが多いです。具体的には、冷却装置の部品に使われることで、効率的に熱を逃がす役割を果たします。このように、六四黄銅は高い熱伝導率を持つため、熱をうまく管理するための重要な材料です。六四黄銅はその特性から、多くの分野で欠かせない存在となっています。
3. 六四黄銅 熱伝導率を考慮した加工方法
3-1. 六四黄銅の加工技術
六四黄銅は、銅と亜鉛の合金で、熱をよく通す特性があります。これは、私たちの生活にとても役立っています。まず、熱伝導率が高いので、鍋やフライパンなどの調理器具に使われます。料理をするとき、熱が均一に伝わることで、食材が美味しく仕上がります。また、六四黄銅は耐腐食性もあるため、長持ちします。さらに、電気を通す性質もあるため、電子機器の部品にも使われています。これらの特性から、六四黄銅は多くの分野で重宝されています。六四黄銅の熱伝導率は、私たちの生活を便利にし、様々な製品に活かされている大切な特性です。
3-2. 加工時の熱伝導率の影響
六四黄銅の熱伝導率は、材料の特性としてとても重要です。熱伝導率が高いと、熱をすばやく伝えることができるため、さまざまな用途に適しています。例えば、六四黄銅は電子機器や配管などに使われており、冷却システムにも役立っています。この材料は、熱を効率よく伝えることで、機器の性能を向上させることができます。さらに、六四黄銅は耐腐食性もあり、長持ちするため、多くの産業で重宝されています。六四黄銅の熱伝導率の高さは、その特性や応用において非常に重要であり、私たちの生活を支える材料の一つと言えるでしょう。
3-3. 加工後の特性評価
六四黄銅は、銅と亜鉛の合金で、特に熱伝導率が高いことで知られています。熱伝導率が高いということは、熱をよく伝えることができるという意味です。これが理由で、六四黄銅は多くの場面で使われています。例えば、調理器具や冷却装置に利用されることが多いです。調理器具では、食材を均一に加熱するために役立ちます。また、冷却装置では、熱を効率よく逃がすことができるため、機械を守るために重要です。六四黄銅の高い熱伝導率は、私たちの生活を便利にするために多くの製品に活かされています。この特性のおかげで、私たちはより良い生活を送ることができるのです。
4. 六四黄銅 熱伝導率と工業製品の関係
4-1. 工業製品における六四黄銅の役割
六四黄銅は、銅と亜鉛の合金で、特に熱伝導率が高い特性を持っています。この特性は、工業製品において非常に重要です。まず、熱伝導率が高いことで、熱を素早く伝えることができるため、冷却装置や熱交換器に使われます。例えば、自動車のラジエーターやエアコンの部品には六四黄銅が使われており、効率的に熱を管理しています。
さらに、六四黄銅は耐腐食性もあり、長持ちするため、様々な環境で安心して使用できます。このように、六四黄銅は工業製品において重要な役割を果たしており、私たちの生活を支えています。六四黄銅の熱伝導率の高さと耐久性は、工業製品に欠かせない特性であると言えます。
4-2. 六四黄銅の熱伝導率がもたらす利点
六四黄銅は、銅と亜鉛の合金で、特に熱伝導率が高いという特性があります。この特性のおかげで、六四黄銅は多くの場面で役立ちます。まず、熱伝導率が高いということは、熱を素早く伝えることができるということです。例えば、調理器具や冷却装置に使われることが多いです。鍋やフライパンに使うと、食材を均一に加熱でき、美味しく料理ができます。また、冷却装置に使うと、効率よく熱を逃がすことができるため、機械が長持ちします。このように、六四黄銅の熱伝導率は、私たちの生活に便利さをもたらしています。これからも、さまざまな分野で活躍が期待される材料です。
4-3. 六四黄銅の用途例
六四黄銅は、特に優れた熱伝導率を持つ金属です。この特性のおかげで、さまざまな用途に使われています。まず、熱伝導率が高いということは、熱をすぐに伝えることができるということです。これにより、六四黄銅は調理器具や冷却装置に利用されます。たとえば、鍋やフライパンの素材として使われ、食材を均一に加熱するのに役立っています。また、電子機器の部品にも使われ、熱を効率よく逃がすことで機器の故障を防ぎます。このように、六四黄銅は私たちの生活に欠かせない素材です。六四黄銅の優れた熱伝導率は、さまざまな分野での活用を可能にし、私たちの生活を便利にしています。
5. 六四黄銅 熱伝導率を理解するための基礎知識
5-1. 銅合金の種類と特徴
六四黄銅は、銅と亜鉛の合金で、特に熱伝導率が高いという特性があります。これは、金属が熱を効率よく伝えることができるため、さまざまな用途に使われます。例えば、六四黄銅は冷却装置や熱交換器に使われ、熱を素早く移動させることで、機械の性能を向上させます。この特性のおかげで、工業や家庭での使用が広がっています。さらに、耐腐食性も高いため、長持ちするという利点もあります。六四黄銅はその優れた熱伝導率と耐久性から、さまざまな分野で重要な役割を果たしているのです。
5-2. 六四黄銅の歴史と発展
六四黄銅は、銅と亜鉛の合金で、特に熱伝導率が優れています。これは、熱を素早く伝えることができるため、さまざまな用途に役立ちます。例えば、六四黄銅は調理器具や冷却装置に使われています。これらの製品では、熱を均一に分散させることが大切です。
なぜ六四黄銅が注目されるのかというと、その特性が他の金属よりも優れているからです。熱をすぐに伝えることができるため、効率的にエネルギーを使用できます。たとえば、鍋を使うとき、六四黄銅の鍋はすぐに熱くなり、食材を短時間で調理できます。
六四黄銅はその優れた熱伝導率から、さまざまな分野で重要な役割を果たしています。これからも多くの場所で利用されるでしょう。
5-3. 銅の重要性とその影響
六四黄銅は、銅と亜鉛の合金で、特に熱伝導率が高いことが特徴です。熱伝導率が高いということは、熱を素早く伝えることができるという意味です。例えば、六四黄銅で作られた鍋は、火にかけるとすぐに温まるので、料理が早くできます。この特性から、六四黄銅は電子機器や配管など、さまざまな分野で使われています。
また、六四黄銅は耐腐食性もあり、長持ちするため、特に水回りの設備に適しています。これらの理由から、六四黄銅は私たちの生活に欠かせない材料の一つです。六四黄銅の熱伝導率の高さと耐久性は、さまざまな用途において非常に重要な役割を果たしています。
まとめ
六四黄銅は、銅と亜鉛の合金で、優れた熱伝導率を持ち、約120 W/m·Kです。この特性により、冷却装置や熱交換器などの応用が広がります。また、耐腐食性や加工性にも優れており、電子機器や配管など多岐にわたる産業で利用されています。
七三黄銅C2600とC2680の熱伝導率を徹底解説!
七三黄銅、特にC2600とC2680は、その優れた物理的特性から多くの産業で使用されていますが、特に熱伝導率に関しては、理解を深めることが非常に重要です。「七三黄銅の熱伝導率についてもっと知りたいが、具体的に何を調べればいいのか分からない…」そんなあなたのために、今回はこの二つの合金の熱伝導率を徹底的に解説します。
この記事では、七三黄銅C2600とC2680の特徴や違い、そしてそれぞれの熱伝導率について詳しく触れていきます。これから金属材料を選定する際に役立つ情報が満載です。「熱伝導率とは何か?」、「どうしてそれが重要なのか?」という疑問を抱える方にも分かりやすくお伝えしますので、ぜひご覧ください。
産業界でも注目されるこの分野の知識を深めることで、具体的な選定基準や応用方法が見えてくるでしょう。七三黄銅の特性に対する理解を深め、新たな可能性を見つける手助けをするために、ぜひこの記事を参考にしてください。
1. 七三黄銅 C2600 C2680 の特性と違い
1-1. C2600の基本特性
七三黄銅のC2600とC2680は、熱伝導率が高い金属です。まず、熱伝導率とは、熱が金属を通ってどれくらい早く移動するかを示す数値です。C2600は、特に熱をよく伝える性質を持っていて、例えば、熱いお湯をすぐに冷やすことができます。一方、C2680も熱伝導率が高いですが、C2600より少し劣ります。しかし、どちらも電子機器や配管など、さまざまな用途で使われています。
これらの特性から、C2600は冷却装置や熱交換器に最適です。C2680は、耐食性が高く、特に水回りでの使用に向いています。このように、C2600とC2680は、それぞれ異なる場面で役立つ金属です。どちらも熱を効率よく伝える能力があり、私たちの生活に役立っています。
1-2. C2680の基本特性
C2680は、七三黄銅の一種で、特に熱伝導率が高いことで知られています。熱伝導率が高いということは、熱をよく伝えることができるという意味です。これにより、C2680は多くの産業で利用されています。例えば、電子機器や冷却装置など、熱を効率的に管理する必要がある場所で使われます。
C2680の熱伝導率は、C2600よりも優れており、より効率的に熱を伝えることができます。これが理由で、C2680は高性能な製品に好まれています。
C2680はその優れた熱伝導率から、多くの分野で重要な材料となっています。これにより、より良い製品を作る手助けをしているのです。
1-3. C2600とC2680の比較
七三黄銅のC2600とC2680は、どちらも熱伝導率が高い金属です。C2600の方がC2680よりも熱をよく伝えることができます。理由は、C2600は銅の含有量が多く、純度が高いためです。具体的には、C2600は約70%の銅を含んでおり、熱を素早く伝える性質があります。一方、C2680は少し合金が加わっているため、熱伝導率がC2600よりも低くなります。このため、C2600は熱交換器や調理器具など、熱を効率的に伝える必要がある場所でよく使われます。熱伝導率を重視する場合はC2600を選ぶと良いでしょう。
2. 七三黄銅 C2600 C2680 の加工方法と基礎知識
2-1. 黄銅の加工技術
七三黄銅のC2600とC2680は、どちらも熱をよく伝える特性があります。C2600の熱伝導率が高いため、特に熱交換器や配管に適しています。理由は、C2600は銅の含有量が多く、熱を効率的に伝えるからです。具体的な例として、C2600は冷暖房システムや自動車の部品に使われることが多いです。一方、C2680はC2600よりも少し熱伝導率が低いですが、耐腐食性が高いので、屋外での使用に向いています。例えば、C2680は外部のパイプや装飾品に利用されます。用途によってC2600とC2680を使い分けることで、効率的な熱管理が可能になります。
2-2. 加工時の注意点
七三黄銅C2600とC2680は、金属の一種で、特に熱をよく通す性質があります。これらの合金は、熱伝導率が高いため、様々な用途で使われています。例えば、C2600は電子機器や冷却装置に使われることが多く、C2680は配管や熱交換器に適しています。これらの金属は、熱を効率よく伝えるため、エネルギーの無駄を減らし、効率的な運用が可能です。したがって、C2600とC2680は、特に工業や製造業で重要な役割を果たしています。七三黄銅のC2600とC2680は、高い熱伝導率を持ち、様々な分野で利用されるため、非常に価値のある材料です。
2-3. 加工に適した工具と機械
七三黄銅C2600とC2680は、金属の中でも特に熱をよく通す性質があります。まず、これらの材料は熱伝導率が高いため、さまざまな用途に適しています。理由は、熱を効率よく伝えることで、エネルギーを節約できるからです。たとえば、C2600は冷却装置や熱交換器に使われ、C2680は電子機器の部品に利用されます。これらの材料を使うことで、製品の性能が向上し、エネルギーコストも削減できます。七三黄銅C2600とC2680は、熱をよく通す特性があるため、さまざまな産業で重宝されていることがわかります。このように、熱伝導率の高さが、これらの金属の重要な特徴です。
3. 七三黄銅 C2680 の用途、強度、耐食性
3-1. C2680の主な用途
C2680は、主に配管や電気機器の部品として使われる特別な金属です。この金属は、熱をよく伝える性質があり、さまざまな場面で役立っています。たとえば、C2680は暖房システムや冷却装置に使われており、効率よく熱を移動させることができます。これにより、エネルギーを節約でき、電気代を抑えることが可能です。また、C2680は耐腐食性も高いため、長期間にわたって使用できるのも大きな特徴です。このように、C2680は熱伝導率が高く、さまざまな用途に適しているため、多くの人にとって重要な材料となっています。C2680はその特性から、多くの産業で必要とされる金属です。
3-2. C2680の強度特性
C2600とC2680は、七三黄銅と呼ばれる金属の種類です。これらの金属は、熱をよく伝える特性があり、さまざまな用途で使われています。まず、C2600は、熱伝導率が高く、電子機器や配管などに使われることが多いです。次に、C2680は、C2600よりも強度が高く、耐久性が必要な場所で使われることが多いです。
例えば、C2600は冷却システムに使われ、C2680は自動車部品に利用されることがあります。これらの金属は、熱を効率よく伝えるため、エネルギーの節約にもつながります。C2600とC2680は、それぞれの特性を活かして、私たちの生活を支える重要な材料です。
3-3. C2680の耐食性について
C2680は、耐食性が高い特性を持っています。これは、C2680が含む銅と亜鉛の割合が良好であるためです。耐食性が高いと、金属が水や空気にさらされても、錆びたり劣化したりしにくくなります。例えば、海の近くにある建物や設備では、塩分が多いために金属が腐食しやすいですが、C2680を使うことで長持ちさせることができます。このように、C2680は厳しい環境でも安心して使える材料です。C2680は耐食性が高く、特に海や湿気の多い場所での使用に適しているため、建設や製造において非常に重要な素材と言えます。
4. 七三黄銅 C2600 C2680 の熱伝導率
4-1. C2600の熱伝導率
C2600は、七三黄銅の一種で、熱伝導率が非常に高い材料です。熱伝導率が高いということは、熱をすばやく伝えることができるという意味です。例えば、鍋やフライパンに使われることが多く、料理をするときに熱が均一に伝わるので、食材が美味しく仕上がります。この特性により、C2600は家庭や業務用の調理器具に最適です。
また、C2600は耐久性もあり、長持ちするため、コストパフォーマンスが良いのも魅力の一つです。たとえば、長い間使っても劣化しにくいので、買い替えの必要が少なくなります。以上の理由から、C2600は熱を効率よく伝えるための優れた選択肢と言えるでしょう。
4-2. C2680の熱伝導率
C2680は、七三黄銅の一種であり、その熱伝導率は非常に高いです。熱伝導率が高いということは、熱を効率よく伝えることができるということです。これにより、C2680はさまざまな産業で利用されています。例えば、電子機器や冷却装置に使われることが多いです。これらの機器では、熱を素早く逃がすことが求められるため、C2680の特性が役立ちます。さらに、C2680は耐腐食性にも優れているため、長期間にわたって安定して使用できます。このように、C2680の熱伝導率の高さは、実用性を高める重要な要素です。C2680は熱を効率よく伝えることで、さまざまな分野での活用が期待されている材料です。
4-3. 熱伝導率の重要性
七三黄銅C2600とC2680は、熱伝導率がとても重要な金属です。熱伝導率が高いと、熱が速く伝わるので、さまざまな用途に使われます。例えば、C2600は、電子機器の部品や冷却装置に使われ、効率よく熱を逃がします。一方、C2680は、より耐食性が高く、屋外での使用に適しています。これらの特性から、どちらの合金も工業界で重宝されています。熱伝導率が高いことは、製品の性能を向上させるために欠かせません。C2600とC2680の熱伝導率は、それぞれの用途に応じた選択を可能にし、私たちの生活をより快適にしてくれるのです。
5. 金属加工における七三黄銅 C2600 C2680 の選択基準
5-1. 選択基準のポイント
七三黄銅のC2600とC2680は、どちらも金属の一種ですが、熱伝導率が異なります。C2600はC2680よりも熱をよく伝えることができます。これは、C2600が銅の割合が高く、熱を伝える力が強いからです。
その理由は、銅が熱を通しやすい特性を持っているからです。例えば、C2600は電子機器の部品や熱交換器に使われることが多いです。これに対し、C2680は熱伝導率が低いため、主に装飾品や耐食性が求められる場所で使われます。
このように、C2600は効率的に熱を伝えるため、特に熱を必要とする用途に適しています。結局、用途によってどちらの合金を選ぶかが重要です。
5-2. 使用目的に応じた選択
七三黄銅C2600とC2680は、金属の中でも特に熱をよく通す性質があります。熱伝導率が高いということは、熱を効率的に伝えることができるということです。これが重要な理由は、例えば、調理器具や冷却装置など、熱を使う製品には最適だからです。
具体的な例として、C2600は主に配管や電気接続部品に使われています。これは、熱をすぐに伝えることで、効率的にエネルギーを使えるからです。一方、C2680は、より高温に耐えられるため、特殊な機械部品に使われます。
このように、七三黄銅の種類によって用途が異なるため、選ぶ際にはそれぞれの特性を理解することが大切です。正しい選択をすることで、より良い結果を得られるでしょう。
5-3. コストと性能のバランス
七三黄銅のC2600とC2680は、熱伝導率が異なる金属です。結論から言うと、C2600の方がC2680よりも熱をよく伝えます。この理由は、C2600がより多くの銅を含んでいるためです。銅は熱を伝える力が強いので、C2600は熱交換器や電子機器に使われることが多いです。
具体的な例として、C2600は冷却装置や調理器具に使われることが多いです。一方、C2680は耐久性が高く、主に建築やインフラに使われています。このように、用途によって使う材料が変わります。
まとめると、熱をよく伝えるC2600は特に熱を扱う製品に適しており、C2680は丈夫さが求められる場面で活躍します。選ぶ際は、どちらの特性が必要かを考えることが大切です。
まとめ
七三黄銅C2600とC2680は、異なる成分比を持つ銅合金で、それぞれ特有の特性があります。C2600は優れた熱伝導率を持ち、加工性も高く、電子機器や配管に多く使用されます。一方、C2680は耐食性に優れ、特に化学工業での利用が一般的です。両者の熱伝導率を理解することで、適切な用途選定が可能になります。
丹銅のヤング率とは?基本概念と特性を解説
丹銅とは、その美しい色合いと優れた耐食性から古くから多くの工業やアートの分野で用いられている合金です。しかし、この素材の力学的特性を理解することは、丹銅を効果的に利用するために欠かせません。特に「ヤング率」という指標は、丹銅の弾性を評価する上で非常に重要です。
「丹銅のヤング率って何?」「どのように測定されるのか?」といった疑問を抱いている方も多いでしょう。この記事では、丹銅のヤング率の基本概念からその特性、そして実際の応用例までを詳しく解説します。丹銅の特性を深く理解することで、あなたのプロジェクトや製品に役立つ情報を得ることができるでしょう。さあ、丹銅の魅力とその物理的特性について、一緒に学んでいきましょう!
1. 丹銅 ヤング率の基本知識
1-1. 丹銅とは何か
丹銅とは、銅に少量の他の金属を加えた合金のことです。特に、丹銅は耐久性が高く、加工がしやすいため、さまざまな製品に使われています。例えば、楽器や電気機器、さらには装飾品などに利用されており、私たちの生活に欠かせない材料です。このように、丹銅は私たちの身近なところで役立っています。
さらに、丹銅の特性の一つに「ヤング率」があります。ヤング率は、材料がどれだけ伸びたり縮んだりするかを示す指標です。丹銅は高いヤング率を持っているため、強い力が加わっても形を保ちやすいのです。この特性があるおかげで、丹銅は信頼性のある素材として広く使われています。要するに、丹銅は私たちの生活に重要な役割を果たしているのです。
1-2. 丹銅の特性と用途
丹銅は、銅とスズの合金で、とても強くて丈夫な金属です。まず、丹銅の特性として、耐腐食性が高いことが挙げられます。これは、湿気や水に強く、長い間使っても劣化しにくいということです。例えば、船や水道管など、水に触れる場所でよく使われています。次に、丹銅は加工がしやすく、さまざまな形にすることができます。このため、楽器や装飾品などにも利用されています。丹銅は美しい色合いを持っているため、見た目にも魅力的です。これらの特性から、丹銅は多くの分野で重宝されています。丹銅はその強さと美しさから、私たちの生活に欠かせない素材の一つと言えるでしょう。
2. 丹銅 ヤング率と弾性係数の関係
2-1. ヤング率とは
ヤング率とは、物質がどれだけ伸びたり縮んだりするかを示す大切な数値です。ヤング率は物質の硬さや弾力性を理解するのに役立ちます。理由は、ヤング率が高いほど、その物質は変形しにくく、逆に低いと柔らかいということです。例えば、金属の銅はヤング率が高く、硬くてしっかりしていますが、ゴムはヤング率が低くて柔らかく、簡単に伸びます。このように、ヤング率を知ることで、私たちは異なる素材の性質を理解し、適切に使うことができます。ヤング率は物質の性質を知るための重要な指標であり、私たちの生活に役立つ情報を提供してくれます。
2-2. ポアソン比との関連性
丹銅のヤング率は、金属の硬さや弾力性を示す大切な指標です。ヤング率が高いと、その金属は力を加えても元の形に戻りやすいことを意味します。例えば、丹銅は非常に高いヤング率を持っているため、強い力がかかっても変形しにくいのです。この特性は、電気機器や楽器など、さまざまな製品に利用されています。特に、丹銅は音の響きを良くするため、楽器の材料として人気があります。つまり、丹銅のヤング率は、金属の特性を理解する上で重要な情報です。このように、丹銅の特性を知ることで、私たちはより良い製品を作る手助けができるのです。
3. C2700材質の特性と物性
3-1. C2700の化学成分
丹銅のヤング率は、金属の硬さや弾力性を示す大切な指標です。丹銅は非常に優れた特性を持っており、特に電子機器や楽器などに使われています。理由として、ヤング率が高いほど、材料は変形しにくく、力を加えても元の形に戻りやすいからです。具体的な例として、丹銅は楽器の弦や配線に使われ、音質や耐久性を向上させます。また、電子機器では、部品が壊れにくくなるため、長持ちします。これらの特性から、丹銅は多くの分野で重宝されています。丹銅のヤング率は、その優れた特性により、私たちの生活に欠かせない材料であることがわかります。
3-2. C2700の機械的特性
丹銅のヤング率は、金属の硬さや弾力性を示す大切な値です。ヤング率が高いほど、金属は引っ張られたときに変形しにくくなります。例えば、丹銅はヤング率が高いため、強い力を加えても元の形に戻りやすいです。この特性は、電気配線や装飾品など、さまざまな製品に使われています。さらに、丹銅は耐腐食性にも優れているため、長持ちします。これらの理由から、丹銅は多くの産業で重宝されています。丹銅のヤング率は、その特性を理解する上で非常に重要であり、私たちの生活に役立つ材料であることがわかります。
4. 銅合金の種類と特徴比較
4-1. 丹銅と黄銅の違い
丹銅(たんどう)と黄銅(おうどう)は、金属の種類で、それぞれ特性が異なります。まず、丹銅は銅に少しの他の金属(主にスズ)を混ぜたもので、非常に強く、耐久性があります。例えば、楽器や工芸品に使われることが多いです。一方、黄銅は銅と亜鉛を混ぜたもので、明るい金色をしており、加工がしやすいです。これにより、装飾品や配管に使われます。
このように、丹銅と黄銅は異なる用途や特性を持っています。丹銅は強さが求められる場面で、黄銅は見た目や加工のしやすさが重視される場面で使われます。だから、どちらの金属もそれぞれの良さがあり、用途に応じて選ばれています。
4-2. 他の銅合金との比較
丹銅のヤング率は、金属の硬さや弾力性を示す重要な指標です。結論から言うと、丹銅は非常に優れた特性を持っています。理由は、丹銅が銅とスズの合金であり、強度が高く、加工しやすいからです。例えば、丹銅は楽器や精密機器に使われており、その優れた弾性によって音質を保つことができます。また、丹銅は耐腐食性にも優れているため、屋外での使用にも適しています。このように、丹銅のヤング率はその特性を理解する上で重要であり、様々な分野での利用を支えています。つまり、丹銅はその特性から多くの場面で重宝されている金属なのです。
5. 丹銅 ヤング率の実験結果の検証
5-1. 実験方法の概要
丹銅のヤング率は、材料の硬さや弾力性を示す重要な指標です。丹銅のヤング率は、金属の特性を理解するために必要です。理由として、ヤング率は材料がどれだけ伸びたり縮んだりするかを教えてくれるからです。例えば、丹銅は電気をよく通し、加工もしやすいので、電気製品や楽器に使われます。具体的に言うと、丹銅で作られた楽器は、音をよく響かせる特性があります。このように、丹銅のヤング率を知ることで、私たちはその特性を活かした製品を作ることができます。丹銅のヤング率を理解することは、科学や技術の進歩に貢献する大切なステップです。
5-2. 結果の考察
丹銅のヤング率について考えてみましょう。丹銅は非常に優れた材料であり、そのヤング率は特に重要です。ヤング率とは、材料がどれだけ伸びたり縮んだりするかを示す数値です。例えば、丹銅は電気をよく通し、柔らかさと強さを兼ね備えているため、電気部品や楽器に使われます。この特性により、丹銅はさまざまな分野で重宝されています。具体的には、電気配線や精密機器の部品として使われているのです。丹銅のヤング率はその使い道に大きく影響し、私たちの生活に欠かせない材料の一つであることがわかります。
まとめ
丹銅のヤング率は、丹銅(銅とスズの合金)の弾性特性を示す指標で、材料が力を受けた際の変形の度合いを表します。一般的に、ヤング率が高いほど材料は硬く、変形しにくい特性を持ちます。丹銅は耐食性や加工性に優れ、電気伝導性も高いため、電子機器や建材に広く利用されています。
丹銅と真鍮の違いを徹底解説!用途や特徴を知ろう
「丹銅と真鍮の違いを徹底解説!用途や特徴を知ろう。」というタイトルを目にしたあなたは、金属材の選び方において重要な情報を求めているかもしれません。「丹銅と真鍮って何が違うの?どう使い分ければいいの?」と疑問に思っている方も多いでしょう。
このガイドでは、まず丹銅と真鍮の基本的な違いを明らかにし、それぞれの特性や用途について詳しく解説していきます。日常生活における金属の選択は、見た目や耐久性、さらには価格にも大きく影響を与えます。特に、ものづくりやDIYを楽しむ方々にとって、適切な素材選びは作品のクオリティを左右する重要な要素です。
知識が深まれば、あなたのプロジェクトに最適な金属を選ぶ力が身に付きます。この機会に、丹銅と真鍮の特徴を理解し、用途に応じて賢く使い分ける方法を学びましょう。さあ、一緒に金属の世界を探求してみませんか?
1. 真鍮の種類や特徴について
1-1. 真鍮の基本的な定義
丹銅と真鍮は、どちらも金属ですが、性質や用途が異なります。まず、丹銅は主に銅でできており、耐腐食性が高く、電気をよく通します。例えば、電線や楽器に使われています。一方、真鍮は銅と亜鉛の合金で、金色の光沢があります。真鍮は装飾品や家具の金具に使われることが多いです。
このように、丹銅は主に電気関連で使われ、真鍮は見た目を重視した用途に向いています。両者の違いを理解することで、どちらの金属がどのような場面で使われるかがわかります。丹銅と真鍮はそれぞれ異なる特性を持ち、異なる目的で利用されています。これを知ることで、金属の選び方がより明確になります。
1-2. 真鍮の成分とその特性
丹銅と真鍮は、どちらも金属ですが、それぞれに違いがあります。まず、丹銅は主に銅からできていて、赤みを帯びた色をしています。一方、真鍮は銅と亜鉛の合金で、黄色や金色に見えます。この違いが、用途にも影響します。
例えば、丹銅は電気をよく通すため、電気機器や配線に使われます。逆に、真鍮は耐腐食性が高く、装飾品や楽器に使われることが多いです。また、真鍮は加工がしやすいので、様々な形に作ることができます。
丹銅と真鍮は成分や色、用途が異なります。これを知ることで、どちらの金属がどのように使われるのか理解できるでしょう。
1-3. 丹銅と真鍮の違いに関する基礎知識
丹銅と真鍮は、どちらも金属ですが、それぞれ異なる特徴があります。まず、丹銅は主に銅でできていて、赤みを帯びた色合いが特徴です。真鍮は銅と亜鉛の合金で、金色のような光沢があります。これらの違いから、使われる場所や目的も異なります。
例えば、丹銅は楽器や美術品に多く使われています。これは、音が良く響くからです。一方、真鍮はドアノブや楽器の部品に使われることが多いです。これは、耐久性があり、見た目も美しいからです。
丹銅と真鍮は色や用途が違い、それぞれの特性を生かして様々な場面で使われています。これを知ることで、金属の選び方がより分かりやすくなります。
2. 真鍮と銅の違いを理解したい
2-1. 丹銅と真鍮の成分の違い
丹銅と真鍮は、金属の種類として異なる特徴を持っています。まず、丹銅は主に銅でできており、真鍮は銅と亜鉛の合金です。理由として、丹銅は高い導電性を持ち、電気や熱をよく通します。一方、真鍮は加工がしやすく、見た目も美しいため装飾品や楽器に使われます。
具体例として、丹銅は電線や配電盤に使われることが多いです。真鍮はドアノブや楽器の部品に使われることがあります。これらの用途は、それぞれの金属の特性に基づいています。
丹銅と真鍮は異なる成分を持ち、それぞれ特有の用途があります。これを理解することで、金属の選び方がより明確になります。
2-2. 性能面での違い
丹銅と真鍮は、どちらも金属ですが、それぞれに違いがあります。まず、丹銅は銅が主成分で、特に強度が高く、耐腐食性にも優れています。このため、楽器や電気製品の部品などに使われます。一方、真鍮は銅と亜鉛の合金で、金色の見た目が特徴です。真鍮は加工がしやすく、装飾品や家具の金具に多く使われています。
例えば、楽器のトランペットは丹銅で作られることが多いですが、ドアノブや装飾的なアイテムには真鍮が使われます。このように、丹銅と真鍮はそれぞれの特性を活かして異なる用途に利用されています。金属を選ぶ際は、目的に応じた特性を理解することが大切です。
2-3. 見た目の違いとその影響
丹銅と真鍮には大きな違いがあります。まず、丹銅は銅を主成分とした金属で、赤茶色の見た目をしています。一方、真鍮は銅と亜鉛を混ぜた金属で、金色に近い色をしています。この違いは、見た目だけでなく、使い方にも影響を与えます。
例えば、丹銅は音楽の楽器や配管に使われることが多いです。これは、丹銅が音をよく響かせる特性があるからです。反対に、真鍮は装飾品や硬貨などに使われます。真鍮は見た目が美しく、耐久性もあるためです。
このように、丹銅と真鍮は見た目や用途が異なります。それぞれの特性を理解することで、どちらの金属を使うべきかを選ぶことができます。
3. 真鍮のデメリットや注意点を把握したい
3-1. 真鍮の耐久性とその限界
真鍮と丹銅は、どちらも金属ですが、いくつかの違いがあります。まず、真鍮は主に銅と亜鉛から作られ、丹銅は銅と少量の他の金属から作られています。理由として、真鍮は耐久性が高く、腐食に強いので、楽器や配管などに使われます。具体例として、トランペットや蛇口などがあります。一方、丹銅は柔らかく、加工しやすいため、細かい装飾品や美術品に使われることが多いです。たとえば、仏像や工芸品などがその例です。このように、真鍮と丹銅は用途や特徴が異なるため、使う場面によって選ぶことが大切です。どちらの金属もそれぞれの良さがあり、私たちの生活に役立っています。
3-2. 環境への影響と注意点
丹銅と真鍮は、どちらも金属ですが、性質や使い道が違います。まず、丹銅は銅に少しの他の金属を混ぜたもので、主に耐久性が高く、電気をよく通す特性があります。これに対して真鍮は、銅と亜鉛を混ぜた金属で、金色に輝く美しさが特徴です。真鍮は装飾品や楽器に使われることが多いです。
具体的な例として、丹銅は電気配線や配管に使われ、真鍮はドアノブや楽器に使われます。このように、丹銅と真鍮はそれぞれ異なる用途があり、使う場所によって選ばれます。
丹銅と真鍮の違いを知ることで、どちらの金属をどのように使うかを理解できるようになります。金属の特性を知ることは、とても大切です。
3-3. メンテナンスの必要性
丹銅と真鍮は、金属の種類であり、それぞれ異なる特徴を持っています。まず、丹銅は銅と少量の他の金属を混ぜたもので、主に耐久性や美しさが求められる製品に使われます。例えば、楽器や装飾品に使われることが多いです。一方、真鍮は銅と亜鉛を混ぜた合金で、加工がしやすく、錆びにくい特性があります。そのため、真鍮はドアノブや楽器、配管など、幅広い用途で利用されています。丹銅と真鍮はそれぞれ異なる特性を持ち、使われる場面が違います。どちらの金属も、私たちの生活に欠かせない大切な材料です。
4. 真鍮の用途や適切な使い方を知りたい
4-1. 真鍮の一般的な用途
真鍮は、金属の一種で、主に銅と亜鉛から作られています。真鍮の特徴は、金色の輝きと優れた加工性です。これにより、さまざまな用途で使われています。例えば、楽器や装飾品、配管部品などが挙げられます。楽器では、トランペットやサックスフォンなどが真鍮で作られ、その美しい音色が魅力です。また、装飾品では、真鍮の輝きがインテリアを引き立てます。
真鍮は耐腐食性もあり、長持ちするため、実用的なアイテムにも多く使われています。このように、真鍮は美しさと実用性を兼ね備えた金属として、多くの場面で活躍しています。真鍮の特性を理解することで、私たちはその魅力をより深く知ることができるでしょう。
4-2. 丹銅と真鍮の適切な使い方
丹銅と真鍮は、どちらも金属ですが、それぞれ異なる特徴と使い方があります。まず、丹銅は銅が主成分で、赤い色をしています。これは主に楽器や電気製品に使われます。例えば、トランペットや電線などです。一方、真鍮は銅と亜鉛の合金で、黄色っぽい色をしています。真鍮は装飾品や家具の金具に使われることが多いです。例えば、ドアノブやジュエリーなどです。このように、丹銅は音や電気に関するものに、真鍮は美しさや耐久性が求められるものに使われます。丹銅と真鍮はそれぞれの特性を活かして、異なる場面で役立っているのです。
4-3. 真鍮を使用する際のポイント
真鍮と丹銅は、どちらも金属ですが、特性や用途が異なります。まず、真鍮は銅と亜鉛の合金で、丹銅は純粋な銅です。真鍮は、色が明るく、加工しやすいので、楽器や装飾品に使われます。例えば、トランペットやドアノブなどが真鍮で作られています。一方、丹銅は耐久性があり、電気を通しやすいので、電気機器や配線に適しています。具体的には、配電盤や電気ケーブルに使われることが多いです。このように、真鍮と丹銅はそれぞれ異なる特徴を持ち、用途も様々です。どちらの金属も重要ですが、目的に応じて選ぶことが大切です。
まとめ
丹銅と真鍮は、いずれも金属合金ですが、成分と特性が異なります。丹銅は主に銅から成り、優れた導電性と耐腐食性を持ちます。一方、真鍮は銅と亜鉛の合金で、加工性や美しい金色が特徴です。用途は丹銅が電気機器や配管に、真鍮が装飾品や楽器に広く用いられています。それぞれの特性を理解することで、適切な選択が可能になります。
快削黄銅の全貌:特性と実際の用途を詳しく見る
「快削黄銅って一体何?その特徴や使い道が知りたい!」と感じているあなたに向けて、この記事をお届けします。快削黄銅は、金属加工の現場で非常に重要な素材ですが、その特性や具体的な用途について深く理解している方は少ないかもしれません。
このガイドでは、快削黄銅が持つ特異な性質から、実際にどのような分野で利用されているのかまで、詳しく掘り下げていきます。「快削黄銅とは何か?」「その特徴は?」「どんな場面で使われるのか?」といった疑問にお答えし、さらにあなたの知識を広げる情報を提供します。
快削黄銅は、加工が容易で精度の高い部品製造に役立つため、機械工業や電子機器の分野で重宝されています。もし、あなたがこの金属の魅力を理解し、実際の用途を知ることで新たなビジネスチャンスを考えているなら、ぜひこの続きを読み進めてください。快削黄銅の全貌を明らかにし、その可能性を探っていきましょう。
1. 快削黄銅 とは 特徴
1-1. 快削黄銅の定義
快削黄銅とは、加工しやすい特性を持った金属の一種です。主に銅と亜鉛でできており、機械での切削が簡単に行えるため、様々な製品に使われています。例えば、快削黄銅はおもちゃの部品や電気機器のパーツ、さらには水道の蛇口などに使われています。このように、快削黄銅は日常生活の中で多くの場面で役立っています。
快削黄銅の特徴は、加工がしやすいだけでなく、耐腐食性にも優れていることです。これにより、長持ちする製品を作ることができます。快削黄銅はその特性から、私たちの生活を支える重要な材料であり、様々な用途で活躍しています。
1-2. 快削黄銅の主な特徴
快削黄銅は、金属の一種で、特に加工がしやすいという特徴があります。なぜなら、切削や加工をする際に、刃物がスムーズに進むからです。例えば、機械の部品や工具など、精密な形が必要なものに多く使われています。この特性により、製造時間を短縮でき、コストも抑えられます。
具体的には、自動車の部品や電子機器のケースなど、日常生活で目にする製品にも使われています。快削黄銅は、耐腐食性もあり、長持ちするため、様々な場面で重宝されています。
快削黄銅はその加工のしやすさと耐久性から、多くの産業で重要な役割を果たしています。これからも、さまざまな製品での利用が期待される素材です。
2. 快削黄銅 とは 用途
2-1. 快削黄銅の一般的な用途
快削黄銅は、特に加工がしやすい金属で、多くの便利な特徴があります。まず、快削黄銅は非常に柔らかく、切削や加工が簡単です。このため、機械の部品や工具に使われることが多いです。例えば、自動車の部品や電気機器の部品など、精密な形を必要とするものに最適です。また、快削黄銅は耐腐食性にも優れているので、湿気の多い場所でも長持ちします。これらの理由から、多くの工場や企業が快削黄銅を選んでいます。快削黄銅はその加工のしやすさと耐久性から、様々な産業で重要な役割を果たしているのです。
2-2. 特殊用途における快削黄銅の利点
快削黄銅は、特に加工がしやすい金属として知られています。これは、金属の中に含まれる特別な成分によって、切削や加工が簡単にできるからです。たとえば、機械部品や精密な工具を作る際に、快削黄銅を使うと、作業がスムーズに進みます。このような特性から、快削黄銅は自動車や電子機器の部品製造に広く利用されています。さらに、耐腐食性が高いため、長持ちするという利点もあります。快削黄銅を使うことで、製品の品質が向上し、製造コストも削減できるのです。このように、快削黄銅は特別な用途において非常に役立つ素材であり、今後も多くの分野で重要な役割を果たすでしょう。
3. 快削黄銅と一般黄銅の違い
3-1. 機械的性質の違い
快削黄銅は、金属の一種で、特に加工しやすいという特徴があります。これは、工具や機械で簡単に形を変えることができるため、製造業でとても重宝されています。例えば、快削黄銅は、ねじやボルトなどの部品を作るのに使われます。これらの部品は、車や家電製品の中に入っていて、私たちの生活に欠かせないものです。
また、快削黄銅は耐腐食性が高いので、湿気の多い場所でも安心して使えます。このように、快削黄銅は加工のしやすさと耐久性を兼ね備えているため、多くの産業で利用されています。快削黄銅はその特性から、様々な用途で重要な役割を果たしている金属です。
3-2. 加工性の違い
快削黄銅とは、加工しやすい特別な金属のことです。まず、この金属の特徴は、切ったり削ったりするのが簡単で、工具が長持ちする点です。例えば、機械の部品や電気機器の部品を作るときに、とても役立ちます。次に、快削黄銅は耐腐食性があり、長い間使っても錆びにくいです。これにより、屋外で使うものや水に触れるものにも適しています。具体的には、水道の蛇口や自転車の部品などに使われています。快削黄銅はその特性から、さまざまな場所で重宝されており、今後も多くの分野で使われるでしょう。こうした理由から、快削黄銅は非常に重要な材料なのです。
4. 快削黄銅の機械的性質とRoHS対応
4-1. 機械的性質の詳細
快削黄銅とは、加工しやすい特性を持つ金属の一種です。この金属は、特に機械部品や工具の製造に使われます。快削黄銅の特徴は、切削加工が容易で、滑らかな表面を持つことです。これにより、部品を作る際に時間を短縮できるため、製造コストを抑えることができます。
例えば、自動車の部品や電子機器の部品など、さまざまな製品に利用されています。快削黄銅を使うことで、高品質な部品を効率的に生産できるため、多くの企業がこの素材を選んでいます。
快削黄銅はその優れた加工性から、現代の製造業に欠かせない重要な材料です。これにより、さまざまな製品の製造がスムーズに行われています。
4-2. RoHS対応についての情報
快削黄銅は、特別な銅と亜鉛の合金です。この金属の特徴は、加工がとても簡単で、切ったり削ったりするのが楽だということです。だから、工場でたくさんの部品を作るのに向いています。例えば、快削黄銅は、ボルトやナット、電気機器の部品など、さまざまな製品に使われています。
快削黄銅が人気な理由は、加工が早いので作業時間が短くなり、コストを抑えられるからです。これにより、企業は効率よく製品を作ることができます。さらに、耐腐食性も高いので、長持ちする製品を作ることができます。
快削黄銅は加工が簡単で、さまざまな用途に使えるため、非常に便利な素材です。
5. 快削黄銅の加工性と耐久性
5-1. 加工性の特徴
快削黄銅は、金属の一種で、とても加工しやすいという特長があります。このため、さまざまな製品に使われています。例えば、機械の部品や電子機器の部品など、精密な形が必要なものに最適です。快削黄銅は、加工する際に切削がスムーズに行えるため、製造時間を短縮でき、コストも抑えられます。また、耐腐食性も持っているため、長持ちするのも魅力です。
このように、快削黄銅は加工が簡単で、さまざまな用途に使えるため、工業界で非常に重宝されています。今後も、これらの特性を活かして、さらに多くの製品に利用されることでしょう。快削黄銅は、私たちの生活に欠かせない素材の一つと言えます。
5-2. 耐久性の評価
快削黄銅は、特別な銅と亜鉛の合金で、加工がしやすいという特徴があります。この金属は、機械部品や工具の製造に使われています。なぜ快削黄銅が人気かというと、加工が簡単で、丈夫だからです。例えば、快削黄銅で作られたネジやボルトは、しっかりとした強度を持ちながら、製造時間を短縮できます。これにより、コストを抑えつつ高品質な製品を作ることが可能になります。さらに、快削黄銅は耐腐食性もあり、長持ちするため、さまざまな環境で使われています。快削黄銅は加工のしやすさと耐久性から、多くの産業で重宝されている金属です。
まとめ
快削黄銅は、加工性に優れた合金で、主に銅と亜鉛から成り立っています。その特性として、高い耐腐食性や機械的強度があり、精密部品や工具、電子機器の部品に広く使用されています。特に、切削加工が容易なため、効率的な生産が可能です。
六四黄銅の特性徹底解説:物理的特性と化学的特性の比較
六四黄銅、つまり銅と亜鉛の合金は、その独自の特性から多くの産業で重宝されています。しかし、その特徴を正しく理解している方は少ないのではないでしょうか。「六四黄銅の特性について詳しく知りたい」「物理的特性と化学的特性の違いを理解したい」とお考えのあなたに向けて、このガイドをお届けします。
この文章を読むことで、六四黄銅とは何か、その基本的な特性や利点、さらには物理的特性と化学的特性の違いについて深く学ぶことができます。六四黄銅は、強度や耐食性に優れており、さまざまな用途に活用されています。その魅力を知り、あなたのプロジェクトやビジネスに役立ててみませんか?
それでは、六四黄銅の特性を徹底的に解説していきましょう。あなたが知りたかったことがきっと見つかります!
1. 六四黄銅 特徴とは?
1-1. 六四黄銅の基本情報
六四黄銅は、銅と亜鉛を主成分とする合金で、特に64%の銅と36%の亜鉛から成り立っています。この合金の特徴は、優れた耐腐食性と加工性です。例えば、六四黄銅は水道管や電気機器など、さまざまな製品に使われています。なぜなら、錆びにくく、長持ちするからです。また、金属の中でも比較的軽いので、扱いやすいという利点もあります。
このように、六四黄銅は多くの場面で役立つ特性を持っています。耐久性が高く、加工しやすいことから、私たちの生活に欠かせない材料となっています。これからも、さまざまな分野で利用されることでしょう。
1-2. 六四黄銅の化学成分
六四黄銅は、銅と亜鉛を主成分とする合金です。この合金は、特に優れた特性を持っているため、多くの産業で使われています。まず、六四黄銅は耐腐食性が高く、水や空気に強いので、長持ちします。例えば、船の部品や水道管に使われることが多いです。また、加工がしやすく、さまざまな形に成形できるため、工業製品や装飾品にも利用されています。
これらの理由から、六四黄銅は非常に人気があります。特に、耐久性や美しさが求められる場面で重宝されているのです。まとめると、六四黄銅はその特性から多くの分野で重宝されている合金であり、今後も需要が高まることが期待されます。
1-3. 六四黄銅の機械的性質
六四黄銅は、特別な金属で、さまざまな特徴があります。まず、この金属はとても強くて、壊れにくいです。だから、工場や建物の部品として使われることが多いです。次に、六四黄銅は加工がしやすいので、さまざまな形にすることができます。例えば、コインや楽器、さらには装飾品などにも使われています。そして、六四黄銅は錆びにくい性質も持っているため、長い間使っても大丈夫です。このように、六四黄銅は強さ、加工のしやすさ、耐久性という特性を持っているため、多くの場所で利用されています。これらの理由から、六四黄銅はとても大切な金属なのです。
2. 六四黄銅 特徴に基づく加工方法
2-1. 六四黄銅の加工技術
六四黄銅は、銅と亜鉛の合金で、特に66%の銅と34%の亜鉛から成り立っています。この合金の特徴は、強度が高く、耐腐食性にも優れている点です。例えば、六四黄銅は水道管や船の部品として使われることが多いです。理由としては、湿気や塩水に強いため、長持ちするからです。また、加工がしやすく、さまざまな形に作ることができるため、工業製品にも広く利用されています。六四黄銅はその特性から、私たちの生活に欠かせない素材となっているのです。このように、六四黄銅は強さと耐久性を兼ね備えた優れた材料であり、さまざまな場面で活躍しています。
2-2. 六四黄銅の加工時の注意点
六四黄銅は、特別な金属で、銅と亜鉛が主成分です。この金属の特性はとても大切です。まず、六四黄銅は耐腐食性が高く、水や空気に強いです。これにより、長い間使えるため、様々な製品に利用されています。例えば、船の部品や水道管などに使われています。また、加工がしやすく、形を変えやすいのも特徴です。これにより、複雑な形の部品を作ることができます。六四黄銅は美しい金色をしているため、装飾品にも使われています。このように、六四黄銅は強さ、美しさ、加工のしやすさを兼ね備えた金属です。これからも様々な場面で活躍するでしょう。
3. 六四黄銅 特徴と用途
3-1. 六四黄銅の主な用途
六四黄銅は、特に多くの場面で使われる金属です。まず、六四黄銅は非常に強くて丈夫なため、建物のパーツや機械の部品に使われます。例えば、パイプやバルブなど、耐久性が求められるものに適しています。また、見た目も美しいので、装飾品やジュエリーにも利用されます。このように、六四黄銅は強さと美しさを兼ね備えた金属です。
さらに、六四黄銅は耐腐食性が高いので、水の中や湿気の多い場所でも安心して使えます。これが、さまざまな産業での需要を支えています。六四黄銅は、強さ、美しさ、耐久性を持ち、幅広い用途で活躍する重要な素材です。
3-2. 六四黄銅の利点と欠点
六四黄銅は、銅と亜鉛を主成分とする合金で、特に優れた特性を持っています。まず、耐腐食性が高いため、湿気の多い場所でも長持ちします。例えば、海に近い場所で使われる船の部品や水道管などに最適です。また、加工がしやすく、さまざまな形に成形できます。これにより、工業製品や装飾品など、幅広い用途があります。
しかし、欠点もあります。六四黄銅は、強度が他の金属に比べて劣るため、重い負荷がかかる場所には向いていません。例えば、建物の構造材としては不適切です。
六四黄銅は耐腐食性や加工のしやすさが魅力ですが、強度が必要な場面では注意が必要です。用途に応じて使い分けることが大切です。
4. 銅と真鍮の違い
4-1. 銅の特徴と用途
六四黄銅は、銅と亜鉛を主成分とする合金で、特に優れた特性を持っています。まず、耐腐食性が高く、水や空気に強いため、さまざまな環境で使えます。例えば、配管や電気機器の部品に利用されています。また、加工がしやすく、さまざまな形に成形できるため、工業製品としても人気です。
さらに、六四黄銅は美しい金色の光沢を持っているため、装飾品やアクセサリーにも使われます。このように、六四黄銅は実用性と美しさを兼ね備えた材料です。
六四黄銅はその特性から多くの分野で重宝されており、私たちの生活に欠かせない素材の一つと言えます。
4-2. 真鍮の特徴と用途
真鍮は金属の一種で、特に銅と亜鉛を混ぜて作られます。真鍮の特徴は、見た目が美しく、耐腐食性が高いことです。これは、真鍮が水や空気に強いからです。例えば、真鍮で作られたドアノブや楽器は、長い間使っても錆びにくく、見た目も良いので人気です。
また、真鍮は加工がしやすく、さまざまな形に変えることができます。これにより、家具や装飾品、さらには電子機器の部品としても使われています。真鍮は、ただの金属ではなく、私たちの生活に多くの便利さをもたらしているのです。
つまり、真鍮は美しさと強さを兼ね備えた金属で、さまざまな用途があるため、私たちの生活に欠かせない存在です。
4-3. 銅と真鍮の比較
六四黄銅は、銅と亜鉛を主成分とした合金で、特に優れた特性を持っています。まず、その理由は耐腐食性が高く、長持ちするからです。例えば、海の近くにある設備でも、六四黄銅は錆びにくく、安心して使えます。また、加工がしやすく、さまざまな形に作ることができるため、工業製品や装飾品にも広く利用されています。さらに、電気伝導性が良いので、電気製品にも使用されています。このように、六四黄銅は多くの場面で役立つ材料です。六四黄銅はその特性から、日常生活や産業に欠かせない重要な素材であると言えます。
まとめ
六四黄銅は、銅と亜鉛を主成分とする合金で、優れた機械的強度と耐腐食性を持ちます。物理的特性では、優れた加工性と耐摩耗性が際立ち、化学的特性では、酸や塩基に対する耐性が重要です。これにより、六四黄銅は多様な産業で広く利用されています。
七三黄銅の特徴と他の素材との違いを比較
あなたは「七三黄銅について知りたいけれど、どこから始めればいいのかわからない」とお悩みではありませんか?そんな方のために、私たちは「七三黄銅の完全ガイド」を用意しました。
この記事は、以下のような疑問を持つあなたにぴったりです。
- 七三黄銅とは何か、どんな特徴があるのか?
- 七三黄銅は他の金属や素材とどう違うのか?
- 七三黄銅を使用するメリットとデメリットは何か?
- 七三黄銅を実際に使ってみたいけれど、どんな場面で役立つのか知りたい!
七三黄銅はその優れた特性から多くの分野で用いられていますが、その魅力を理解するためには、しっかりとした知識が必要です。本記事では、七三黄銅の基本的な情報から、他の素材との具体的な比較まで、幅広く解説していきます。これを読めば、七三黄銅の世界がぐっと身近に感じられることでしょう。さあ、一緒に七三黄銅の魅力を探ってみましょう!
1. 七三黄銅 特徴とは?
1-1. 七三黄銅の基本情報
七三黄銅は、銅と亜鉛を主成分とする合金で、特に銅が70%、亜鉛が30%の割合で含まれています。この素材の特徴は、耐腐食性が高く、加工がしやすいことです。例えば、七三黄銅は水道管や電気機器の部品に使われることが多いです。なぜなら、水や電気に強く、長持ちするからです。
他の素材と比べると、例えばステンレス鋼はもっと硬くて丈夫ですが、加工が難しいことがあります。また、アルミニウムは軽いですが、強度が劣ることがあります。七三黄銅は、これらの良いところを持ち合わせているのです。
このように、七三黄銅は様々な利点を持つため、多くの場面で利用されています。だからこそ、工業や日常生活でとても重要な素材なのです。
1-2. 七三黄銅の化学成分
七三黄銅は、銅と亜鉛を主成分とする合金で、その特徴はとても優れています。まず、七三黄銅は耐腐食性が高く、水や空気に強いため、長持ちします。例えば、海の近くの建物や配管に使われることが多いです。また、加工がしやすく、さまざまな形に成形できるため、工業製品や装飾品にも利用されています。
さらに、七三黄銅は美しい金色の光沢を持っており、見た目が良いことからジュエリーや楽器にも使われます。このように、七三黄銅は耐久性と美しさを兼ね備えた素材です。
七三黄銅はその特性から多くの分野で重宝されており、他の素材と比べても非常に魅力的な選択肢となっています。
1-3. 七三黄銅の物理的特性
七三黄銅は、銅と亜鉛を主成分とする合金で、特に73%が銅、27%が亜鉛で構成されています。この合金の特徴は、強度が高く、耐腐食性にも優れていることです。例えば、七三黄銅は水道管や楽器の部品に使われています。これは、長持ちするため、安心して使えるからです。また、加工がしやすく、さまざまな形に成型できるため、工業製品にも広く利用されています。さらに、七三黄銅は見た目も美しく、金色の光沢があるため、装飾品にも適しています。このように、七三黄銅はその特性から多くの分野で重宝されており、他の素材と比較しても非常に優れた選択肢と言えるでしょう。
2. C2680の材質と性質
2-1. C2680の成分と特徴
七三黄銅は、銅と亜鉛の合金で、特に耐腐食性に優れています。この素材の特徴は、強度が高く、加工もしやすいことです。そのため、様々な製品に利用されています。例えば、配管や電気機器の部品など、日常生活でもよく見かけるものです。
他の素材と比較すると、七三黄銅は特に耐久性が高い点が魅力です。例えば、アルミニウムは軽いですが、強度が劣りますし、鉄は頑丈ですが、錆びやすいです。七三黄銅は、そのバランスが優れているため、多くの場面で選ばれています。
七三黄銅はその特性から非常に使いやすい素材です。これからも、様々な製品で活躍し続けるでしょう。
2-2. C2680の機械的特性
七三黄銅は、銅と亜鉛を主成分とする合金で、特に耐腐食性や加工性に優れています。まず、七三黄銅の特徴は、その強度と柔らかさのバランスが良いことです。このため、さまざまな形に加工しやすく、日常生活の中でよく使われています。例えば、硬貨や配管、楽器の部品などに使われています。
他の素材と比べると、例えばステンレス鋼は錆びにくいですが、加工が難しいです。一方、七三黄銅は加工が簡単で、見た目も美しいため、装飾品にも適しています。このように、七三黄銅は特に便利で使いやすい素材です。
七三黄銅はその特性から多くの場面で重宝されており、他の素材と比べても優れた選択肢と言えます。
2-3. C2680の用途と利点
七三黄銅は、特に優れた特徴を持つ金属です。まず、耐腐食性が高く、長持ちするため、さまざまな製品に使われています。例えば、銅製の配管や電気機器に多く使われており、これは水や電気に強いからです。また、七三黄銅は加工がしやすく、さまざまな形にすることができます。これにより、デザイン性のある製品も作りやすくなります。
他の金属と比べると、七三黄銅は軽量でありながら強度があるため、特に人気があります。たとえば、航空機の部品や自動車の部品にも利用されています。このように、七三黄銅は多くの利点を持ち、様々な場面で活躍しています。これらの理由から、七三黄銅は非常に重要な素材と言えるでしょう。
3. 銅合金の種類と用途
3-1. 銅合金の基本的な分類
七三黄銅は、銅と亜鉛が主成分の合金で、特に耐食性や加工性に優れています。この素材の特徴は、強度が高く、さびにくいことです。これにより、さまざまな製品に使われています。例えば、七三黄銅は水道管や電子機器の部品に利用されており、長持ちするため、多くの人に選ばれています。
他の素材と比べると、例えばアルミニウムは軽いですが、強度が劣ります。また、ステンレス鋼は強いですが、加工が難しいことがあります。七三黄銅は、そのバランスの良さから多くの場面で重宝されています。
七三黄銅は優れた特性を持ち、他の素材と比べても魅力的な選択肢です。これからも、さまざまな分野で活躍することでしょう。
3-2. 各種銅合金の特徴
七三黄銅は、銅と亜鉛を主成分とした合金で、特に耐腐食性や加工のしやすさが特徴です。これらの特性から、七三黄銅は配管や電気機器、さらには楽器の製造にも使われています。例えば、七三黄銅で作られた楽器は、音色が豊かで美しい音を出すため、多くのミュージシャンに好まれています。
他の素材と比べると、七三黄銅は強度が高く、長持ちするため、日常生活でも安心して使えます。例えば、アルミニウムや鉄に比べて、錆びにくいという利点があります。
このように、七三黄銅はその特性から多くの場面で利用されており、非常に価値のある素材と言えます。これからも様々な分野でその魅力が発揮されるでしょう。
3-3. 銅合金の産業での利用例
七三黄銅は、銅と亜鉛の合金で、特に耐腐食性や加工のしやすさが特徴です。この素材は、さまざまな産業で利用されています。例えば、配管や電気機器、さらには楽器の製造にも使われています。七三黄銅は、他の金属と比べて軽く、強度も高いため、長持ちします。また、見た目も美しい金色をしているため、装飾品にも適しています。
このように、七三黄銅は多くの利点があり、さまざまな場面で活躍しています。例えば、楽器のトランペットは、音色が良くなるために七三黄銅が使われています。このように、実用性と美しさを兼ね備えた素材として、七三黄銅は非常に重要です。だからこそ、私たちはこの素材の特性を理解し、活用していくことが大切です。
4. 銅と真鍮の違い
4-1. 銅と真鍮の成分の違い
七三黄銅は、銅と亜鉛を主成分とする合金で、特に銅が70%、亜鉛が30%の割合で含まれています。この素材の特徴は、耐腐食性が高く、加工がしやすいことです。例えば、七三黄銅は水道管や電気配線に使われることが多いです。これは、長持ちし、錆びにくいからです。
他の素材と比べると、アルミニウムよりも強度が高く、ステンレスよりも軽いのが特徴です。これにより、様々な用途に適しているのです。例えば、七三黄銅は楽器や装飾品にも使われ、見た目も美しいです。
七三黄銅はその優れた特性から、多くの分野で重宝されている素材です。
4-2. 銅と真鍮の物理的特性の比較
七三黄銅は、銅と亜鉛を主成分とする合金で、特に耐腐食性や加工性に優れています。この素材の特徴は、金属の中でも強度が高く、さびにくいため、さまざまな製品に使われています。例えば、七三黄銅は水道の配管や楽器の製造に使われることが多いです。このように、七三黄銅は他の素材と比べて耐久性が高く、長持ちするため、選ばれることが多いのです。
さらに、七三黄銅は加工がしやすく、さまざまな形に成形できます。これに対して、鉄などは重くて加工が難しいことがあります。つまり、七三黄銅は使いやすく、生活の中で役立つ素材と言えるでしょう。これらの理由から、七三黄銅は多くの場面で重宝されています。
4-3. 銅と真鍮の用途の違い
七三黄銅は、銅と亜鉛を主成分とする合金で、特に耐食性や加工性に優れています。この素材は、主に配管や電気機器、さらには楽器などに使われています。七三黄銅の特徴は、強度が高く、金属の中でも軽いことです。例えば、楽器のトランペットにはこの素材が使われており、音色が美しく響きます。
他の素材と比べると、七三黄銅は錆びにくいので、屋外での使用にも適しています。アルミニウムや鉄と比べると、耐久性が高く、長持ちします。これにより、長期間にわたって安心して使用できるのです。
七三黄銅はその優れた特性から多くの用途で重宝されており、他の金属素材と比べても非常に魅力的な選択肢となっています。
5. 真鍮の加工方法と注意点
5-1. 真鍮の加工技術
七三黄銅は、特に優れた特徴を持つ金属です。この金属は、70%の銅と30%の亜鉛からできており、強度が高く、耐腐食性にも優れています。例えば、七三黄銅は水道管や電気機器の部品に使われることが多いです。これは、湿気や水に強いからです。
他の金属と比べると、七三黄銅は加工がしやすく、さまざまな形にすることができます。たとえば、複雑な形の部品も作りやすいので、工業製品に適しています。
七三黄銅は強さや耐腐食性、加工のしやすさから、多くの場面で使われています。この金属の特徴を理解することで、私たちの生活にどのように役立っているかがわかります。
5-2. 真鍮加工時の注意点
七三黄銅は、銅と亜鉛を主成分とする合金で、特に耐腐食性が高く、加工がしやすいという特徴があります。このため、さまざまな製品に利用されています。例えば、楽器や配管、さらには装飾品など、幅広い分野で使われています。
他の素材と比べると、七三黄銅は強度がありながらも軽量で、見た目も美しいため、人気があります。例えば、ステンレス鋼は耐久性が高いですが、重くて加工が難しいことがあります。それに対して、七三黄銅は扱いやすく、デザインの自由度が高いのです。
まとめると、七三黄銅はその優れた特性から、多くの場面で重宝されています。これからも、様々な製品に使われ続けることでしょう。
5-3. 真鍮のメンテナンス方法
七三黄銅は、特に耐久性と美しさで知られる金属です。この素材は、70%の銅と30%の亜鉛からできており、強度が高く、腐食にも強いのが特徴です。例えば、七三黄銅で作られた水道の蛇口や装飾品は、長い間使っても劣化しにくいです。このため、家庭や工業用として非常に人気があります。
他の素材と比べると、七三黄銅は見た目も美しく、金色の輝きが魅力的です。また、鉄やアルミニウムよりも軽く、扱いやすいのも利点です。これらの理由から、七三黄銅は多くの人に選ばれています。
七三黄銅は耐久性と美しさを兼ね備えた素晴らしい素材であり、さまざまな用途に適しています。
まとめ
七三黄銅は、銅と亜鉛の合金で、耐腐食性と加工性に優れています。特に、機械部品や配管に多く使用されます。他の素材と比較すると、アルミニウムよりも強度が高く、ステンレスよりも軽量でコスト効率が良い点が特徴です。これにより、多様な産業で重宝されています。
丹銅と他の金属との違い〜あなたが知らない特性とは〜
「丹銅」という言葉を聞いたことがありますか?しかし、丹銅がどのような金属で、他の金属と何が違うのかを理解している人は意外と少ないかもしれません。この金属は、実はその特異な特性から多くの分野で重宝されています。
本記事では、「丹銅とは何か?」という基本的な疑問から、丹銅の特性、利用方法、そして他の金属との違いについて詳しく解説します。例えば、丹銅は優れた導電性を持ちながらも、耐腐食性や加工性に優れているといった特徴があります。また、どのような場面で丹銅が利用されているのかを知ることで、あなたの日常生活や仕事に役立つかもしれません。
金属の世界は奥が深く、丹銅の特性を理解することで、新たな視点や発見が得られるはずです。それでは、丹銅の魅力に迫ってみましょう!
1. 丹銅 とは何か
1-1. 丹銅の定義と歴史
丹銅とは、銅とスズを混ぜた金属のことです。丹銅は特別な性質を持っており、他の金属と比べて優れた特徴があります。理由は、丹銅が耐食性に優れ、加工しやすいからです。例えば、古代の日本では、丹銅は武器や道具、装飾品に使われていました。このように、丹銅は長い歴史を持ち、実用的な用途がたくさんあります。また、丹銅は美しい色合いを持つため、アートやジュエリーにも利用されています。丹銅はその特性から、他の金属とは一線を画す存在であり、私たちの生活に深く関わっています。丹銅の魅力を知ることで、もっと身近に感じることができるでしょう。
1-2. 丹銅の特性
丹銅とは、銅に少量の他の金属を混ぜて作られた特別な金属です。丹銅の特性はとてもユニークで、他の金属とは違った魅力があります。まず、丹銅は非常に強く、耐久性があります。これにより、長い間使用することができるのです。例えば、丹銅で作られた楽器や装飾品は、長い時間美しさを保ちます。
また、丹銅は抗菌性があり、細菌が繁殖しにくいという特性も持っています。これが、医療器具や飲食器に使われる理由です。丹銅は見た目が美しく、色合いが温かみを感じさせるため、多くの人に愛されています。
このように、丹銅はその強さや美しさ、そして衛生面での特性から、他の金属とは一線を画す存在です。
2. 丹銅 とは他の金属との違い
2-1. 丹銅と銅の違い
丹銅とは、銅に少しの他の金属を加えたものです。結論から言うと、丹銅は普通の銅よりも強く、耐久性があります。この理由は、他の金属を加えることで銅の性質が変わるからです。例えば、丹銅はよく使われる楽器や装飾品に使われます。楽器の場合、音がきれいに響くので、多くの音楽家に好まれています。また、装飾品では、光沢が美しく、長持ちするため、人気があります。丹銅は普通の銅よりも優れた特性を持っているため、さまざまな場面で利用されています。これが、丹銅が特別な金属である理由です。
2-2. 丹銅とアルミニウムの比較
丹銅とは、銅に少量のスズを加えた金属のことです。丹銅はとても強く、耐久性があります。この特性から、丹銅はさまざまな用途で使われています。例えば、楽器や美術品、さらには建築材料としても利用されます。丹銅は、アルミニウムと比べると重く、強度が高いため、特に壊れにくいという利点があります。アルミニウムは軽くて加工しやすいですが、強度では丹銅に劣ります。このように、丹銅は特定の用途において非常に優れた特性を持っています。丹銅はその強さと耐久性から、特別な用途に適した金属であり、私たちの生活の中で重要な役割を果たしています。
2-3. 丹銅とステンレスの特性比較
丹銅とは、銅と少量の他の金属を混ぜた特別な金属です。丹銅は、非常に優れた特性を持っており、特に耐久性と導電性が高いのが特徴です。例えば、丹銅は電気をよく通すため、電気機器の部品によく使われます。一方、ステンレスは錆びにくいですが、導電性は丹銅ほどではありません。このように、丹銅は特に電気関連の用途に適しています。
また、丹銅は加工がしやすく、様々な形に成形できるため、工芸品や楽器にも利用されています。例えば、トランペットの一部は丹銅で作られています。このように、丹銅は独自の特性を持ち、特定の分野で非常に役立つ金属なのです。丹銅はそのユニークな性質から、私たちの生活に欠かせない存在と言えるでしょう。
3. 丹銅 とは製造方法とプロセス
3-1. 丹銅の製造工程
丹銅とは、銅に少量のスズを加えた合金です。丹銅の特性は、耐腐食性や強度が高いことです。このため、丹銅はさまざまな用途で使われています。例えば、楽器や装飾品、さらには機械部品などに利用されることがあります。
他の金属と比べると、丹銅は特に音の響きが良いです。これは、スズが加わることで音の質が向上するからです。また、丹銅は見た目も美しく、金色に近い光沢があります。これが、芸術作品や高級な商品に使われる理由です。
丹銅はその特性から非常に多様な用途があり、他の金属とは違った魅力を持っています。丹銅の特性を知ることで、私たちはその価値をより深く理解できるでしょう。
3-2. 丹銅の合金化プロセス
丹銅とは、銅に少量のスズを加えた金属のことです。丹銅の特性は、他の金属と比べてとてもユニークです。まず、丹銅は耐腐食性が高く、長持ちすることが大きな特徴です。理由は、スズが銅の酸化を防ぎ、湿気や空気から守るからです。具体例として、丹銅は楽器や装飾品に使われることが多いです。たとえば、トランペットやサクソフォンの一部は丹銅で作られており、音色が良く、見た目も美しいです。このように、丹銅はただの金属ではなく、私たちの生活に役立つ特別な素材です。丹銅の特性を理解することで、私たちはその魅力をもっと知ることができます。
4. 丹銅 とは金属リサイクルにおける役割
4-1. 丹銅のリサイクルプロセス
丹銅は、銅とスズの合金で、特別な特性を持っています。まず、丹銅はとても強くて耐久性があります。これは、建物や楽器など、長持ちするものに使われる理由です。たとえば、丹銅で作られた楽器は、音色が美しく、演奏者に愛されています。また、丹銅は抗菌性もあり、バイ菌がつきにくいので、衛生的です。この特性から、医療器具や食品に関わる道具にも使われています。さらに、丹銅は他の金属と比べて錆びにくいので、屋外の製品にも適しています。つまり、丹銅は強さ、衛生面、耐久性から多くの場面で重宝されています。これらの特性から、丹銅はとても重要な金属だと言えるでしょう。
4-2. 環境への影響と利点
丹銅とは、銅と他の金属を混ぜて作られた特別な金属です。丹銅はとても強く、耐久性が高いという特性があります。これは、丹銅が銅の良さを保ちながら、他の金属の特性も取り入れているからです。例えば、丹銅は電気をよく通すため、電気機器に使われることが多いです。また、錆びにくいので、屋外の装飾品や楽器にも使われています。このように、丹銅はさまざまな場面で役立っており、私たちの生活を便利にしています。丹銅の特性を理解することで、私たちはその重要性を知り、より良い選択ができるようになります。
5. 丹銅 とは使用される製品
5-1. 丹銅を使用した工業製品
丹銅とは、銅に少量の他の金属を混ぜた特別な金属です。丹銅は、普通の銅とは違って、強さや耐久性が高いのが特徴です。例えば、丹銅は電気をよく通すので、電気機器や配線に使われます。また、耐腐食性もあり、湿気の多い場所でも劣化しにくいです。これにより、丹銅は水道管や屋外の設備にも適しています。さらに、丹銅は加工しやすいので、さまざまな形に作ることができます。これらの特性から、丹銅は工業製品にとても重要な材料となっています。丹銅はその優れた特性により、私たちの生活に欠かせない金属であると言えます。
5-2. 丹銅のアートと装飾品
丹銅とは、銅とスズの合金で、特に美しい色合いが特徴です。この金属は、アートや装飾品に使われることが多く、他の金属と比べて独特な魅力を持っています。まず、丹銅は耐久性が高く、長い間色あせません。例えば、丹銅で作られた彫刻やアクセサリーは、時間が経っても美しさを保ちます。また、丹銅は加工がしやすく、細かいデザインが可能です。これにより、アーティストは自由に創作でき、個性的な作品が生まれます。丹銅の温かみのある色合いは、見る人に親しみを感じさせます。このように、丹銅はアートや装飾品において特別な存在であり、その魅力は多くの人に愛されています。
まとめ
丹銅は銅とスズの合金で、耐腐食性や耐摩耗性に優れています。特に、電気伝導性が高く、加工が容易なため、さまざまな産業で利用されています。また、丹銅は抗菌性も持ち、医療器具や食品関連の用途に適しています。他の金属と比べて、独自の特性が多く、特に美しい色合いが魅力です。